Прокатный станок своими руками: методы и технологии изготовления
Рассмотрим наглядный пример, как можно сделать прокатный станок своими руками: методы и технологии его изготовления. Но прежде всего, необходимо понять для какой цели этот станок нам потребуется.
Достаточно сложно представить современную повседневную жизнь без металла. Он используется повсеместно, и требует для обработки соответствующего оборудования. Металлургическая промышленность в основном использует современные прокатные станки, которые, в свою очередь, имеют высокую цену. Для самостоятельного же использования и изготовления профтрубы, можно сконструировать прокатно-вырубной станок своими силами.
Для чего используется такое оборудование?
Прокатно-вырубные станки и иная техника для металлообработки чаще всего используется при создании конкретной формы металлической детали. Так как этот материал используется повсеместно, к его обработке подходят с надлежащей ответственностью и вниманием.
Прокатные станки для металлического профиля распространены повсеместно, однако многие и не догадываются, что сделать такое сложное оборудование можно самостоятельно. В силу того, что цена на подобное оборудование крайне высокая, мы наглядно рассмотрим пример, как своими руками изготовить прокатно-вырубной механический станок.
Ярким примером металлических деталей, где при изготовлении используется прокатный станок для профильных труб, являются присутствующие в каждом доме или квартире трубы или радиаторы батарей. Все эти изделия изготавливаются на металлообрабатывающем оборудовании, которое в силу изготовить самостоятельно без каких-либо навыков и глубоких познаний.
Важно: если вы решили самостоятельно изготовить прокатно-высечной тип станка, то для надежности последующих изготавливаемых на нем деталей, к его сборке следует отнестись с надлежащим вниманием и ответственностью.
Разновидности прокатного станка
Как уже стало ясно из ранее сказанного, прокатное оборудование необходимо для переработки металлической заготовки в готовую геометрически сформированную деталь. В данном случае для листового металла используются следующие типы оборудования:
- Непрерывно-удлинительные, которые позволяют изготавливать металлические трубы с сечением в 110 мм.
- Пилигримовые станки, что используются при изготовлении массивных труб с диаметром от 400 до 700 мм.
- Короткоправочные модели оборудования, что используются при производстве бесшовных труб диаметром до 450 мм.
- Станки трехвалового типа, которые, в свою очередь, применяются для выполнения толстостенных труб, диаметр которых может достигать 200 мм. Нередко такой тип оборудования называют ювелирным прокатным станком.
Важно: на современных заводах металлообработки также нередко применяются широкопрофильные модели гибочной системы установок, что позволяет изготавливать профильные трубы общей длиной до 3 метров.
Составные детали оборудования
Как правило, в состав любого прокатного станка входят три основных составляющих компонента, а именно:
- рабочие клетки;
- передаточные устройства;
- электрические двигатели.
Валы куда помещаются металлические составляющие будущей детали входят в состав рабочей клетки. Также в эту составляющую входят следующие элементы: установочные механизмы, станины, плитовины, а также проводки. За движение всех составляющих компонентов прокатного станка отвечают мощные электродвигатели. Они соединяются с рабочими элементами при помощи муфт, передаточных элементов и шпинделей.
Важно: основной составляющей прокатного оборудования обжимного и заготовочного типа является диаметр вала, а именно величина его рабочей поверхности.
Современные металлообрабатывающие станки могут иметь сразу несколько рабочих клетей, это необходимо для изготовления деталей сложной геометрической формы. Нередко его называют станок для гусиных лапок, что позволяет выполнять работу сразу в нескольких проекциях.
Как правило, такие устройства имеют внушительные габариты и могут обеспечивать рабочую поверхность до 3 метров. Отличительной особенностью современных прокатных станков является работа сразу в трех направлениях для:
- Изготовления отверстий в металлическом листе.
- Вытяжки заготовки в трубу.
- Калибровка изделия, что позволяет задавать диаметр будущей детали.
Важно: работу на прокатном станке может осуществлять лишь квалифицированный специалист, который прошел инструктаж по технике безопасности.
Изготовление прокатной установки своими руками
Для профильной трубы своими руками потребуется изготовить небольшой станок, который существенно отличается от промышленных установок по размерам. Это возможно сделать в повседневных условиях при наличии под станок свободного пространства.
При этом можно отметить, что самодельный станок может позволить вам изготовить детали любой сложности. При его помощи вы достаточно легко сможете сделать проволоку любого диаметра, нарезать листовой металл, что предусматривает кровельное покрытие любой крыши, а также множество иных деталей, что часто востребованы в повседневном быту.
Предварительно вам потребуется подобрать подходящие чертежи, чтобы у вас получился самодельный прокатный станок. После этого предстоит подготовить его компоненты, а именно:
- пара мощных стоек из крепкого металла;
- прут из стали, чей диаметр будет не меньше 5 см;
- верхняя плита с гайками М10;
- две шестерни соответствующего размера;
- зубчатое колесо;
- пружины и упоры;
- а также бронзовые подшипники и втулки.
После того как все компоненты у вас имеются в наличии, можно приступать к изготовлению рабочего станка, который при этом будет достаточно мобильный к перемещению:
- При помощи болтов из стоек и металлической плиты собирается некое подобие рабочей клети.
- К этим же стойкам монтируются два рабочих вала. Их предварительно следует выточить из ранее приготовленного стального прута. Также их необходимо закалить, чтобы получить улучшенную прочность металла.
- Нижний вал монтируется между стоек при помощи подготовленных втулок и подшипников. Верхний вал при этом монтируется на специальные ползуны и является подвижным элементом станка. Движение вверх ползунов ограничивается упорами.
- Непрерывное сжатие двух отдельных валов обеспечивается за счет пружины, что удерживает их в постоянном напряжении. Она крепится одновременно к плите, основаниям и непосредственно подвижному верхнему валу.
Важно: для обеспечения работы такого станка необходимо синхронное вращение рабочих валов. Решить эту задачу вы можете при помощи зубчатой передачи, что передает вращающий момент шестерне, которая установлена на нижний вал. Таким образом, при помощи рукояти можно запустить в работу устройство.
Сделанная таким образом установка имеет ручной привод. Для ее работы требуется непрерывное вращение. Если ручной механизм остановится, то соответственно и валы перестанут свое вращение. Таким образом, получается универсальное устройство, на котором можно менять компоненты и тем самым изменять профильную пригодность станка.
Плюсы самодельного устройства
В конечном счете все, что вам потребуется для изготовления такого универсального устройства, можно купить по небольшой стоимости в любом строительном магазине либо подобрать нужные компоненты из старых давно забытых вещей, а также подобрать чертежи. В любом случае цена такого станка очень быстро себя окупит, так как изготовить на нем можно детали любой сложности с минимальными затратами на расходный материал.
Важно: аренда прокатного станка обойдется в круглую сумму, из-за чего вы можете размещать объявления и неплохо зарабатывать на своем устройстве.
Сделанная работа достаточно быстро окупается, так как вы можете изготавливать любые детали. Вот лишь небольшой их список:
- профтрубы;
- металлические направляющие для профиля под гипсокартон;
- покрытия для фальцевой кровли;
- элементы для металлосайдинга;
- металлические листы квадратной и прямоугольной формы;
- дополнительные крепления для сайдинга;
- провод для электрической проводки.
Все эти самоделки пригодятся вам при строительстве нового дома или его ремонте. Как показывает практика, листогибочные самодельные станки крайне востребованы, так как их схема не требует сложного изготовления, но при этом позволяет изготавливать массу полезных и нужных деталей.
Видео: прокатный станок своими руками.
Итоги
Таким образом, вручную вы можете сделать прекрасный станок для фальцевания кровельных листов и иных конструкций с минимальными вложениями и трудозатратами, при этом вам больше никогда не потребуется арендовать листогибочные станки или какого-либо иного оборудования для металлообработки.
Настоящие мастера ювелиры уже давно подрабатывают, таким образом, имея стабильную прибыльную подработку, или используют свое самодельное оборудование в качестве основного источника дохода.
metmastanki.ru
Технологии и ремесла | Полезное своими руками
1) Способы изготовления искусственных цветов по виду неотличимых от живых.
2) Технология декоративной обработки органического стекла и плексигласа.
3) Технология восстановления эмалированного слоя, гладкой глянцевой поверхности и однородного цветового покрытия с устранением микротрещин на ваннах, раковинах, унитазах, посуде. С описанием нескольких способов. Специального оборудования и дефицитных материалов не требуется. После реставрации ванны и раковины выглядят как новые.
4) «Работа со стеклом» — декоративная отделка и живопись на стекле: травление, матирование, опаловое стекло, орнамент на стекле, стеклянные витражи, изготовление и ремонт зеркал, Декоративная обработка стекла под хрусталь; под мрамор; декоративно-художественное травление стекла (фотохимический способ) /фотография или рисунок на стекле/; фигурная резка стекла без алмаза (любые конфигурации: по кругу, вдоль и поперек), приготовление жидкого стекла (вассерглас), приспособление к электродрели для сверления отверстий в стекле, закалка стекла и мн.др. Возможно коммерческое применение с хорошим доходом. Брошюра.
5) Способ защиты стекол от механического разрушения (разбивания). При прямом попадании камней, ударов по стеклу палками и железками стекла не разбиваются. Уникальная технология. Возможно коммерческое применение, а заказчики будут из киосков, офисов, различных служебных помещений, в квартирах, на дачах, в теплицах и т.д.
6) «ОРИГАМИ» — японское искусство изготовления чудесных фигурок из обычной бумаги.
7) Обработка дерева: Имитация ценных пород под: светлый дуб, темный дуб, серый клен, орех, под красное, черное, розовое дерево, полисандровое, кипарисовое. Золочение, серебрение, бронзирование дерева. Обработка от загнивания и огнеупорная. Способы изготовления изделий из древесных опилок по типу ДСП и многое другое.
8) Пособие «Декоративная резьба по дереву» — старинное русское ремесло.
9) «Плетение из бересты» Способы изготовления декоративно-художественных изделий: обложки туеса, футляры, лукошки, подстаканники, сумочки, пестери, бутылки, фляжки и др.
10) «Плетение из соломы, хмеля, мочала, пеньки, куга»- бытовых и сувенирных изделий.
11) Производство гончарных изделий (домашний цех): обработка глиняной массы, сушка и обжиг приготовление глазури (12 рецептов цветов и оттенков). Тарракотовые изделия.
