виды, устройство, обзор лучших производителей
Годы идут, наука и техника двигаются вперед, а твердые виды топлива по-прежнему остаются востребованными. Сжигать дрова в традиционной печи или в буржуйке не слишком эффективно, но ситуацию изменили пиролизные котлы отопления – агрегаты отличаются высоким КПД и относительно простой эксплуатацией.
Согласитесь, это достаточно значимые аргументы при обустройстве автономного отопления. Если вы подыскиваете эффективный котел для дома, то стоит внимательнее присмотреться к пиролизным котлам.
Мы расскажем, как устроены и работают агрегаты длительного горения, в чем их технико-эксплуатационные особенности, а также приведем обзор наиболее рейтинговых моделей отечественных и зарубежных производителей.
Содержание статьи:
Что такое пиролиз
Дрова – это, пожалуй, самое первое топливо в человеческой истории. Практически каждому известно, как быстро они сгорают на открытом воздухе, и что тепла при этом выделяется не так уж и много. Но ситуация кардинально изменяется, если создать иные условия для процесса сгорания.
Так называемое пиролизное горение осуществляется в закрытых камерах. Туда загружают дрова или иное твердое топливо подобного типа: пеллеты, опилки, отходы древесного производства и т.п.
Топливо поджигают и затем сокращают количество воздуха, поступающего в камеру.
Галерея изображений
Фото из
К пиролизным котлам относят все твердотопливные теплогенераторы длительного горения, перерабатывающие твердый тип топлива
Значительную часть тепловой энергии, поставляемой котлами длительного горения, дает процесс сгорания пиролизных газов
В пирокотле сложные химические соединения расщепляются на более простые компоненты под воздействием высокой температуры без применения реагентов
В результате термической обработки топливо выделяет газ, который проще и легче горит. Потому пиролизные котлы относят к разряду газогенераторных
В пиролизном агрегате непрерывно происходит выделение огромного количества тепловой энергии, а отбираться может только необходимый ее объем
Желающим сделать пирокотел собственными руками следует учесть, что из-за непрерывно происходящих процессов высокотемпературного горения для изготовления топки нужна жаростойкая футеровка
По схеме горения пиролизные котлы делят на агрегаты естественного и принудительного типа. Естественные дешевле, но менее эффективны, чем принудительные, оборудованные наддувом
По специфике обслуживания систем пирокотлы делятся на одно-и двухконтурные. Первые предназначены только для отопления, вторые обслуживают отопление и ГВС
Пиролизные котлы заводского производства
Схема увеличения производительности агрегата
Принцип действия и эффективность пиролизного котла
Газогенераторная основа работы оборудования
Экономические преимущества пирокотла
Специфическая особенность самоделок
Естественный и принудительный тип горения
Одноконтурное пиролизное оборудование
Как известно, при горении происходят окислительные процессы, один из главных участников которых – кислород, содержащийся в воздухе. Если кислорода мало, реакция замедляется и дрова сгорают медленно, фактически в таких условиях они просто тлеют. При этом выделяется некоторое количество тепловой энергии, зола и горючий газ.
Процесс пиролиза на этом не заканчивается. Полученный при сжигании первичного топливо газ смешивается с воздушными массами и также сгорает. В итоге тепловой энергии выделяет значительно больше, чем при работе стандартных теплогенераторов.
Поэтому пиролизные котлы демонстрируют очень приличный КПД по сравнению со своими чисто , а также нередко предоставляют возможность заметно сэкономить на отоплении.
Преимущество отопительной техники этого типа состоит в том, что принцип ее работы и устройства относительно не сложен. Количество воздуха, поступающего в камеры сгорания, регулируется обычной механической заслонкой. Простая конструкция обеспечивает надежность устройства, поломки для пиролизных котлов – явление не частое.
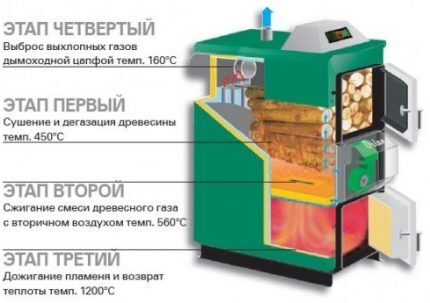
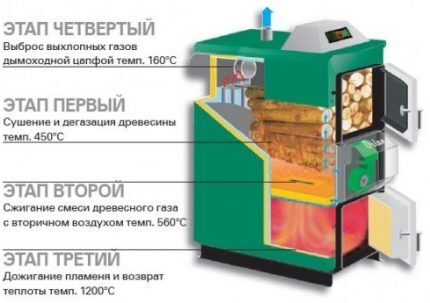
Эта схема наглядно демонстрирует все этапы процесса пиролизного горения. Температура внутри устройства может достигать 1200°С (+)
Еще один “плюс” пиролизных котлов – длительный период горения. Полная загрузка устройства топливом позволяет не вмешиваться в процесс в течение нескольких часов, иногда и более суток, т.е. нет необходимости постоянно подбрасывать дрова в топку, как это происходит при открытом горении.
Конечно, это не означает, что пиролизный котел можно оставлять без присмотра. Как и в отношении прочей отопительной техники, здесь имеются строгие правила техники безопасности.
Стоит помнить, что пиролизный котел не всеяден – влажность топлива должна быть невысокой. Иначе часть драгоценной тепловой энергии уйдет не на подогрев теплоносителя, а на высушивание топлива.
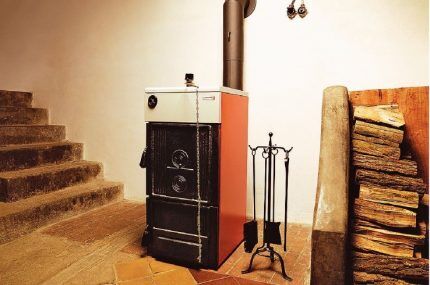
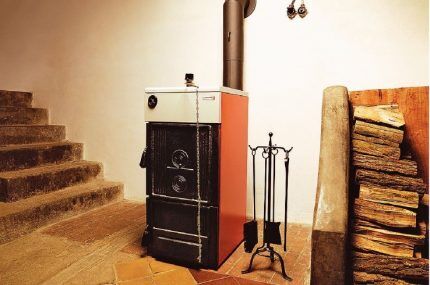
Котлы пиролизного горения, особенно выполненные из чугуна, обладают значительным физическим весом, поэтому они всегда представлены только напольными моделями
При реализации пиролизного горения топливо сгорает почти полностью, чистить устройство придется гораздо реже, чем при эксплуатации традиционного твердотопливного котла. Мелкую золу, полученную после очистки, используют в качестве удобрения. Горение топлива в таких котлах осуществляется по направлению сверху вниз.
Поэтому возможности для естественной циркуляции воздуха в топке заметно ограничены. Использование принудительного нагнетания воздуха с помощью вентилятора значительно улучшает эффективность работы устройства, но при этом делает котел энергозависимым, поскольку для работы вентилятора необходима электроэнергия.
Устройство и работа пиролизного котла
Топка пиролизного котла разделена на два отделения. В первой сгорают дрова, а во второй производится вторичное сгорание смеси пиролизных газов и воздуха. Отделяет первую камеру от второй колосниковая решетка, на которую и укладывают топливо.
Воздух обычно нагнетается принудительно с помощью небольшого вентилятора. Хотя в небольших моделях иногда для создания тяги используют дымосос.
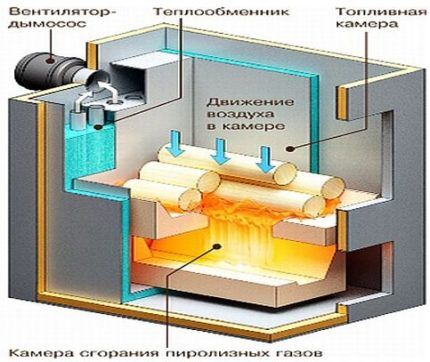
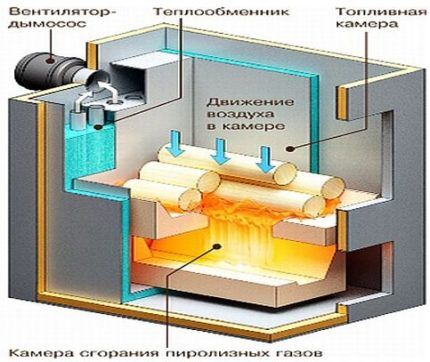
На этой схеме представлено устройство пиролизного котла нижнего горения. Дрова медленно сгорают при малом количестве кислорода и выделяют горючий газ (+)
Наличие принудительной вентиляции можно считать основным отличием пиролизного котла от классической твердотопливной модели. Корпус устройства состоит из двух частей, вставленных друг в друга. Пространство между стенками заполняют теплоносителем, роль которого традиционно выполняет вода.
Сначала в первое отделение топки пиролизного котла загружают топливо, затем включают вентилятор и поджигают топливо. Образующиеся в результате горючие газы перемещаются во второе отделение, смешиваются с воздухом и сгорают.
Температура горения может достигать 1200°С. Вода, находящаяся в наружном теплообменнике, нагревается и циркулирует по системе отопления дома. Остатки продуктов сгорания удаляются через дымоход.
В упрек устройствам, в работе которых используется пиролизный принцип горения, можно поставить относительно высокую цену. Обычный твердотопливный котел стоит значительно меньше. Но в котлах длительного горения дрова сгорают практически полностью, чего о классическом котле не скажешь.
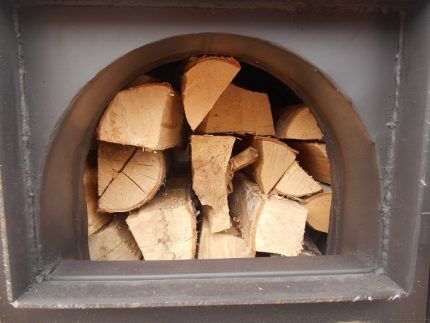
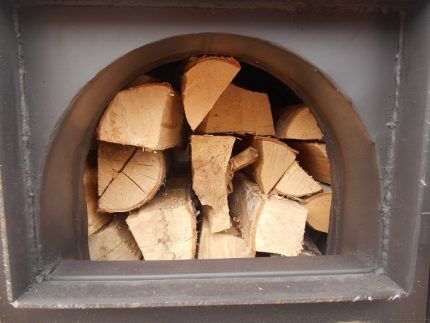
К дровам для пиролизного котла предъявляют определенные требования по размерам и влажности. Подробную информацию можно найти в инструкции изготовителя
Выбирая пиролизный котел, следует помнить, что недорогие модели малой мощности обычно рассчитаны только под дрова. Дорогие модификации способны работать на разных .
Причем загружать топливо в устройство придется по максимуму, снижение нагрузки приводит к повышенному образованию золы и сажи, а также негативно сказывается на работе агрегата в целом.
Котлы верхнего горения
Один из вариантов пиролизного устройства – котел верхнего горения. Принцип действия этих двух агрегатов очень схож.
Точно так же в топку загружают большое количество твердого топлива низкой влажности, воздух нагнетают принудительно и обеспечивают тление топлива при пониженном количестве кислорода. Задвижку, которая регулирует поток кислорода, устанавливают в нужном положении.
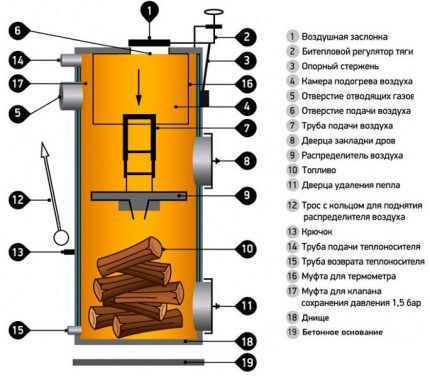
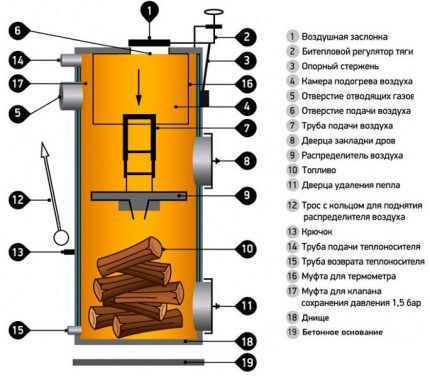
Схема устройства котла верхнего горения. Топка такого котла имеет глухое дно, частички продуктов горения удаляются через дымоход (+)
Но котлы длительного горения не имеют ни зольника, ни колосника. Дно представляет собой глухую металлическую плиту. Такие котлы устроены так, чтобы древесина сгорала полностью, а оставшееся в топке малое количество золы выдувалось воздухом.