12) «Шликерное литье» — метод массового изготовления изделий из глины (скульптурки, статуэтки, поделки, игрушки, фигурки, посуда, панно и многое другое).
13) «ДЫМКОВСКАЯ ИГРУШКА» — Способы изготовления различных сувениров из глины.
14) «ЛЕПНИНА» — старинная технология отделки помещений, офисов, коттеджей, учреждений и др. в стиле «ампир», «модерн», «ретро» — Это сейчас очень прибыльный вид бизнеса.
15) Работа с гипсом. Как придать твердость гипсу. Способы изготовления статуэток, сувениров, барельефов и декоративных отделочных плиток, багета, рамок и многое другое.
16) Имитация слоновой кости и рога, имитация под черепаху. Изготовление декоративных дорогостоящих сувенирных изделий, пользующихся большим спросом. Простой способ изготовления барельефов, маленьких скульптур, статуэток — не отличающихся по внешнему виду от изделий из слоновой кости. Можно открыть очень прибыльное дело.
17) Работа с металлами: сталь, железо, чугун, медь, бронза, латунь, олово, свинец, цинк, алюминий, серебро, золото, хром, никель и т.д. — способы определения марок и сплавов, совместимость и термическая обработка, гибка, правка, рихтовка, клепка, сварка и паяние, оксидирование, анодирование, фосфатирование, закалка, воронение, науглероживание, травление, полировка, вощение, матирование, патинирование и многое другое. Брошюра.
18) ГАЛЬВАНОПЛАСТИКА: электролитический способ копирования барельефов, медалей, старинных монет, ювелирных декоративных украшений и мн.др. Способы изготовления мемориальных досок Способы металлизации растений, насекомых и других не металлических предметов. Как смастерить простейшую гальваническую ванну для электрохимического окрашивания металлических изделий в любой цвет. Простейшая миниатюрная установка для гальванического покрытия металлических поверхностей и рецепты электролитов для омеднения, никелирования, хромирования, оцинкования, серебрения, золочения. Графитирование, формовка, оксидирование, патинирование, наращивание цветных и драг. металлов и многое другое.
19) ХИМОПЛАСТИКА: способы химического полирования, никелирования, хромирования, золочения, серебрения и декоративного окрашивания металлов (чугуна, стали, меди, латуни, бронзы) и неметаллических предметов (пластмассы, стекла, керамики, дерева и т.д) без применения электрического тока. Новейшая технология применима в домашних условиях.
20) Гальваническая ванна на переменном токе — поможет выполнить электрохимическое травление, нанести на металл узоры, эскизы, рисунки, извлечь серебро из фиксажа и мн.др.
21) «Гравюра на металле» — как делать изображения с микроскопическими призмами отражающими свет, которое производит впечатление рельефности изображения на рисунки.
22) «Ювелирное дело» — это древнейшее ремесло, которое никогда не потеряет свою популярность. Приведены способы изготовления ювелирных изделий на дому. Вы научитесь быстро делать серьги, брошки, подвески, колье, кулоны, кольца, перстни, браслеты, цепочки.
23) Способы изготовления сплавов-имитаций драгоценных металлов: а).Сплавы похожие на золото: Нюрнбергское золото, Золото Тальми, Французское золото, Американское золото, Сплав Айха, Сусальное золото.
24) Сплавы похожие на серебро: Французское серебро, Сплав цинка с серебром, Сплав Рудольфа, Мельхиор.
25) Сплав похожий на платину: «Зубной сплав». Гравирование (нанесение надписей и узоров на драг.изделия). Как отличить настоящее золото и серебро от подделок и мн.др. Стоимость сборника «Имитация драг.металлов».
26) Способы изготовления искусственных драгоценных камней: Аквамарин, Аметист, Авантюрин, Бирюза, Гранат, Изумруд, Коралловые камни, Лазуревые камни, Малахит, Опал, Рубин, Сапфир Турмалин, Топаз, Хризолит, Хризопрас, Янтарь. Искусственный жемчуг и мн.др. Способы изготовления драгоценных изделий, бусы, серьги. Сборник «Имитация драг.камней».
27) «Ремесло художественной обработки металлов» — изготовление объемных декоративных изделий из листового металла (вазочки, подсвечники, оправы, витые гардины и мн.др.).
28) Самый простой способ изготовления чеканок (портреты, рисунки, орнаменты и т.д.)
29) Способы изготовления значков штамповкой: артисты, рок-звезды, футбольные команды, клубы эмблемы, гербы, звери, птицы, партийные значки, символические события и мн.др.
30) ЦИНКОГРАФИЯ: Способы изготовления типографского клише (рисунки, изображения, оригинал — макеты и т.д). Изготовление клише методом химического травления. Изготовление наборных шрифтов, печатей, штампов. Изготовление штампа для размножения рисунков. Способы приготовления разноцветных печатных паст. Методы размножения и копирования и мн.др.
31) ШЕЛКОГРАФИЯ: Способы изготовления сетчатых шаблонов. Отделка изделий герметиком, латексом, виксинт-компаундом, кислотными красителями и мн.др.
32) Способы нанесения объемного и набивного рисунка на ткань (холодный и горячий способы) Область применения самая разнообразная. Очень прибыльное дело.
33) Способы отделки ткани по методу «ПЛИССЕ» и «ГОФРЕ». Отделка ткани по типу «ВАРЕНКА». Расписная отделка на ткани «ПОД БАТИК»: одежда, шторы, шарфы, платки и т.д.
34) Роспись «ПОД ХОХЛОМУ»
35) Уникальный способ изготовления дорогостоящего сувенира «ПАРУСНИК В БУТЫЛКЕ»
36) «Работа с полимерами»: гетинакс, пластик, текстолит, оргстекло, стеклоткань, целлулоид, пластмассы, полистирол, винилпласт, нейлон, капрон, дедерон, акрилат и т.п. — обработка, изготовление художественных поделок и сувениров.
37) Изготовление корочек для удостоверений. Пользующихся большим спросом у малых предприятий, частных фирм, различных политических партий, религиозных организаций и т.д.
38) Способы изготовления полиэтиленовых пакетов, хозяйственных сумочек, красочных упаковочных пакетов и коробок под импортные. Специальные приспособления для проклейки.
39) Способы изготовления сувениров и декоративных поделок из эпоксидной смолы.
40) Настольная литейная (пресс, плавильная печь, литьевая установка) и литьевой прибор для изготовления изделий из пластмасс: игрушки, сувениры, декоративные поделки и мн.др.
41) Способы изготовления сувенирных, декоративных, разноцветных и прозрачных свечей: Выбор экспозиций зависит от вашего воображения: различные зверьки, фигурки, орнаменты, любые абстрактные предметы, елочки, Дед морозы, Снегурочки. Новогодние свечи и т.д.
42) Способы изготовления ажурных цепочек, сережек, кулонов, брелков и мн.др.
43) Как сделать: Фотографию на ткане, на керамике, на пластмассе, на дереве, на металле. Полимерную объемную фотографию за несколько секунд. Рельефную фотографию. Простой способ превращения полутоновой фотографии в штриховой рисунок. Изготовление фототрафаретов. Фотография без фотоаппарата /фотограмма/ и многое другое. Уникальный сборник.
44) Способы извлечения золота, серебра, платины из фотофиксажа, радиодеталей, часов.
45) Бизнес, дающий сотни долларов прибыли. Технология отбора и обработки до товарного вида желчных камней КРС. Адреса за границей и в странах СНГ для сбыта готовых ЖК КРС.
46) Сборник «Лесная замша» — технология переработки и изготовления дефицитной продукции из доступного всем и каждому — гриба тутовика. Очень прибыльное занятие.
47) «СТАРИННЫЕ РЕМЕСЛА» — Объемная резьба по дереву. Контурная резьба. Кудринская резьба. Резьба по Ганчу. Ручное ковроделие. Петельчатый ковер. Войлочный ковер. Безворсовый ковер. Художественное литье олова. Мороз по жести. Ажурное литье. Прорезная береста. Плетение из стружки. Скульптура из соломы. Русские точеные потешки. Русские кружева. Рельеф на коже. Инкрустация из кожи. Мозаика. Керамика. Сграффито. Альфейная роспись или Фрески. Маркетри. Мастичная инкрустация. Инкрустация на дереве, металле, камне, кости. Роспись стекла. Басма.
48) «Дать книге вторую жизнь» — Переплет книг, восстановление блока распавшейся книги, изготовление переплетных крышек, изготовление книг в твердом и мягком переплете, графическое художественное оформление переплета и мн.др. Имея эту технологию, вы сможете не только отреставрировать все свои книги, но и открыть свой доходный бизнес по изготовлению дипломов, рефератов, юбилейных папок с золотым тиснением и т.д.
Скачать сборник «Технологии и ремесла»
electro-shema.ru
Как сделать жидкий камень своими руками: технология, рекомендации по изготовлению
Жидкий камень своими руками сделать довольно просто. Он представляет собой современный отделочный материал, который изготавливается по технологии, позволяющей добиться имитации полученных изделий с внешним видом природного камня. Такое название объясняется тем, что готовый продукт является результатом полимеризации многокомпонентного жидкого состава на основе полиэфирных смол. Полученные материалы используются в разных областях, это могут быть отделочные работы, облицовка фасадов, а также изготовление сантехники. В итоге удается получить следующие изделия:
- скульптуры;
- декоративные фонтаны;
- ступени;
- столешницы;
- ванны.
Используется жидкий камень, своими руками который вы можете изготовить, и для отделки помещений разного назначения. Изделия получаются дешевыми, но очень прочными и пластичными, что порой необходимо. Это верно при облицовке поверхностей с неправильной конфигурацией. Производство можно превратить в прибыльный бизнес.
Изготовление столешницы из жидкого камня
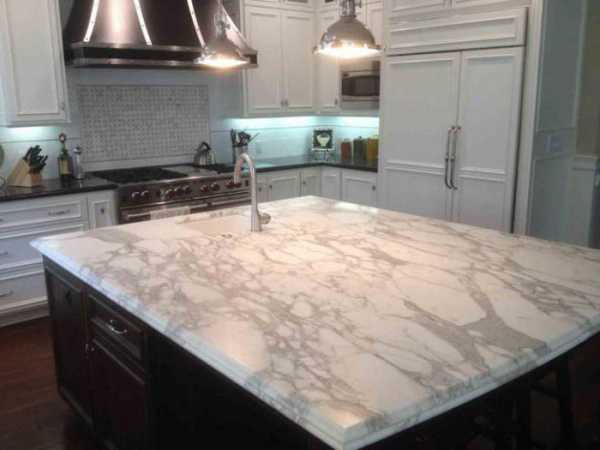
Прежде чем приступать к изготовлению жидкого камня для столешницы, необходимо выполнить форму. Поверхность в итоге должна получиться максимально ровной, поэтому основание следует сделать прочным. Это обусловлено тем, что раствор не должен продавить своим весом материал. Для этого можно использовать листы ДСП, которые устанавливаются на стойки или козлы.
Поверхность основания нужно чем-то накрыть, чтобы после застывания отделить столешницу от ДСП. Отличным решением станет применение полимерной плёнки. Цельный лист устанавливается на несколько козлов, только после можно приступать к изготовлению формы. Ее можно выполнить для нескольких столешниц.
Следующим шагом станет приготовление жидкого камня для столешницы. Для этого можно использовать цементно-песчаную основу, к которой добавляются дополнительные ингредиенты. Это могут быть наполнители в виде песка, а также смолы и мраморной крошки. Предпоследний компонент выступает связующим.
Обзор дополнительных свойств жидкого камня

Полиэфирная смола обычно входит в состав жидкого камня, который представляет собой полимерную композицию. Она является пластмассовой квинтэссенцией. Разные наполнители и составляющие придают этому материалу особые свойства. Стандартные цвета насчитывают около 120 единиц. При необходимости материалу можно придать практически любой цвет, который будет оставаться неизменным в течение длительного времени.
Если добавить к ингредиентам полиэфирную смолу, то поверхность после полимеризации не будет требовать практически никакого ухода, достаточно будет протирать ее мягкой ветошью, смоченной в мыльном растворе. В большинстве случаев такая облицовка используется при облагораживании интерьеров, а также при изготовлении предметов мебели.
Покрытие является полимерным, оно имитирует цвет и фактуру натурального материала, который, в отличие от природного, является более пластичным и тёплым. Из него получаются превосходные столешницы и подоконники, которые могут быть выполнены в имитации бетонной или кирпичной стены.
Камень не выгорает на солнце и обладает повышенным сопротивлением износу. Им отделывают стены возле моек, то есть просто используют взамен обычной плитки. Несмотря на то что такая отделка напоминает гранит, она отличается более доступной стоимостью и меньшей массой. Изделия экологически безопасны, они устойчивы к механическим воздействиям и перепадам температур, не подвергаются коррозии и не покрываются царапинами при интенсивной эксплуатации. В структуре не образуются среды, которые были бы подходящими для возникновения патогенных микроорганизмов. В пласт до полного затвердевания смеси часто добавляются древесные, металлические и стеклянные компоненты. В качестве одного из принципиальных свойств этого материала выступает его дешевизна.
Методы изготовления жидкого гранита
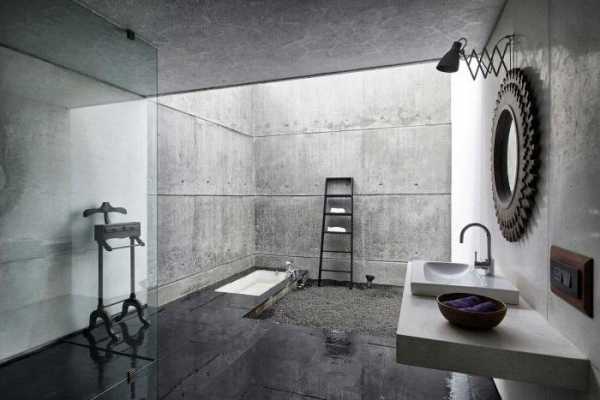
Жидкий гранит может быть выполнен по одной из двух технологий. Первая предусматривает использование методов литья, тогда как вторая предполагает метод напыления. При литье готовая смесь заливается по формам и оставляется до полного высыхания, а затем изделия извлекаются, а на следующем этапе осуществляется их обработка.
Жидкий гранит может быть изготовлен ещё и по методу напыления. В этом случае используется технология распыления на поверхность жидкого камня, толщина слоя не превышает несколько миллиметров. В свою очередь, метод опыления подразделяется еще на два вида:
- прямое напыление;
- обратное напыление.
Первый способ выглядит следующим образом: на заготовку наносится грунт, а после оставляется до момента высыхания. Затем методом распыления на основание наносится слой жидкого камня, осуществляется его шлифовка и полировка, но только после высыхания. Производство жидкого камня может быть выражено в методе обратного напыления. Он используется, если заготовка не является частью предмета мебели.
Изделия укладываются на формовочную поверхность из стекла или ДСП, контуры обводятся, а после устанавливается бортик из пластика или ДСП. На поверхность наносится слой антиадгезива, а затем распыляется жидкий камень. После его частичного затвердевания распыляется грунт, чтобы слой камня не просвечивал. В итоге удается получить форму, куда заливается полиэфирная смола. После полимеризации изделия извлекаются.
Производство жидкого гранита
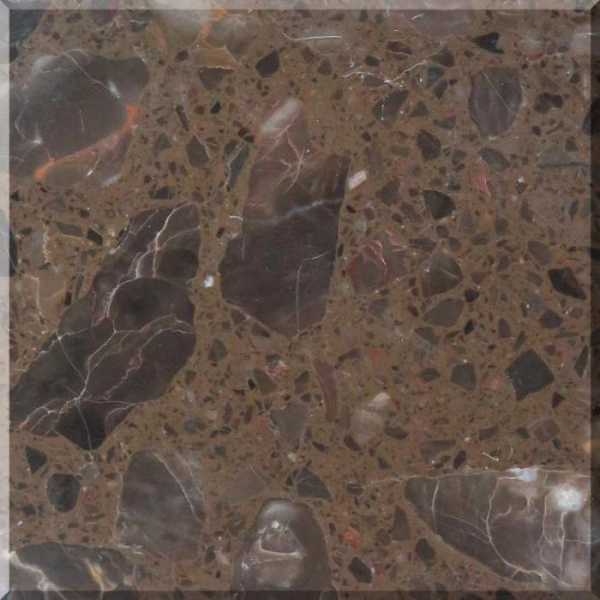
Технология изготовления жидкого гранита предусматривает соблюдение некоторых правил. Первое из них говорит о том, что помещение для производства должно состоять из двух комнат. Первая требуется для литья, тогда как вторая – для шлифовки полученного изделия. Температура поддерживается на уровне 24 °C, обязательна вентиляция.
Производство жидкого камня начинается с обезжиривания поверхности, с неё удаляют пыль и грязь. Перед покрытием основание промывается водой и хорошо просушивается. Все повреждения и трещины должны быть отремонтированы. На следующем этапе подготавливается смесь из прозрачного гелькоута с гранулами. Использовать при этом нужно соотношение 2 к 1. Первый ингредиент представляет собой полимерную смолу. Перед напылением добавляется отвердитель. Полученный состав наносится на основание. Для этого можно использовать один из двух способов, которые были описаны выше. Поверхность нового изделия должна быть отшлифована и отполирована.
Изготовление жидкого мрамора
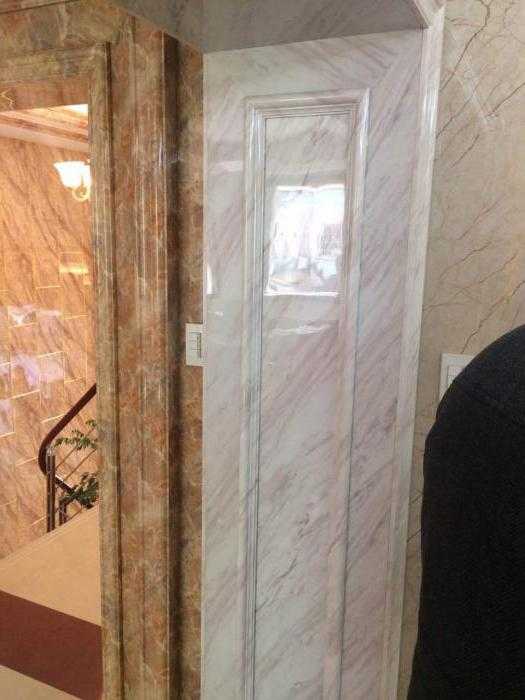
Если вы хотите изготовить жидкий камень своими руками, то можете попытаться сделать мрамор. Он пользуется большой популярностью, что особенно касается литиевой его разновидности. Она представляет собой композитный материал, в основе которого лежит полиэфирная смола. Дополнительным ингредиентом выступает минеральный наполнитель. Впрочем, им может быть кварцевый песок или крошка из мрамора.
В зависимости от того, какие наполнители будут выбраны, мрамор может быть получен в имитации следующих разновидностей камней:
- оникс;
- малахит;
- гранит;
- яшма;
- натуральный мрамор.
Изготавливая жидкий камень своими руками, вы должны знать о нём некоторые особенности. Среди прочих следует выделить то, что материал можно использовать для отделки, а представляет он собой лёгкий, экологичный и гибкий материал с акриловыми полимерами и крошкой из мрамора. Такие изделия можно разрезать даже ножницами или ножом, а также наклеивать на стены вместо обоев.
Дополнительная область использования
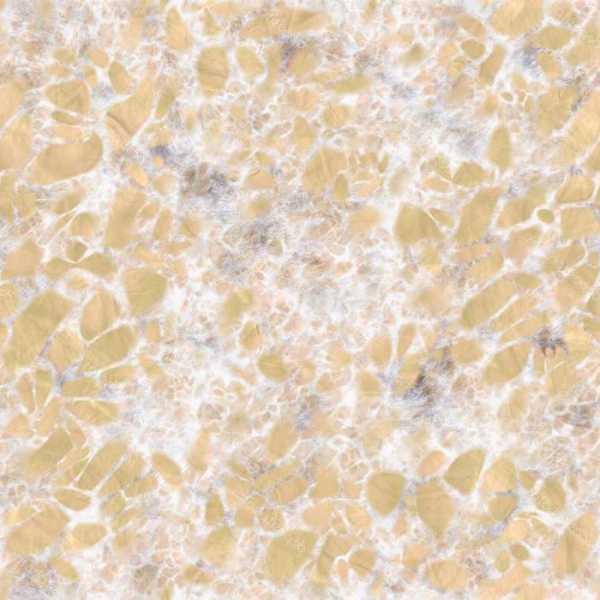
Материал имеет идеально ровную бесшовную поверхность, поэтому его можно использовать для облицовки сооружений неправильной формы, а именно:
- сферических предметов;
- колонн;
- арок.