Такие устройства отличаются высоким КПД и также работают при температурах более 1000°С.
Основная особенность таких устройств – они действительно обеспечивают длительный срок работы при полной загрузке. Топливная камера в таких устройствах обычно выполнена в форме цилиндра.
В нее сверху загружают топливо, сверху же, по центру, нагнетается необходимый для горения воздух.
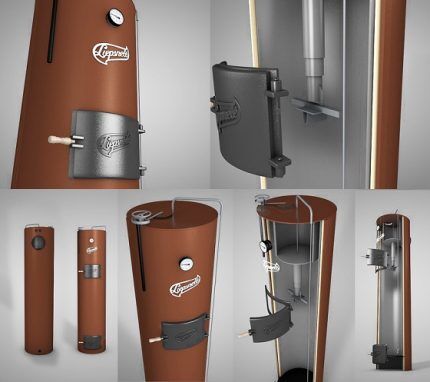
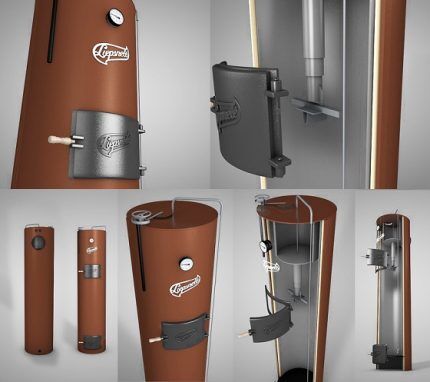
В котлах верхнего горения устройство для нагнетания воздуха – это подвижный элемент, который опускается вниз по мере прогорания дров
Таким образом осуществляется медленное тление верхнего слоя топлива. Топливо постепенно сгорает, его уровень в топке понижается. Одновременно изменяется и положение устройства для подачи воздуха в топку, этот элемент в таких моделях подвижен и он практически лежит на верхнем слое дров.
Второй этап горения осуществляется в верхней части топки, которая отделена от нижнего отделения толстым металлическим диском. Горячие пиролизные газы, образовавшиеся в результате сгорания топлива внизу, расширяются и перемещаются вверх.
Здесь они смешиваются с воздухом и сгорают, дополнительно передавая теплообменнику солидную порцию тепловой энергии.
Балка, удерживающая диск, который разделяет камеру сгорания на две части, как и сам этот диск, в процессе работы котла верхнего сгорания постоянно находится под воздействием высокой температуры. Со временем эти элементы сгорают, их придется периодически заменять.
На выходе из второй части топливной камеры обычно установлен регулятор тяги. Это автоматический прибор, который определяет температуру теплоносителя и в зависимости от полученных данных регулирует интенсивность движения горючего газа. Он защищает устройство от возможного перегрева.
Стоит отметить, что наружный теплообменник в таких котлах реагирует на изменение скорости циркуляции жидкости в теплообменнике, т.е. на колебания температуры. На поверхности устройства сразу же образуется слой конденсата, который вызывает коррозию, особенно если речь идет о стальных котлах.
Предпочтительнее брать устройство из чугуна, которое значительно лучше сопротивляется подобному воздействию.
Хотя топливо в пиролизных котлах длительного горения должно сгорать без остатка, на практике так бывает не всегда. Порой пепел спекается, образуя частички, которые трудно удалить с помощью потока воздуха.
Если в топке накопится большое количество таких остатков, может наблюдаться заметное снижение тепловой отдачи агрегата. Поэтому котел верхнего горения следует периодически все же прочищать.
Особенность устройств этого типа в том, что по мере сгорания топлива его можно догружать, не дожидаясь сгорания всей закладки топлива. Это удобно, когда нужно избавиться от горючего бытового мусора.
Существуют также разновидности котлов верхнего горения, которые работают не только на древесном топливе, но и на угле. Сложные узлы автоматического управления в пиролизных котлах этого типа отсутствуют, поэтому серьезные поломки наблюдаются крайне редко.
Конструкция котла верхнего горения позволяет загружать топку лишь частично, если это необходимо. Однако в этом случае выполнить розжиг верхнего слоя топлива может быть не просто. Само топлива должно быть подсушенным, дрова из открытой поленницы для такого котла не подходят.
Топливо крупных фракций также не следует использовать для этого вида техники, т.е. дрова придется обязательно колоть на небольшие части.
Особенности эксплуатации газогенераторных котлов
Эффективность работы пиролизного котла во многом зависит от типа и качества топлива. Технически в топку можно загрузить не только древесину, но и уголь, и даже торф, большинство современных моделей котлов рассчитаны на использование нескольких видов топлива.
Древесина сгорает примерно за 5-6 часов, в зависимости от сорта. Чем тверже дерево, тем дольше оно горит.
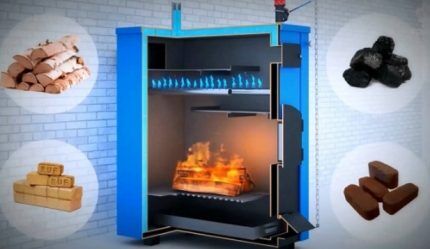
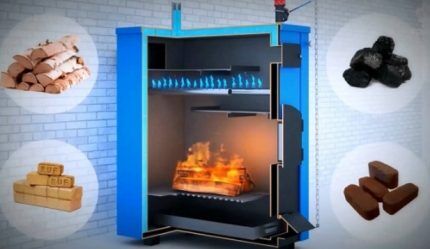
Современные модели котлов пиролизного горения могут работать на различных видах древесного топлива: дровах, брикетах, пеллетах, угле, торфе и т.п.