Перед тем как сделать жидкий камень, необходимо подготовить соответствующее оборудование:
- заливочные формы;
- миксер;
- распылитель;
- кисти.
Информация о формах
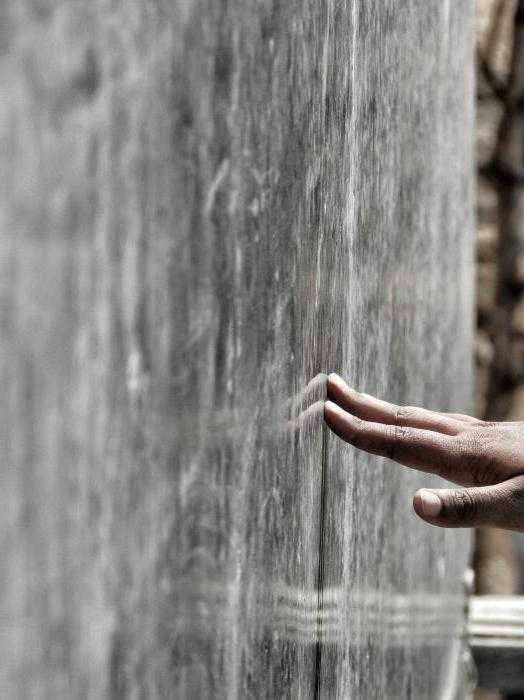
Заливочные формы еще называются матрицами, а вот распылитель понадобится для гелькоута. Для размешивания состава необходимо запастись миксером, тогда как смазывать формы предстоит кистями. Формы для мрамора выполняются на основе полиуретановой резины. Матрица отличается прочностью и отсутствием склонности к деформациям, поэтому стоит дорого, однако ее цена окупается, ведь производство обладает высокой рентабельностью.
Состав материала
Если вы затеяли изготовление жидкого камня, то необходимо придерживаться пропорций. Для этого смешивают полиэфирную или акриловую смолу с мраморной крошкой, используя для этого соотношение 4 к 1. В качестве связующего ингредиента можно использовать цементный либо известковый раствор или строительный гипс. Однако наиболее часто применяются смолы, так как они обеспечивают высокую прочность.
Заключение
Изделия из жидкого камня сегодня используются повсеместно. Это могут быть элементы декора или части предметов мебели, а также облицовочные материалы. Примечательно, что их вы можете выполнить самостоятельно, что позволит значительно сэкономить. Кроме того, разновидностей такого камня сегодня очень много, а все ингредиенты можно отыскать в магазине строительных материалов. А вот производством можно заняться на основе технологии, которая нравится вам больше прочих.
fb.ru
изготовление строительного блока, расчёт пропорции в домашних условиях
Многочисленные исследования специалистов, которые работают в сфере строительства, доказали, что опилкобетон является отличным материалом для возведения прочных и тёплых стен. Помимо этого, он отличается высокими теплоизоляционными свойствами, хорошими санитарно-гигиеническими показателями и огнестойкостью. Изготовить качественный опилкобетон своими руками не так уж и сложно, главное, придерживаться правильной пропорции и технологии производства.
Краткое описание материала
Опилкобетон относится к категории лёгких материалов. Это связано с тем, что для его изготовления используются обычные древесные опилки, песок и цемент. Впервые этот материал был разработан ещё в 1960 году, но своё применение получил только вначале 90-х. Засчет того, что опилкобетон обладает высокими санитарно-гигиеническими показателями, он широко используется для возведения различных зданий и учреждений. Блоки получаются очень крепкими, благодаря чему их можно смело подвергать любым механическим обработкам. Можно не бояться, что на опилкобетоне образуются трещины или сколы.
Многие потребители часто путают этот материал со специфическими арболитовыми блоками. Но между ними есть главное отличие — в них используются совершенно разные заполнители. Стоит отметить, что для арболита применяется специальная дроблёная щепка, которую получают в результате тщательного измельчения древесины. В состав также входят дроблёные стебли хлопчатника и камыша. А вот что касается опилкобетона, то для его изготовления нужен только опилковый заполнитель.
Особенности изготовления
Специалисты всегда акцентируют внимание на том, что для производства опилкобетона необходимо использовать только качественные опилки тех пород дерева, которые отличаются минимальным содержанием сахаров. Оптимальными в этом случае считаются:
- Сосна.
- Ель.
- Тополь.
- Берёза.
Несмотря на то что лиственница отличается высокими прочностными характеристиками, она находится на самом последнем месте по популярности, так как в ней содержится высокий процент сахаров. К примеру, у ели начало набора прочности начинается через 14 дней после полного высыхания, а вот окончание этой процедуры происходит на сороковой день после изготовления. Что же касается лиственницы, то этот период длится гораздо дольше — более 30 дней для набора прочности и 140 дней для его окончания.
Чтобы добиться желаемого результата, все работы по опилкобетону нужно проводить в середине весны, чтобы к приходу осени все было готово. Из-за того, что из опилок выделяется специфический сахар, работать с ними нужно исключительно на свежем воздухе. Не стоит забывать о том, что опилки обязательно нужно полить чистой водой, чтобы смыть все имеющиеся остатки распада сахара.
Состав смеси
Именно от того, насколько правильно подобран каждый компонент, зависит качество будущего материала. Используемые блоки должны быть прочными и долговечными. Вне зависимости от марки опилкобетона, в его состав должны входить следующие компоненты:
- Песок.
- Цемент.
- Опилки.
- Гашёная известь.
Разница в пропорции зависит только от соотношения компонентов смеси. Строители отмечают, что блоки с большим содержанием цемента больше всего подходят для возведения многоуровневых нежилых зданий. Такая тенденция объясняется тем, что меняется коэффициент теплопроводности материала, а это чревато большими расходами на отопление. Если мастер решит использовать цемент М10, то коэффициент будет равен 0.21, что очень хорошо при любых условиях.
Для марки цемента М15 этот показатель составляет 0.24, что обусловлено незначительными изменениями в требованиях к прочности. Именно поэтому мастеру потребуется гораздо больше цемента, чтобы построить качественный двухэтажный дом. Что касается марки цемента М25, то его коэффициент увеличивается до 0.39, а это уже в два раза больше, нежели у блока М10. Конечно, такой опилкобетон получается более холодным, но он отлично подходит для возведения больших зданий.
Преимущества и недостатки
Каждый специалист знает, что перед тем использованием любого материала необходимо ознакомиться со всеми его плюсами и минусами. Помимо этого, чтобы изготовить строительные блоки из опилок своими руками, нужно учесть каждый нюанс. Начинать знакомство с опилкобетоном лучше всего с его сильных сторон.
Преимущества:
К положительным характеристикам можно отнести хорошую устойчивость к низким температурам. Опилкоблок может выдержать до 50 циклов сильной заморозки.
- Невысокая стоимость расходных материалов.
- Высокий процент теплоэффективности. Качественный блок из опилок считается лидером на современном строительном рынке. Если сравнивать этот материал с представителями лёгких бетонов, то превзойти опилкобетон может только полистиролбетон. Стоит отметить, что коэффициент блока из опилок варьируется от 0.07 до 0.20.
- Материал легко поддаётся обработке, а его габариты сравнительно велики. Именно эти факты указывают на то, что с помощью этих блоков можно возвести необходимые здания за короткий срок.
- В состав опилкоблоков входят только экологические материалы, которые полностью безопасны как для людей, так и для окружающей среды.
- Хорошая защита от посторонних звуков.
- Засчёт того, что в блоке содержится цемент, он не подвержен внезапному возгоранию.
- Многие специалисты утверждают, что изготовление опилкобетонных блоков в домашних условиях не имеет каких-либо сложностей, и с задачей справится даже новичок.
Среди недостатков можно выделить:
Блоки подвержены усадке.
- Очень часто геометрия материала оставляет желать лучшего.
- Достаточная гигроскопичность. Опилки хорошо впитывают влагу. Но важно отметить, что этот показатель не считается высоким среди стеновых зданий.
- Нужно много времени, чтобы опилкобетон достиг необходимой марочной прочности. В некоторых случаях это может занять несколько месяцев.
- В связи с тем, что технология изготовления блоков не является сложной, их часто изготавливают в кустарных условиях. Конечно, качество таких изделий не контролируется и не тестируется, что повышает риски покупки материала сомнительного качества.
Этапы самостоятельного производства
Чтобы изготовить качественные опилкоблоки своими руками, нужно придерживаться нескольких рекомендаций, которые были разработаны опытными специалистами. Это связано с тем, что только точное выполнение всех норм позволит получить качественное изделие, которое будет обладать необходимыми прочностными и эксплуатационными характеристиками. Основной алгоритм производства выглядит следующим образом:
- На первом этапе осуществляется подготовка всех необходимых материалов. Стоит отметить, что нет необходимости приобретать основные составляющие компоненты заранее. Все это можно сделать непосредственно перед изготовлением блоков. В этом случае отлично подойдёт не только специализированный строительный магазин или склад, можно воспользоваться производственными отходами деревообрабатывающих предприятий.
- Все компоненты должны быть смешаны в одной ёмкости в соответствии с пропорцией. Для перемешивания может быть задействован механический способ с применением мощного бетоносмесителя либо ручным путём при помощи обычных лопат. Как показывает практика, автоматизация технологического процесса с помощью строительной бетономешалки позволяет существенно повысить итоговую производительность, а также улучшить качество продукции. В этом случае обеспечивается тщательно смешивание всех ингредиентов, которое помогает избежать последующего брака.
- На следующем этапе осуществляется формировка блоков. Огромным преимуществом обладает групповой процесс формировки. Эта технология подразумевает то, что тщательно перемешанный состав заливается сразу в несколько форм. В зависимости от масштабов стройки, специалисты могут использовать как единичные, так и групповые формы разборной конструкции. Они могут быть изготовлены из качественной древесины толщиной 2 см и обиты пластиком или же металлом. Использование обычной полиэтиленовой плёнки упрощает извлечение готовых блоков.