Около десяти часов уйдет на сгорание черного угля, а такое же количество бурого угля будет тлеть в течение восьми часов. На практике самую высокую теплоотдачу пиролизная техника демонстрирует при загрузке сухим деревом. Оптимальными считаются дрова влажностью не более 20%, а длиной около 45-65 см.
Если доступа к такому топливу не имеется, можно использовать уголь или другое органическое топливо: специальные и пеллеты из древесины, отходы, полученные при обработке дерева, торф, материалы с целлюлозой и т.п.
Перед началом эксплуатации котла следует внимательно изучить рекомендации производителя устройства в отношении топлива.
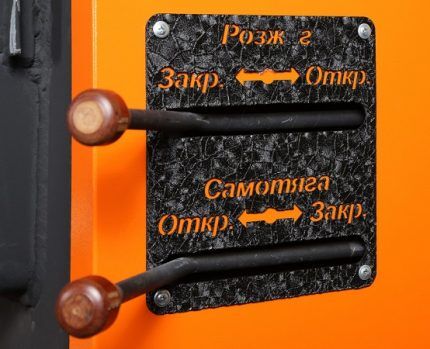
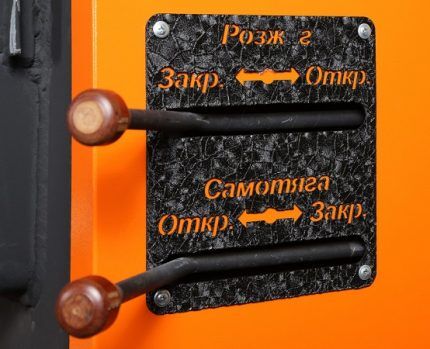
В котлах пиролизного горения поступление воздуха регулируется обычными механическими задвижками. Отсутствие сложной электроники обеспечивает высокую отказоустойчивость прибора
Слишком влажное топливо в таких устройствах недопустимо. При его сгорании в топке образуются дополнительные водяные пары, которые способствуют образованию таких побочных продуктов, как деготь и копоть.
Стенки котла загрязняются, теплоотдача снижается, со временем котел может даже прекратить работу, затухнуть.
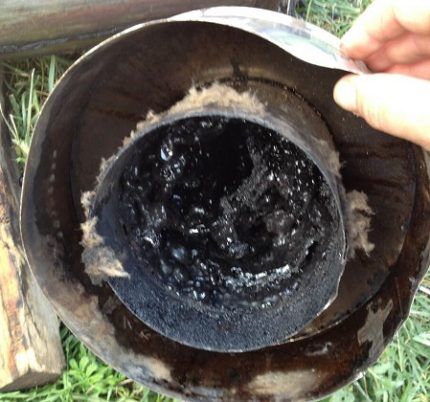
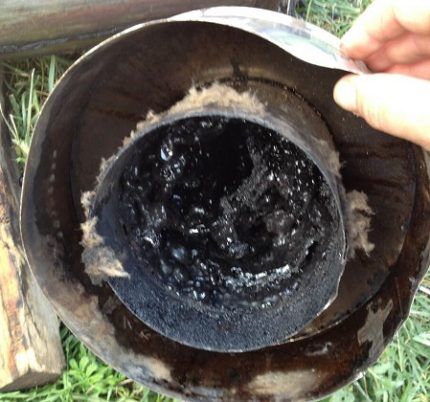
Если использовать для котла пиролизного горения дрова со слишком высокой влажностью, внутри устройства возникнут условия для образования дегтя, который ухудшит теплоотдачу устройства и может привести к поломкам
Если в топку заложено сухое топливо и котел настроен правильно, пиролизный газ, полученный в результате работы устройства, будет давать пламя желто-белого цвета. Такое горение сопровождается ничтожным выделением побочных продуктов сгорания топлива.
Если цвет пламени окрашен иначе, имеет смысл проверить качество топлива, а также настройки прибора.
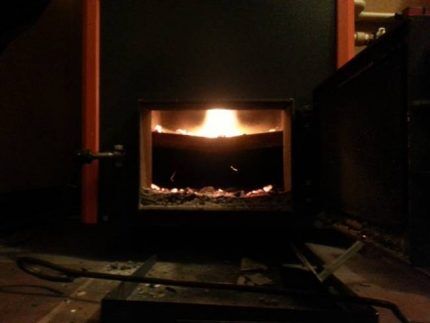
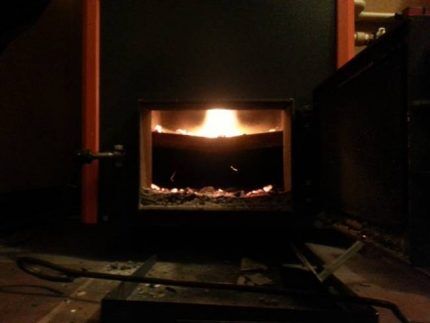
Пиролизные газы, смешанные с воздухом, горят ровным желто-белым пламенем. Если цвет пламени изменился, возможно, нужно проверить настройки котла или качество топлива
В отличие от обычных твердотопливных устройств, перед загрузкой дров в пиролизные котлы, работающие на твердом топливе, топку следует разогреть.
Для этого выполняют следующие шаги:
- Загружают на дно топки мелкую сухую растопку (бумагу, щепу и т.п.)
- Поджигают ее с помощью факела из подобных материалов.
- Закрывают дверцу камеры сгорания.
- Дверцу загрузочной камеры оставляют немного приоткрытой.
- Добавляют порции растопку по мере ее сгорания.
- Процесс повторяют до тех пор, пока на дне не образуется слой тлеющих углей.
К этому моменту топка уже прогревается примерно до 500-800°С, создавая условия для загрузки основного топлива. Не следует использовать для розжига растопки бензин, керосин или любые другие подобные жидкие вещества. Перед тем, как прогревать топку котла длительного горения, следует убедиться, что устройство готово к эксплуатации.