- На финальном этапе проводится сушка готового материала под открытым небом. Через 5 суток после заливки осуществляется снятие форм. В этом случае мастер должен ослабить затяжки барашковых гаек, извлечь резьбовые шпильки и поэтапно разобрать формировочный ящик. Длительность естественной сушки зависит исключительно от породы древесины (не более трёх месяцев). В течение этого промежутка времени существенно снижается количество влаги, и блоки приобретают необходимую эксплуатационную прочность.
Необходимые инструменты и формы
Не только опытные строители, но и начинающие мастера все чаще решают сделать опилкобетон своими руками. Технология изготовления подразумевает наличие щитков для опалубки. Они должны быть правильно вымерены, чтобы блоки получились максимально ровными. Желательно, чтобы доски для щитка имели толщину 38 мм. Опилки обязательно просеивают от накопившегося мусора и камней. Когда щепа и кора отсортированы, нужно добавить к ним подготовленную древесную стружку. Так можно увеличить итоговую прочность материала в несколько раз.
Укладка раствора может осуществляться в два типа форм:
Небольшие блоки. Такие формы имеют компактные размеры, и за один раз можно изготовить до 9 опилкоблоков.
- Габаритные блоки. Для такого материала необходимо подготовить вместительные ящики из досок. Стоит отметить, что чаще всего они разборные, так как это ускоряет процесс изъятия готового материала.
Специалисты утверждают, что к укладке приготовленного раствора необходимо приступать сразу, так как уже через несколько часов он начнёт застывать. Нужно помнить, что перед использованием внутренние части опалубки обязательно увлажняются обычной водой.
Укладывать раствор необходимо аккуратными слоями по 150 мм. При этом каждая часть должна быть тщательно утрамбована, так как это предотвращает образование пустот.
Через четыре дня опалубку необходимо аккуратно снять (но только в том случае, если раствор полностью застыл). А вот опилкоблоки желательно оставить досыхать ещё на четыре дня. Это делается для того, чтобы повысить итоговую прочность материала. Отдельно стоит учесть, что для сушки изготавливаемых блоков лучше всего использовать тот участок, где есть сквозняки, чтобы раствор застывал равномерно. Между каждым опилкоблоком должен присутствовать зазор. Если собирается дождь, тогда материал нужно укрыть плёнкой, чтобы предотвратить намокание.
Для гарантированной сушки должны быть задействованы столбы. Блоки можно уложить на кирпичи. Благодаря таким манипуляциям, можно добиться 90% прочности уже после месяца такой сушки.
Оптимальные пропорции
Как показывает практика, несоблюдение минимальных требований чревато негативными последствиями, которые могут существенно снизить качество возведённого здания. Пропорции зависят от того, какую марку цемента будет использовать мастер. Оптимальное соотношение компонентов выглядит следующим образом:
Для цемента марки М10 нужно: полное ведро чистого песка, 5 кг цемента и три полных ведра опилок.
- Опилкобетон на основе цемента М15: 1.5 ведра песка, полведра цемента и 4 ведра древесных опилок.
- Цемент М25: 1.5 ведра песка, 0.5 ведра цемента и три ведёрка опилок.
Стоит отметить, что каждый мастер должен придерживаться именно этой рецептуры, так как это было проверено в течение нескольких десятилетий. Строителей не должно смущать отсутствие прогрессии в пропорциях и количестве. Такая тенденция связана с тем, что в каждом случае компоненты работают совершенно по-разному. Что касается гашёной извести, то она нужна для надёжного обессахаривания опилок.
tvoidvor.com
разновидности и технологии изготовления своими руками
Здравствуйте, мои дорогие читатели! Совсем недавно, возле ближайшего к нашему дому магазина поставили тандыр. Теперь я не могу спокойно пройти мимо, потому что оттуда постоянно доносится обалденный запах свежего хлеба. Хотя я стараюсь меньше употреблять белую муку, но по утрам иногда позволяю себе небольшой кусочек еще теплой лепешки со сливочным масло. Ммм… Какое это объедение! И сегодня мне захотелось рассказать вам немного об этой печи и, конечно же, поделиться секретами ее изготовления своими руками.Тандыр – это очень интересная конструкция для готовки необычных, вкусных блюд, преимущественно восточной кухни. По своей сути тандыр является одновременно печью, жаровней и мангалом. В нём за счёт прямого (от тлеющих углей) и контактного тепла от разогретых стенок происходит тепловая обработка различных продуктов, в результате чего они доводятся до приготовленного состояния, приобретают великолепные органолептические качества.
Придумали тандыр люди из Центральной и Средней Азии, а упоминания об этих необычных печах начали встречаться в рукописях Х века н. э. Такая географическая локализация их появления совсем неслучайна – на пустынных территориях того региона был постоянный дефицит хорошего топлива из-за отсутствия деревьев. Это обстоятельство заставило найти эффективное решение, позволяющее готовить еду при минимальных затратах дров.
Немного об истории появления тандыров
Придумать способ готовки нормальной еды в пустынных условиях Азии “подсказала” сама природа. Её особенности и строительные материалы оптимально подходили для постройки печей-жаровен. Во-первых, невероятно сухой, жаркий климат, а во-вторых – изобилие лёсса – природного строительного материала, обладающего некоторыми уникальными чертами. К ним относятся:
- высокая теплоотдача и отличная теплоёмкость – это обуславливает быстрое нагревание и продолжительное время освобождения (испускание) тепловой энергии
- лёсс характеризуется достаточной прочностью, воздухопроницаемостью и жаростойкостью
- материал в сухом состоянии довольно легко обрабатывается, а при смачивании водой приобретает мягкость и податливость, как детский пластилин
Справка! Лёсс – осадочная, неслоистая, однородная горная порода палевого или светло-жёлтого цвета. В пустынных местах встречается в измельчённом виде. Он состоит из порошкообразных частиц полевого шпата, кварца, вулканического пепла, слюды, каолинита и мн. др.!
Используя этот замечательный материал, кочевники и пастухи создавали первые прототипы тандыров. Окружающий климат благоприятствовал упрощению методики изготовления этих полезных сооружений. Самые простые первые тандыры представляли собой земляные сооружения. Их делали в массе лёссового грунта. Выкапывали яму небольших размеров (приблизительно, глубина 34,5 см, диаметр 0,45 м) в которой сбоку обустраивали воздуховод.
Дальнейшее развитие технологии способствовало прогрессированию конструкции тандыра. Люди стали выкапывать более глубокие, узкие сверху ямы, напоминающие свой формой кувшин. Такая конфигурация позволяет более эффективно концентрировать тепло в центральной части печной камеры.
Немного позже получили распространение печи-жаровни из каолиновой или шамотной глины, которая очень близка по характеристикам к лёссовому материалу. Начали добавлять в глину рубленую шерсть и песок для придания большей густоты раствору. Из него мастера формировали заготовку, которую выставляли на двухнедельную просушку под палящее солнце. Сухой, горячий воздух и томительный зной создавали практически идеальные условия низкотемпературного обжигания глиняных сооружений. Таким способом строили легендарные узбекские печи-тандыры.
Особенности функционирования тандыра
Организован принцип работы таких печей на удачной комбинации уникальных качеств материала и своеобразности конструкции.
Построенная из лёсса, шамотной глины или иного аналогичного материала печь, после хорошего разогревания изнутри, равномерно и постепенно отдаёт тепло во внутреннюю камеру, где размещается приготавливаемая пища. В результате продукты нагреваются и доводятся до съедобного состояния.
Еда внутри тандыра не жарится непосредственно над тлеющими углями, как на классическом мангале, а всесторонне запекается. Кстати, подобный принцип теплового томления характерен для русской печи.
В тандыре тепловая энергия поступает в ограниченный (закрытый) объём от сильно нагретых теплоёмких стенок, абсолютно равномерно нагревая пищевые продукты или разогреваемую еду. Именно эта особенность существенно отличает тандыр от широко известного мангала, на котором яство запекается неравномерно, только с одной стороны.
Разновидности тандыров
Существует три вида печей-жаровен:
Стационарные наземные – это конструкция, напоминающая по форме продольную или поперечную половину кувшина, установленную на фундаментное основание.
Земляные (ямные) – сооружения такого типа бывают двух модификаций. Первая – в виде неглубокой ямы с ровными глиняными стенками, а вторая – сформированная основа яйцеобразной формы с горловинным отверстием сверху и воздуховодным снизу. Последний вариант подразумевает размещение и закапывание готовой печи в яме. При этом потребуется приладить к нижнему отверстию трубу, выходящую вторым концом рядом над землёй.
Современные переносные – последняя историческая версия тандыров. Конструкция здесь представлена большим глиняным или шамотным кувшином с крышкой и вспомогательными металлическими частями (обрамление, ручки, внутренние скобы или крючки для подвешивания продуктов, ножки и т. п.).
Важно! Все виды тандыров обязательно обустраиваются каналом-трубой в донной части для поступления воздуха к дровам, брикетам или углям на стадии розжига и разогревания стенок!
Принципы использования тандыра
Чтобы приготовить в печи-жаровне вкусную, пропечённую еду, необходимо выполнить такую последовательность действий:
- подготовить тандыр – очистить от старых углей, пепла и нагара на стенках
- открыть наземный конец воздуховодного канала
- поместить уголь или дрова внутрь печного корпуса максимум на 2/3 объёма
- аккуратно разжечь топливо (дрова, брикеты, уголь)
- после прогорания загруженного материала образуется слой тлеющих углей, здесь можно подкорректировать равномерность их расположения
- поместить заготовленные продукты в печную камеру
- закрыть крышками горловину тандыра и внешнее отверстие воздуховодного канала
Принять в расчёт! О новом нагаре и пепле не стоит беспокоиться, поскольку основная масса копоти самостоятельно опадёт со стенок ещё до размещения продуктовых полуфабрикатов!
Спустя некоторое время пища будет приготовлена и её можно вынимать из печи. По завершении процесса готовки, тандыр должен пассивно остывать естественным образом.
Тандыр своими руками: технология создания наземной и ямной печи
Построить на участке или в собственном дворе типично-азиатскую печь – задача не совсем простая. Только в случае выполнения пошаговой инструкции можно соорудить долговечный, надёжный агрегат.