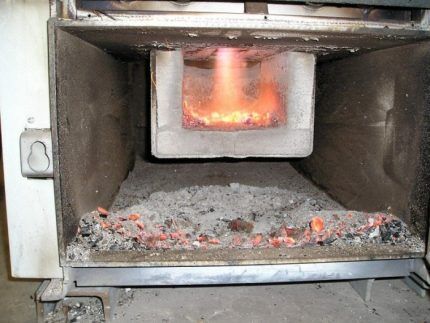
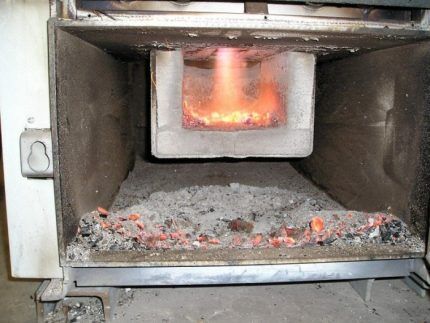
Характерная особенность котлов пиролизного горения – малое количество золы и пепла, что облегчает процесс очистки устройства и его обслуживания
Для этого проверяют наличие тяги, герметичность дверок, исправность запорных механизмов и регулировочной аппаратуры, наличие и т.п.
Затем следует включить терморегулятор, чтобы убедиться, что на прибор поступает напряжение. После этого открывают шибер прямой тяги и вентилируют котел в течение 5-10 минут.
Обзор популярных моделей
Следует понимать, что любой пиролизный котел – это достаточно тяжелый агрегат, который не предназначен для подвешивания на стену. Такие устройства можно применять как для отопления небольшого дома, так и для просторных коттеджей. Как и другие отопительные агрегаты, различаются по мощности.
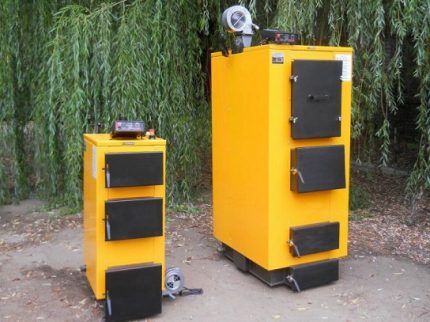
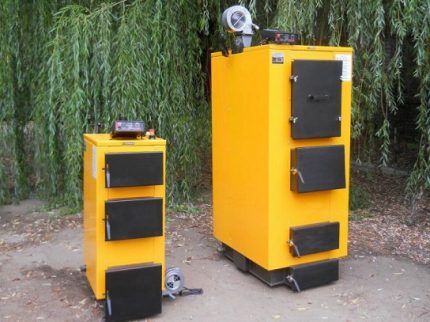
Выбирая котел пиролизного горения, следует ориентироваться на такие показатели, как тепловая мощность устройства, размеры камеры загрузки, наличие второго контура и т.п.
На этот показатель обычно и ориентируются покупатели.
Среди популярных моделей такой техники следует упомянуть:
- Atmos (Украина) – представлены устройствами, которые могут работать и на дровах, и на угле, мощность варьируется в пределах от 14 до 75 киловатт.
- Attack (Словакия) – способны справиться с обогревом площадей до 950 кв. м, некоторые модели способны продолжать работу даже при перебоях с электроэнергией.
- Bosch (Германия) – высококачественная продукция известного бренда, мощность варьируется в пределах 21-38 киловатт.
- Buderus (Германия) представлена линейками Elektromet и Logano, первая хорошо известна в Европе как классический вариант пиролизного котла, вторая – более современные версии, предназначенные для частных домов.
- Gefest (Украина) – высокомощные устройства с КПД до 95%.
- КТ-2Е (Россия) специально разработан для крупных жилых помещений, мощность агрегата составляет 95 киловатт.
- Opop (Чехия) – относительно недорогие котлы, надежные и долговечные, мощность 25-45 киловатт.
- Stropuva (производства Литвы или Украины) с мощностью от семи киловатт вполне подойдут для небольшого дома, но в модельном ряде представлены и более мощные устройства.
- Viessmann (Германия) – идеальный выбор для частных домовладений, мощность стартует с 12 киловатт, применение современных технологий позволяет экономить топливо.
- “Буран” (Украина) с мощностью до 40 киловатт еще один популярный вариант для владельцев больших коттеджей.
- “Логика” (Польша) высокомощные устройства на 20 киловатт с легкостью обогревают помещения площадью до 2 тыс. кв. м, это скорее котел для промышленных нужд: обогрева цехов, офисов, теплиц и т.п.
Выбирая пиролизный котел для частного дома, следует обратить внимание на модели с двумя контурами, чтобы не только отапливать жилище, но и обеспечить его автономным горячим водоснабжением.
Теплообменник для ГВС бывает накопительного или проточного типа. Для последнего варианта используют модели котлов повышенной тепловой мощности.
При желании сэкономить средства, можно попробовать сделать пиролизный котел своими руками. Технология его сборки описана в .
Выводы и полезное видео по теме
На этом видео наглядно изображен принцип работы пиролизного котла:
Подробный обзор работы котла верхнего горения можно посмотреть здесь:
Пиролизные котлы недешевы, но полностью оправдывают вложенные в их приобретение средства. При правильной установке и обслуживании такие устройства обеспечат дом стабильным и недорогим теплом.
Подыскиваете пиролизный котел для отопления дома? Или есть опыт эксплуатации таких агрегатов? Оставляйте, пожалуйста, комментарии к статье и делитесь впечатлениями об использовании пиролизных котлов. Форма обратной связи расположена в нижнем блоке.
Пиролизные котлы для отопления частного дома своими руками: чертежи и видео
Содержание статьи:
Одним из решений проблемы обогрева дома могут стать пиролизные котлы отопления на твердом топливе — эффективные в работе и неприхотливые в эксплуатации. Однако высокая стоимость отопительных устройств заводского изготовления заставляет потенциального покупателя задуматься: а не попробовать ли самому сделать пиролизный котел? Для работящего человека с техническими навыками это вполне по силам. Наша статья поможет понять, как происходит процесс горения в пиролизном котле для отопления частного дома, из каких материалов его можно смонтировать и как подключить к отопительной системе.
Особенности пиролизных отопительных устройств
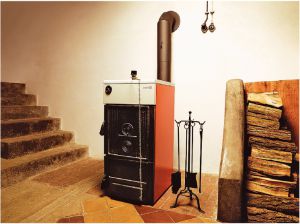
Пиролизный котел служит генератором тепла в домашней системе отопления
Главным отличием пиролизного твердотопливного котла отопления (газогенераторного) считается особый принцип горения топлива. Если в обычных котлах дрова или уголь просто горят открытым пламенем, то здесь процесс разделен на два этапа:
- Топливо загружают в топочную камеру и разжигают огонь. Когда температура превысит 400 °С, начинается процесс пиролиза — медленного тления топлива при недостатке кислорода. При этом выделяется тепло, дым и пиролизный газ, в состав которого входит окись углерода и различные углеводороды.
- Для перевода котла в рабочий режим закрывают заслонку прямой тяги и включают вентилятор. Газообразные продукты пиролиза вытесняются струей первичного воздуха в камеру сгорания, где они обогащаются кислородом от подачи подогретого вторичного воздуха. Смесь пиролизных газов и взвешенных частиц полностью сгорает и отдает свою тепловую энергию встроенному в котел теплообменнику.
Насколько экономичны и удобны пиролизные котлы отопления, подтверждают отзывы пользователей. Теперь им больше не нужно вставать по ночам, чтобы подбросить дровишек. Загруженная в котел очередная порция топлива будет потихоньку тлеть с вечера до позднего утра. Эффективность сгорания такова, что золы почти не остается, а из дымохода идет лишь легкий прозрачный дымок.
Для нормального протекания процесса пиролиза котел должен быть оборудован вентилятором, поэтому необходимо, чтобы электроснабжение в доме было бесперебойным.
Требования к самодельным пиролизным котлам
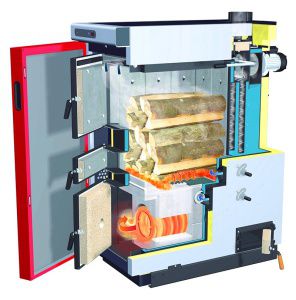
Схематическое устройство пиролизного котла
Для того чтобы пиролизный котел отопления, изготовленный своими руками, превзошел по эффективности обычный твердотопливный котел, его конструкция должна отвечать строгим требованиям:
- температура в топке должна быть оптимальной (600–700 °С), поскольку именно в этих условиях происходит наиболее качественное выделение продуктов пиролиза;
- регулирование мощности горения не должно существенно снижать КПД;
- котел отопления должен быть пригоден для длительного непрерывного сжигания топлива;
- корпус камеры сгорания пиролизных газов должен быть устойчив к коррозии и способен выдерживать температуру выше 1200 °С.
Желательно также, чтобы в конструкции котла была предусмотрена камера для предварительного подсушивания древесного сырья.
Технические характеристики, которыми должен обладать самодельный пиролизный котел для отопления частного дома:
Технические параметры
| Ед. изм. | Для небольших домов
| Для коттеджей |
Мощность | кВт | 15–25 | 35–50 |
КПД | % | 80 | 85 |
Максимальное рабочее давление | бар | 1,8–2,0 | 3,0–4,5 |
Макс. площадь отопления | м² | до 200 | до 500 |
Объем воды в теплообменнике | л | 18–25 | 40–65 |
Объем топки | л | 70–100 | 200–300 |
Использование самодельного отопительного устройства иногда бывает рискованным, поскольку при неправильно отрегулированном процессе горения может произойти так называемый «хлопок» — взрыв пиролизного газа.
Топливо для пиролизных котлов
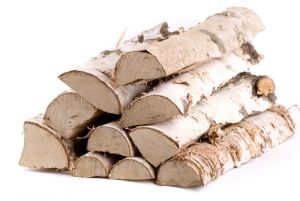
Древесина обладает наилучшей способностью образовывать газообразные горючие смеси в процессе пиролиза
Из всех видов топлива для пиролизного процесса лучше подходят дрова и различные древесные отходы. Кроме этого, в пиролизных котлах для отопления частного дома можно сжигать также уголь или торф, но эффективность будет несколько меньше.
Толщина поленьев не имеет большого значения, а их длина ограничивается только габаритами топочной камеры. Главное условие — чтобы среди них не попадалась гниль и труха. Если кроме дров использовать для сжигания опилки и стружку, их объем не должен превышать 1/3 часть от общей загрузки топлива.
Древесное топливо должно быть сухим, влажностью не более 20–25%. В противном случае его сгорание будет неполным, теплоотдача снизится, а дымовая труба забьется сажей и дегтем.
Пиролизный котел своими руками
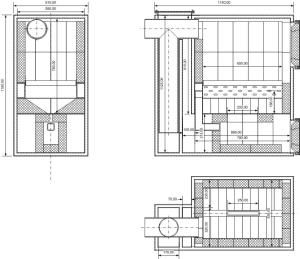
Один из вариантов конструкции отопительного котла, развивающего мощность 45 кВт
Чтобы сделать котел отопления пиролизный твердотопливный, самодеятельному мастеру придется для начала изучить доступную информацию по этому вопросу.
В рамках нашей статьи мы в состоянии дать только общие рекомендации, а подробные чертежи можно поискать в интернете. Полезно также заглянуть на форумы, где специалисты обмениваются мнениями.
По их отзывам, пиролизные котлы отопления делать своими руками все же обойдется дешевле, чем покупать фирменные.
Мощность пиролизного котла определяют несколько факторов, и главные среди них: общие габариты изделия, объем камеры горения и высота подачи первичного воздуха.
Любую готовую схему системы отопления с пиролизным котлом нужно будет доработать с учетом конкретных условий своего жилища.
Материалы и технология изготовления
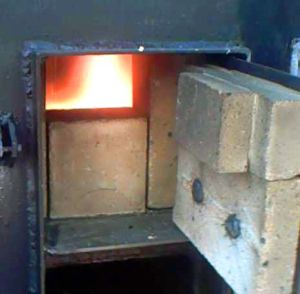
Высокую температуру горения пиролизного газа может выдержать только огнеупорный кирпич
Для изготовления пиролизного котла отопления своими руками понадобится:
- электросварочный аппарат и хороший запас электродов;
- «болгарка» и к ней не менее 20 отрезных кругов;
- сталь 4мм, 3 листа 1,25×2,5 м;
- сталь 2 мм, один лист;
- труба 57 мм общей длиной 8 м;
- шамотный кирпич, 12—14 шт.;
- и еще некоторые мелкие детали.