Материалы и инструменты, необходимые для строительства
Чтобы создать любую разновидность стационарного тандыра (ямный или наземный) потребуется основной набор следующих материалов и инструментов:
- цемент, очищенная глина, мелкий песок
- огнеупорный кирпич и облицовочный материал (плитка, натуральный камень и т. п.)
- металлическая колосниковая (щелевая) решётка и кладочная сетка
- ёмкости для замешивания глиняной массы и цементно-песчаного раствора
- мастерок, лопата, строительный уровень, болгарка, вёдра
В зависимости от выбранного варианта тандыра, может понадобиться и другой инструментарий.
Пояснение! Настоящий, классический тандыр возводится из несколько других материалов (лёсс, шерсть животных и т. п.), хотя современные условия позволяют применять не менее качественные составляющие!
Методики создания тандыров
Заблаговременно необходимо определиться с типом желаемого тандыра. Наиболее распространённой считается вертикальная наземная разновидность. Рассмотрим подробнее технологию возведения вертикального тандыра и земляной печи-жаровни. Методики имеют принципиальные различия, поэтому описаны они будут по отдельности.
Постройка наземного тандыра своими руками
Строительство вертикальной конструкции (высота 1,27–1,35 м) состоит из следующей последовательности этапов:
Выбор и подготовка места для строительства тандыра – площадка должна быть ровной, твёрдой и желательно с навесом.
Обустройство качественного фундамента, способного выдерживать массу печи. Необходимо выкопать в земле яму достаточного размера и глубины. Поместить на дно углубления «подушку» из песка и среднефракционного щебня, а затем залить раствор бетона. Как правило, бетонное основание делают толщиной в 15,5-20,0 см. Если изготавливается фундамент превышающий уровень земли, то нужно построить соответствующую опалубку из фанерных полос или досок.
Дождаться схватывания бетонной заливки. Пятнадцатисантиметровый фундамент при сухой погоде застывает через пару-тройку суток.
На фундаментной площадке намечается правильную окружность диаметром в 1,0 метр. Из огнеупорных кирпичей выкладывается идеально ровный первый ряд, в котором должно располагаться «окошко» для поступления воздуха, необходимого горящему топливу. Следующий кирпичный ряд кладётся с половинным сдвигом (для большей прочности и устойчивости), по всей окружности целиком, без каких-либо промежутков.
На созданном втором кирпичном ряду размещается колосниковая решётка и кладка продолжается. Приблизительно до восьмого ряда возведение строения выполняется строго вертикально. Последующие ряды аккуратно укладываются с 0,5-сантиметровым сдвигом вовнутрь, поскольку необходимо формировать куполообразное сужение.
Завершается кирпичная кладка на высоте, где верхнее отверстие сузится до 50,0-сантиметрового диаметра (для 1,0-метрового основания).
После укладки кирпича (можно сразу же) осуществляется обмазка корпуса изнутри глиняной массой, которая готовится непосредственно перед нанесением. По консистенции глиняный состав должен быть схожим с густой сметаной. Окончив равномерное обмазывание, необходимо печь оставить на пассивную просушку.
По завершении полного высыхания следует наполнить тандыр хорошо горящей смесью (хворост, сухая солома и древесная стружка) и поджечь её. Эта процедура закалит глиняную обмазку и сделает печь-жаровню полностью готовой к дальнейшему использованию.
Дождавшись остывания, нужно обложить конструкцию вторым (внешним) слоем кирпича, соблюдая точную вертикальность.
Нюанс! При создании внешней кладки необходимо с особой тщательностью проводить заполнение всех щелевых пустотных пространств между положенными кирпичами!
Когда нанесённый цементно-песчаный раствор надёжно схватится, зазор между печью и наружной кладкой заполняется густой смесью глины, песка, керамзита и воды. Здесь вместо глины можно использовать цемент.
Создание земляного тандыра своими руками
Ямная узбекская печь собирается по такому принципу:
- выбор подходящего места
- подготовка котлована для тандыра – глубина рассчитывается исходя из высоты самой печи (обычно 1,25 м) плюс толщина фундаментной основы (в среднем 17,0 см). Фундамент (дно) выкладывается из одного слоя шамотного кирпича
- укладывание первого ряда тугоплавких кирпичей с обязательным формированием промежутка для подсоединения пути, подводящего воздух
- устройство воздуховодной трубы – к подготовленному фундаменту, в оставленный промежуток первого ряда кирпичей помещается конец асбестоцементной трубы. Все щели между кирпичами и трубой тщательно замазываются цементно-песчаной смесью. Разумеется, труба должна располагаться под наклоном (угол 45 град), чтобы второй её конец возвышался над поверхностью земли
- далее выполняется строительство печи по аналогии с надземным тандыром, технология создания которого описана ранее
- изнутри кладка покрывается густой, пластичной глиняной массой
- снаружи кирпичи нужно обмазать цементно-песчаной смесью и конструкция оставляется на просушку
- финишным этапом будет засыпание свободного пространства по бокам печи, очищенным от камней, грунтом. Почву следует плотно утрамбовать, а сверху, площадку вокруг горловины, залить бетоном или сделать кладку из тротуарной плитки
Как только все фиксирующие и изоляционные составы высохнут, можно приниматься за процесс обжига тандыра. Закалка выполняется по технологии, описанной в предыдущем разделе статьи.
Заключение
Помимо описанных моделей тандыров, существуют более замысловатые варианты, которые не так доступны и менее популярны. Простую, но весьма качественную восточную печь-жаровню может соорудить даже малоопытный строитель. Главное – это правильный выбор места для печи, грамотная постройка фундамента с предварительным расчётом нагрузки и точное следование инструкциям на последующих этапах возведения.
Надеюсь, статья стала для вас полезной и интересной! Делитесь ею с друзьями, оставляйте комментарии! До новых встреч! Пока!
homeblogkate.ru
Изготовление арболита своими руками: технология производства и самостоятельные работы
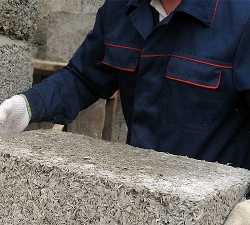
Поэтапная технология изготовления арболита предвидит подготовку основания, определения компонентов и состава блочного материала. В данной статье рассмотрим особенности производства своими руками с применением необходимого оборудования, расчета массы и заливки.
Оглавление:
- Преимущества и недостатки арболита
- Технология производства арболита
- Подготовка основания для работы
- Компоненты и состав арболита
- Процесс и принципы изготовления
- Оборудование: применение на практике
- Блочные формы для арболита
- Процесс производства своими руками
- Советы экспертов при изготовлении блоков своими руками
Преимущества и недостатки арболита
Для многих строителей арболитные блоки являются ценным и качественным материалом для возведения домов. Главная особенность теплоизоляционных свойств позволяет из раствора производить напольные листы. Технология изготовления и принципы выдержки и сушки блоков предоставляют арболиту некоторые преимущества:
1. Прочность материала составляет 600-650 кг/м3, что по компонентной структуре не уступает иному строительному материалу. Главной особенностью является пластичность, что формируется в результате использования древесины, которая качественно армирует блоки. Таким образом, арболит не трескается под тяжестью иных материалов, а может только слегка деформироваться сохраняя общую систему конструкции.
2. Стойкость к низким температурам, что очень важно в процессе возведения дома и его эксплуатации. Дело в том, что если здание нагреется и замерзнет несколько раз, то это не повлияет на качество материала. Фактически дом из арболита может простоять минимум 50 лет в любые погодные условия. Конструкции из пеноблоков не имеют подобных свойств, ведь при постоянном замораживании они быстро потеряют свою функциональность.
3. Арболит не поддается воздействию углекислого газа, так что не стоит беспокоиться о карбонизации блоков, ведь их структура не позволит превратиться материалу в мел.
4. Теплопроводность блоков свидетельствует о популярности материала. Сравнивая показатели, стоит отметить, что стена из арболита в 30 см равняется 1 метру толщины кирпичной кладке. Структура материала позволяет сохранять тепло внутри помещения даже в самые холодные зимы, что весьма экономично при строительстве.
5. Звукоизоляционные свойства свидетельствуют о высоком коэффициенте поглощения арболита, который составляет от 0,7 до 0,6. Для сравнения древесина имеет показатели 0,06 -0,1, а кирпич немного больше около 0,04-0,06.
6. Легкость материала, что позволяет сэкономить средства на заливку фундамента.
7. Арболит является экологически чистым и долговечным строительным материалом, что определяет компонентный состав блоков. После возведения дома он не образует плесень и грибок на стенах.
8. Материал является безопасным, так он не воспламенятся.
9. Арболитные блоки легко применять в строительных работах, поскольку без труда в них можно забить гвозди, просверлить отверстие, использовать шурупы и так далее. Внешняя структура материала позволяет покрывать его штукатуркой без использования специальных сеток и дополнительных утеплителей.
Мы рассмотрели преимущества арболитных блоков, но для полного воссоздания картины о данном строительном материале приведем некоторые недостатки:
1. Стеновая панель может не выделяться точными геометрическими параметрами, от чего для восстановления ровности стены используют вагонку, сайдинг или гипсокартон, а сверху все отделяют штукатуркой.
2. Блоки не являются дешевым строительным материалом, ведь изготовление щепы для арболита требует некоторых затрат. Делая расчеты по сравнению из газобетоном, данный строительный материал обойдется только на 10-15 процентов дороже, что не формирует полное преимущество.
Технология производства арболита
Изготовление арболита требует следованию технологиям производства с расчетом состава и объема для одного блока. Арболитные блоки представляют собой строительный материал простой по компонентному составу, в который входят древесина, вода, опилки, цемент и другие предметы.
Главной основой для производства считается древесная щепа. Составная часть арболитового блока определяет его прочность и устойчивость к повреждениям, что высчитывается высшим уровнем, чем у пено- или газоблоков. Производство в домашних условиях осуществить не сложно, однако необходимо придерживаться распределения массы предмета и следовать инструкции.
Подготовка основания для работы
Основной составляющей для изготовления щепы для арболита является соотношение пропорций стружки и опилок – 1:2 или 1:1. Все предметы хорошо высушивают, для чего их помещают на 3 – 4 месяца на свежий воздух, время от времени обрабатывая известью и переворачивая.
Примерно на 1 кубический метр средства потребуется около 200 литров извести 15-ти процентной. В них помещают все щепы на четыре дня и перемешивают их от 2 до 4 раз на день. Все работы проводятся с целью убрать сахар с древесины, который может спровоцировать гниение блоков. Щепу приобретают в готовом виде, однако, с помощью щепорезов можно сделать самостоятельно.