Раскроить металл и выполнить сварочные работы — задача не из легких. Если нет возможности заняться этим самостоятельно, придется пригласить мастера.
Дверцы котла должны закрываться герметично, чтобы не терялось тепло и не выходил наружу дым.
Испытание готового котла
В ходе испытания должны быть выявлены недостатки самодельного отопительного котла и определены способы их устранения. Качественно смонтированный пиролизный агрегат обладает следующими свойствами:
- топливо разгорается достаточно легко при естественной тяге;
- дым не вырывается из-под уплотнителя верхней дверцы;
- вентилятор обеспечивает стабильный поток воздуха и не шумит;
- котел за 20-30 минут выходит на рабочий режим;
- при включении вентилятора пламя в камере сгорания сильное и ровное;
- процесс сжигания пиролизного газа поддается регулированию;
- при остановке вентилятора не возникает эффекта обратной тяги;
- соотношение тепловой мощности к затраченному количеству дров соответствует расчетам.
Если самодельный отопительный котел демонстрирует соответствие этим параметрам, его можно признать работоспособным после устранения обнаруженных недоделок.
Схемы подключения пиролизного котла к отоплению
Тепло в доме зависит от того, правильно ли устроена система отопления с пиролизным котлом и соответствует ли норме режим топки. Все нюансы нужно предусмотреть на этапе составления проекта. Отопление дома может производиться как с помощью горячей воды, так и воздушным способом.
При разработке системы отопления нужно неукоснительно следовать специальным рекомендациям и нормам техники безопасности.
Водяное отопление
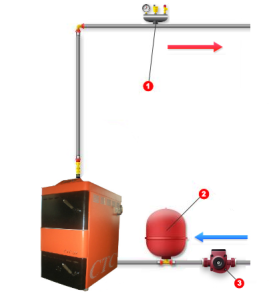
Кроме котла, в системе установлены: 1 – группа безопасности, 2 – расширительный бак, 3 – циркуляционный насос
Монтаж пиролизного котла отопления на твердом топливе должен производиться в помещении, специально отведенном под котельную. Кроме самого котла, здесь следует разместить такие элементы отопительной системы, как циркуляционный насос, запорная арматура, расширительная емкость, датчики, термометры и другие устройства. В той же котельной есть смысл оборудовать место для поленницы дров недалеко от котла, чтобы не приходилось часто выходить за ними на мороз.
Непосредственное подключение пиролизного котла к системе отопления может быть выполнено по-разному. На следующем рисунке показан наиболее простой способ подключения.
Другие способы подключения пиролизного котла к водяной системе отопления:
- с контуром подмеса — к перечисленным выше элементам системы добавляется дополнительный контур и краны, регулирующие количество нагреваемой воды;
- с гидрострелкой — эта схема лучше всего проявляет себя в системах отопления с несколькими контурами;
- с аккумулирующим баком — подогрев воды происходит посредством ее поступления из бака и позволяет оптимизировать работу котла даже без электричества.
Выбирая схему подключения к отопительной системе пиролизного котла, желательно просчитать стоимость каждого варианта, чтобы найти среди них оптимальный.
Воздушное отопление
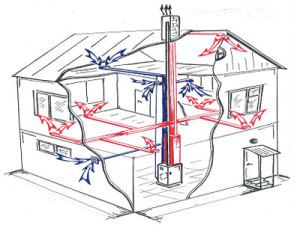
Схема распределения воздушных потоков при обогреве дома от пиролизного котла воздушного отопления
Домовладельцы используют пиролизный котел воздушного отопления чаще всего не для обогрева дома, а для гаражей, складов, теплиц и других хозяйственных помещений. Метод отопления жилых комнат подогретым воздухом пока еще не получил распространения. Но и здесь использование пиролизного котла могло бы продемонстрировать его преимущества. Например, система воздушного отопления особенно актуальна, когда хозяева загородного дома озабочены тем, чтобы водяная отопительная система не разморозилась за время их длительного отсутствия.
Система, использующая пиролизные котлы воздушного отопления, состоит из одного или нескольких вентиляторов, термодатчиков, блока управления и сети воздуховодов для транспортирования горячего воздуха к местам обогрева.
В какой бы из систем отопления ни использовались котлы отопления пиролизные твердотопливные, для их безотказной работы необходимо утеплить дымовую трубу, чтобы на ее стенках не образовывался конденсат.
В заключение
Анализируя отзывы о пиролизных котлах отопления, можно составить впечатление об их несомненных достоинствах. В условиях постепенного удорожания природного газа все чаще становится оправданным решение устроить систему отопления с пиролизным котлом собственноручного изготовления. Многих пользователей привлекает автономность такой системы и простота ее эксплуатации.
Посмотрите видео, как сделать своими руками достаточно простую модель пиролизного котла:
Тем, кому невозможно подсоединиться к центральному газоснабжению, пиролизные котлы отопления на твердом топливе станут надежными помощниками в деле обогрева жилья. Но если вы решили сэкономить, тогда вашим решением будет самостоятельное изготовление отопительного устройства. Монтаж и подключение пиролизного котла к системе отопления будет доступным для людей, имеющих инженерные и слесарные навыки.
Лучший выбор пиролизных отечественных и импортных котлов.
При отсутствии магистрального газоснабжения котлы, работающие на твердом топливе, становятся оптимальным вариантом отопления. Они просты в обслуживании и достаточно эффективны. Но где купить пиролизные котлы длительного горения по выгодной цене? Решение этого вопроса доверьте нам. Наш интернет-магазин Купитькотлы.РФ занимается реализацией отопительного оборудования не первый год, поэтому предлагает своим клиентам только лучшие модели котлов. Если Вы проживаете в Санкт-Петербурге или любом другом городе России, можете выбирать наш интернет-магазин Купитькотлы.РФ. Вас приятно удивит наш ассортимент. Ваш заказ может быть доставлен в любую точку РФ удобной вам транспортной компанией.