Компоненты и состав арболита
Компонентный состав арболита является самым важным этапом технологии производства и требует внимательного соотношения всех материалов. При изготовлении блоков важно следить за качеством и разновидностью приобретаемых материалов, которые определяют готовый строительный материал. После процесса изготовления в щепу добавляют следующие материалы, такие как:
- известь гашеную;
- жидкое стекло растворимое;
- портландцемент;
- хлористый калий;
- алюминий и сернокислый кальций.
Производство арболита в пропорциях представлено в таблице 1. Стоит учесть, что для всех компонентов масса рассчитана на четыре процента доли цемента. Данная компоновка помогает сохранить огнеупорность предмета и придает пластичности.
Таблица 1. Состав арболита по объему
Марка арболита | Цемент (М400) | Кол-во извести | Кол-во песка | Кол-во опилок | Получаемая плотность (кг/м3) |
5 | 1 | 1,5 | — | 15 | 300-400 |
10 | 1 | 1 | 1,5 | 12 | 600-700 |
15 | 1 | 0,5 | 2,5 | 9 | 900-1000 |
25 | 1 | — | 3 | 6 | 1200-1300 |
Процесс и принципы изготовления
Оптимальные параметры блоков для технологии производства арболита составляют 25х25х50 сантиметров. Установленные размеры удобны при кладке стен домов, а также в процессе промышленности. Заливка блока состоит из трех рядов смеси и арболита, после каждого этапа необходимо уплотнять раствор молотком, отделанным жестью.
Излишняя масса свертывается при содействии шпателя. Выдерживается блок при температуре 18 градусов тепла на раскрытом воздухе. По истечении суток арболит выстукивается из формы на ровную поверхность, где он скрепляется на протяжении 10 дней.
Оборудование: применение на практике
Для производства необходимо разное снабжение, например, станки для изготовления арболита, которые выбираются в соответствии с объемом продукции и количества сырья. Технология промышленного процесса должна отвечать требованиям и критериям СН 549-82 и ГОСТу 19222-84. В качестве основного материала для выработки выступают хвойные деревья. Раздробление древесины происходит с помощью рубильных машин, таких как РРМ-5, ДУ-2, а более скрупулезное дробление осуществляется на оборудовании ДМ-1.
Арболитовую смесь подготавливают со смесителями и растворителями различного цикличного воздействия на материал. Подвозят большие объемы обработанной смеси к формам с помощью приспособления в качестве бетонораздатчиков или кюбелей. Подъем или опускание машины должно осуществляться при параметрах 15о по верхнему подъему и 10о по нижнему, а скорость оборудования рассчитывается в 1 м/с. Разлив арболитовой смеси по формам делают на высоте до 1 метра.
Уплотнения раствора производят с содействием вибропреса или ручной трамбовки. Для производства небольшого количества блоков нужно применить мини-станок. Изготовление своими руками арболита не представляет особых трудностей, однако на промышленных объектах применяется специальное оборудование по смешиванию, изготовления блоков. На некоторых заводах присутствуют тепловые камеры с ИК-излучением или ТЭНом, что позволяет определить нужную температуру для высыхания блоков.
Блочные формы для арболита
Существуют разные блочные формы для обработки арболита, а примерные величины могут составлять: 20х20х50 см или 30х20х50 см. Выпускаются предметы и прочих размеров, особенно для постройки вентиляционных систем, покрытий и так далее. Формы можно приобрести в строительных магазинах или же подготовить все своими руками. Для этого, используют доски толщиной в 2 сантиметра, которые скрепляют до образования определенной конструкции. Внешне форма отделывается фанерой, или пленкой.
В зависимости от класса арболитовые блоки применяют в малоэтажном строительстве для возведения несущих стен, перегородок, а также для теплоизоляциии и звукоизоляции конструктивных элементов здания.
Процесс производства своими руками
Рассмотрев технологию изготовления состава арболита, можно приступать к выполнению работы самостоятельно. Для начала потребуются некоторые материалы и оборудование:
- специальный лоток для смеси;
- падающий и вибрирующий стол;
- стол с ударно-встряхивающим эффектом;
- разъемные формы и подставки;
- поддон из металла для форм.
Производить арболит своими руками очень сложно без использования необходимых инструментов, станков и оборудования. Как правило, на производстве потребуются некоторые приспособления:
1. Для получения качественного раствора необходимо применить бетономешалку. Разумеется, в процессе можно все сделать своими руками, однако придется, много времени потратить на получение раствора необходимой консистенции.
2. Для формирования структуры блоков важно приобрести формы соответствующих размеров. Как правило, арболит имеет прямоугольную форму, а в производстве используются пластиковые формы.
3. При помощи станка вы профессионально измельчите щепу.
4. Используя пресс можно получить хорошую плотность материала при трамбовке, при этом важно убрать воздух из консистенции. В качестве приспособлений применяется вибростол.
5. Обязательное наличие камеры для сушки арболита, что позволит его превратить в твердую однокомпонентную структуру.
6. В домашних условиях понадобится лопата для загрузки смеси в формы, а для скрепления блоков используют армирующую сетку.
При наличии выше перечисленных приспособлений можно производить в день около 350 – 450 м3 строительного раствора в месяц. Места для монтажа потребуется около 500 квадратных метров, а затрат на электроэнергию пойдет 15-45 кВт/ч. Для самостоятельного процесса органические средства заливаются водой, а также цементом до образования однородной смеси. Все пропорции и расчеты отображены в таблице 1, главное чтобы вышедшая смесь была сыпучей.
Перед заливкой раствора в формы, их обмазывают с внутренней стороны молочком известковым. После этого, средство скрупулезно и аккуратно укладывают и утрамбовывают специальными приспособлениями. Верхняя часть блока выравнивается с помощью шпателя или линейки и заливается раствором штукатурки на слой в 2 сантиметра.
После образованной формы арболита его потребуется тщательно уплотнить с помощью деревянной конструкции, оббитой железом. Прочными и надежными считаются блоки, которые выстоялись и схватились на протяжении десяти дней при температуре 15о. Чтобы арболит не пересох, рекомендуется периодически поливать его водой.
Технология изготовления арболита своими руками не представляет определенной сложности, а поэтому все работы провести легко при наличии необходимых инструментов и приспособлений. При соблюдении правил и критериев производства, правильного расчета компонентов строительный материал получится качественным и прочным для применения.
Советы экспертов при изготовлении блоков своими руками
Рекомендации специалистов по производству арболитных блоков основаны на практике их использования и применения. Чтобы достичь высокого качества продукции необходимо следовать некоторым факторам. В производстве рекомендуется применять не только большую щепу, но и использовать опилки, стружку из дерева. Обработка консистенции и выдавливание из него сахара позволяет избежать дальнейшего вспучивания строительного материала, что не приспускается при сооружении дома.
В процессе изготовления раствор следует тщательно перемешивать, чтобы все части оказались в цементе. Это важно для качественного и прочного скрепления древесины и иных материалов в блоке. В производстве не менее важным остается добавление следующих компонентов, таких как алюминий, гашеная известь и так далее. Весь состав образует дополнительные свойства арболита, например жидкое стекло не позволяет впитывать влагу блокам, а известь служит в качестве антисептика.
Хлористый калий способствует уничтожению микроорганизмов и других веществ, что не благотворно влияют на структуру. При добавлении всех компонентов стоит следить за таблицей пропорциональности, чтобы готовый раствор соответствовал требованиям производства арболитных блоков.
strport.ru
Декоративный бетон своими руками: состав и технология изготовления
Если взглянуть на красивые покрытия дорожек, стен и заборов, довольно сложно представить себе, что все они изготовлены из обычного бетона. Современные покрытия отличаются от своего предка, который известен унылым малопривлекательным серым видом. В данном случае речь идет о декоративном бетоне, который нашел свое широкое распространение в ландшафтном дизайне и современном строительстве.
Основные компоненты
Впервые его применили в 60-х гг. прошлого века при строительстве взлетно-посадочных полос. Перед мастерами стояла задача создать материал, который сочетал бы в себе и хорошие эксплуатационные характеристики, и отличные декоративные качества. В основе структуры лежат:
- заполнитель;
- вода;
- цемент;
- присадки;
- краски.
Главные преимущества
Покрытие соответствует всем необходимым требованиям, поэтому и получило распространение в ряде отраслей. Декоративный бетон, благодаря усилиям разработчиков, обрел ряд неоспоримых преимуществ, среди которых следует выделить:
- устойчивость к воздействию химических веществ, нефтепродуктов и агрессивных соединений;
- устойчивость к ультрафиолетовому излучению;
- способность претерпевать высокую нагрузку;
- устойчивость к истиранию и механическим воздействиям.
Что касается способности выдерживать нагрузку, то она почти в три раза больше, чем у прессованной тротуарной плитки. Если использовать прессованный бетон, то можно создать красивые и долговечные покрытия. В массу добавляются специальные вещества, которые исключают расслаивание и растрескивание.
Способы формирования интересных фактур
Если проводить сравнение декоративного бетона с обычным, то можно выделить исключительно эстетичность и долговечность. Технология сводится к заливке и нанесению на верхний слой определенного рисунка. Для оформления поверхности можно использовать штампы и другие инструменты. Это могут быть прессформы, трафареты и химические составы для протравливания, с помощью которых можно создавать сложные орнаменты. Применив пилы с алмазными полотнами, вы сможете сформировать тонкие линии, которые придадут бетону четкость и выразительности рисунка.
Технология изготовления
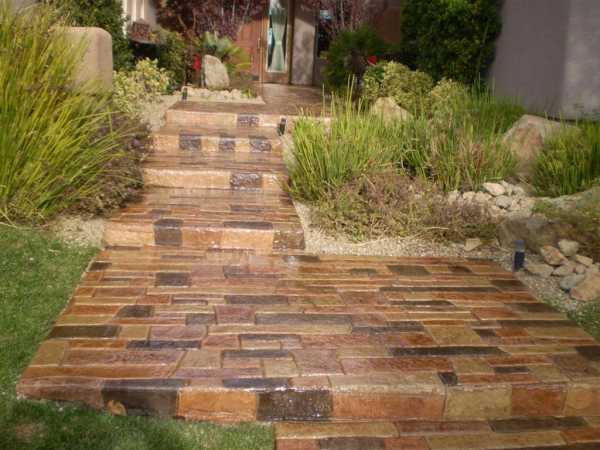
Декоративный бетон может стать отличным материалом для дорожек и превосходным решением при оформлении приусадебной территории. Материал имеет превосходные качественные характеристики и отличается эстетичностью. Покрытие удобно для уборки и обладает устойчивостью к маслу и жиру.
Площадки с таким покрытием не требуют установки бордюра, благодаря этому можно сэкономить на строительстве. При желании вы можете сделать своими руками декоративный бетон. Формы и сухую смесь для приготовления можно приобрести в строительном магазине. Оформление будет зависеть от предпочтений хозяина. Вы можете приобрести силиконовую или пластиковую форму, которая может состоять из квадратов и ромбов.
Декоративное покрытие из бетона создается следующим образом. На первом этапе необходимо подготовить поверхность. При изготовлении дорожки на выбранной территории вы должны будете снять грунт, углубившись на 10 см. В полученное пространство устанавливается опалубка, а на дно насыпается слой щебня.
Методика проведения работ
На выровненную поверхность необходимо выложить цементный раствор и разгладить его поверхность. Далее можно заняться нанесением отвердителя. Он обычно имеет определенный цвет. Это позволит придать поверхности оттенок. Воспользоваться предстоит сухим красителем. Вы можете выбрать материал, в который, помимо красящих пигментов, входит наполнитель из кварцевого песка или гранита.
Декоративный бетон, фото которого представлены в статье, на следующем этапе прессуется формами. На немного схватившуюся, но еще не полностью застывшую поверхность необходимо выложить формы, которые хорошо прижимаются друг к другу. Для того чтобы сформировать четкий отпечаток, форму необходимо утрамбовать.
Готовность бетонной смеси к штампованию можно определить, дотронувшись до материала пальцем. Смесь считается готовой, если материал не тянется за рукой. После выдержки материала в течение нескольких дней нужно отмыть покрытие с помощью щетки. Она смачивается в растворе соляной кислоты. Как только верхний слой высохнет, можно начинать нанесение защитного состава, что будет препятствовать испарению влаги со свежего бетона.
Изготовление декоративного бетона предусматривает формирование деформационных швов, которые будут располагаться в местах вероятного излома материала. Расстояние между швами составит 6 м. Пустоты заполняются бесцветным герметиком. Для того чтобы продлить срок эксплуатации бетона и улучшить его эстетические характеристики, поверхность рекомендуется обработать пропиточным составом, который образует защитную пленку.
Информация о составе
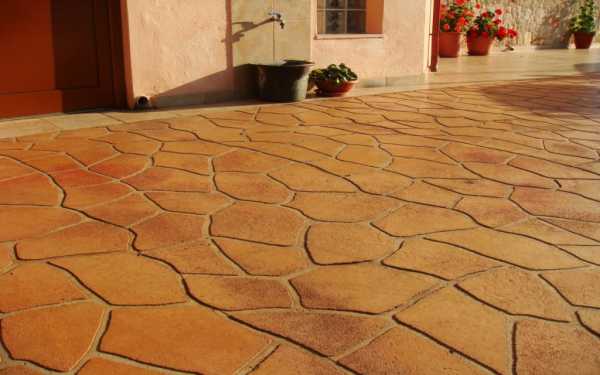
Описываемый материал — это композитная масса, которая состоит из следующих компонентов:
- крупнофракционного заполнителя;
- цемента;
- присадки;
- мелкого заполнителя;
- воды;
- красителя.
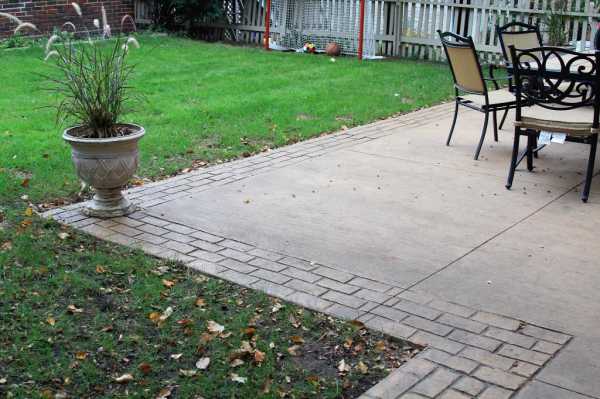
Именно состав отличает декоративную смесь от обычного бетона. Это обуславливает возможность изготовления из смеси почти любой конструкции. Например, материал может лечь в основу лепнины или тротуарной плитки, а также брусчатки. В качестве одного из основных преимуществ такого состава выступает его высокая устойчивость к истиранию.
Если вы задумались над вопросом о том, как сделать декоративный бетон, то должны для начала разобраться в основных его разновидностях. Среди прочих следует выделить цветной бетон, который имитирует архитектурные и художественные формы по типу фигур и фонтанов. Натуральный камень можно имитировать с помощью печатного или штампованного бетона.
Каждая разновидность декоративной смеси имеет свое назначение. Например, цветной бетон наиболее часто используется при формировании тротуарной плитки. Это позволяет получить более выразительные изделия. А вот художественный бетон используется для отделки зданий. Из него можно изготавливать разные фигуры для благоустройства приусадебной площади. Бетон в имитации камня используется для изготовления фасадной плитки, цоколя и отмостки.
Особенности использования микроцемента

Декоративная штукатурка под бетон — это относительно новое покрытие, которое еще называется микроцементом. В итоге удается получить поверхность, которая имитирует бетон. Перед началом работ необходимо подготовить основание, которое следует очистить, высушить и избавить от явных дефектов. Далее осуществляется укладка армирующей сетки и нанесение эпоксидной смолы. На поверхность укладывается сетка с отступом от стен и углов 2 см.
Арматуре необходимо позволить отлежаться и выпрямиться в течение 10 часов. После на нее валиком или распылителем наносится раствор смолы с отвердителем. Использовать при этом необходимо пропорцию 2 к 1. На свеженанесенную смолу необходимо рассеять кварцевый песок, фракция которого варьируется от 0,8 до 1,2 мм. Рекомендованное время высыхания — 24 часа.
Как только эпоксидная смола высохнет, необходимо постараться устранить неровности с помощью наждачной бумаги, зерно которой составляет 40 или 60. Далее можно приступать к нанесению грунта «Бетоноконтакт». Использовать для этого необходимо валик, с помощью которого смесь удобно распределяется по поверхности. В таком состоянии основание оставляется на 24 часа, затем можно приступать к нанесению базы. Но перед этим необходимо смешать материалы в отдельной емкости. Полученный состав смешивается с полимером, только после можно переходить к нанесению первого слоя.
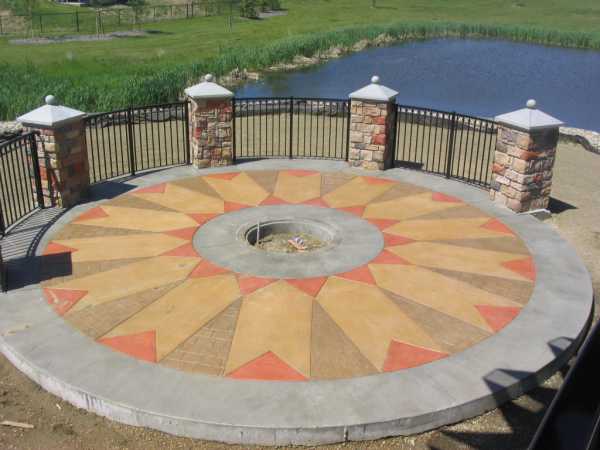
Микроцемент распределяется широким шпателем из нержавеющей стали. Для пола почти всегда требуется нанесение смеси в 2 слоя. Перед каждым новым слоем необходимо дождаться полного высыхания предыдущего. После этого можно наносить второй слой, который будет финишным. Микроцемент наносится тонкими слоями. После схватывания материала, что произойдет примерно через 15 минут, темные следы, оставляемые шпателем, необходимо пригладить. Толщина каждого слоя не должна быть больше 1 мм. Суммарная толщина составляет 3 мм максимум. Полное высыхание каждого слоя происходит за 24 часа.
Изготовление панелей своими руками
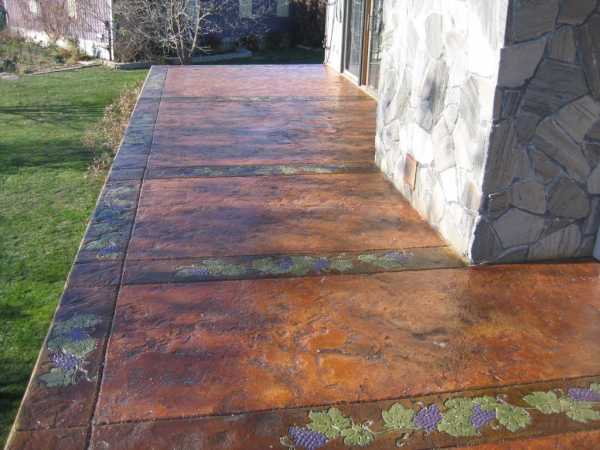
Декоративные панели из бетона можно выполнить самостоятельно. Смотрятся они довольно эффектно, а использовать их можно при оформлении не только внешних, но и внутренних стен здания. В основу может лечь все тот же бетон, состав которого был описан выше. Однако вы должны приобрести интересные формы, которые и будут составлять рисунок поверхности.
После затворения смеси ее разливают по формам, а после застывания производится распалубка. Изделия должны вылежаться, только после их можно использовать для монтажа. Установка осуществляется на все тот же цементный раствор. Однако можно использовать и специальный клей. Он должен быть достаточно надежным, чтобы выдержать нагрузку изделий, которые обладают внушительным весом.
В заключение

Для того чтобы выполнить декоративный бетон в имитации кирпича, а также камня и других материалов, следует сформировать поверхность из смеси, а затем осуществить нанесение кислотного красителя. Он укладывается несколькими слоями. Состав вступает в реакцию с раствором, благодаря чему удается получить необходимый цвет. Оттенок можно дополнить разными эффектами. Краситель наносится несколькими методами, в частности, по технологии напыления. Для создания красивой фактуры или получения уникального изображения можно использовать трафареты.
www.nastroy.net