Преимущества пиролизных котлов
Твердотопливный пиролизный котел прекрасно подойдет как для обогрева жилого дома, так и для офиса или промышленного сооружения. В качестве топлива такое оборудование может использовать дрова, древесные отходы, специальные брикеты и пеллеты. Кроме того, в последнее время распространение получили пиролизные котлы, работающие на угле и коксе. Стоит отметить некоторые особенности такого обогревателя, а именно:
- выход оборудования на заявленную производительность занимает от получаса до часа, за это время котел нагревается до 60-90°C и прогревает систему отопления;
- малый расход твердого топлива, по сравнению с котлами прямого горения, экономия до 3 раз;
- увеличенный срок горения на одной закладке до 16 часов;
- котел имеет высокую производительность – до 92%, а благодаря тому, что топливо сгорает полностью, зола отсутствует;
- наличие котлов любых мощностей от 10 кВт до 2,5 мВт;
- благодаря наличию современной автоматики, обогреватель способен поддерживать стабильную температуру в течение всего времени работы.
Важно также то, что для корректного функционирования системы необходимо оборудовать правильно дымоход.
Как заказать у нас?
Чтобы приобрести пиролизный котел у нас, достаточно заполнить форму заказа. Остались вопросы? Не стеснитесь и задавайте их нашим квалифицированным специалистам по номеру: +7 (812) 947-69-80. Наши консультанты всегда будут рады помочь Вам определиться с выбором. Также Вы можете отправить Ваш вопрос на адрес электронной почты или заказать бесплатный обратный звонок с сайта.
Как выбрать дровяной пиролизный котел
или,
что нужно знать,
покупая дровяной пиролизный котёл
- Что такое пиролиз древесины
- Поджиг и горение древесины
- Что такое пиролизное горение древесины
- Что такое дровяной пиролизный котёл
- Топливо для пиролизного котла
- Работа дровяного пиролизного котла (видео)
- Как выбрать дровяной пиролизный котёл
- Что делать с дровяным пиролизным котлом после его покупки
(шуточные советы от производителя)
Дополнительно:
- Ностальгия по газовой идиллии
- Газовое отопление – непозволительная роскошь
- Дровяное отопление – как вариант
–=|=–
Что такое пиролиз древесины
Пиролиз – это разложение вещества под воздействием температуры.
Пиролиз древесины – это термическое разложение древесного вещества.
Под воздействием температуры древесина разлагается на продукты пиролиза древесины – углерод (древесный уголь) и летучие углеводороды (пиролизный газ). Продукты пиролиза древесины – горючие вещества. Когда дерево горит – мы видим горение (окисление) именно продуктов пиролиза древесины. Без предварительного пиролиза (термического разложения) древесина гореть не будет. Предварительный пиролиз древесного вещества – это обязательное условие горения древесины. В любом костре и печке, на кончике горящей спички и в бушующем лесном пожаре, обязательно происходит одно и тоже – непрерывно идёт термическое разложение (пиролиз) древесного вещества и горение (окисление) продуктов пиролиза древесины. Если древесина не горит – значит нет достаточно сильного и эффективного процесса пиролиза древесного вещества, способного поддержать горение древесины.
Поджиг и горение древесины
Если древесину нагревать достаточно долго и сильно – начнётся её термическое разложение с последующим воспламенением продуктов пиролиза. Первый, вялотекущий процесс пиролиза древесины начинается уже при её нагревании до температуры 120°С…150°С. Потом, по мере нагрева – термическое разложение усиливается и становится заметно невооружённым глазом. При температуре 250°С…350°С наступает обугливание поверхности дерева и появляется белый дым. При этой температуре может наступить кратковременное воспламенение продуктов пиролиза. При дальнейшем нагревании древесины до 600°С, наступит непременное воспламенение этих самых продуктов температурного распада – образовавшегося древесного угля и пиролизного газа. Если зону воспламенения не переохладить – древесина загорится и будет гореть. Более подробно о процессе горения древесины можно почитать в статье «Обычное горение древесины».
Прим. Здесь и далее по тексту, под древесиной подразумеваются дрова и все остальное, из чего можно делать органические (углеводные) топливные брикеты.
Что такое пиролизное горение древесины
Принципиально, любое горение древесины является пиролизным, поскольку любому горению древесины предшествует её предварительный пиролиз – термическое разложение. Горение древесины не может быть никаким другим, как непременно – пиролизным.
Понятие «пиролизное горение древесины» пришло к нам из описания работы пиролизных котлов – отопительных агрегатов, имеющих специфическую двухкамерную конструкцию корпуса. Топливо (древесина) в таких пиролизных котлах горит сразу в двух камерах.
При этом:
Горение древесины с её предварительным пиролизом и последующим РАЗДЕЛЬНЫМ сжиганием твёрдых и газообразных продуктов пиролиза, получило название «пиролизное горение древесины»
Что такое дровяной пиролизный котёл
Дровяной пиролизный котёл – это отопительное оборудование, работающее на дровах и органических отопительных брикетах, по принципу пиролизного (раздельного) горения топлива. Поскольку, при таком раздельном горении топлива выделяется (генерируется) пиролизный газ, то пиролизные котлы часто называют «газогенераторными» или «газицирующими». Специалисты могут разделять эти понятия для тех случаев, когда это действительно важно. Для рядового-же потребителя нужно запомнить только одно:
Главное отличие пиролизного котла – это наличие двухкамерной конструкции корпуса, которая обеспечивает раздельное горение топлива
Более подробно про пиролизные котлы можно почитать в статье «Сага про пиролизные котлы»
Топливо для дровяного пиролизного котла
Топливом для пиролизного котла служат дрова и топливные брикеты (древесные и органические). В небольшом процентном соотношении (не более 15-25% от общей массы) можно добавлять щепу, опилки, стружку, мелкие деревоотходы и даже – пеллеты.
Несмотря на то, что пеллеты – это 100% древесина, они не могут служить основным топливом для пиролизного котла, из-за своей мелкой фракции. Минимальные размеры кусков топлива для пиролизного котла – 70-100мм в поперечнике, не менее.
Не могут служить топливом для пиролизного котла ископаемые энергоносители и продукты их переработки – газ, нефть, уголь и угольные топливные брикеты, а также резиноизделия и пластмассодержашие вещества.
Работа дровяного пиролизного котла (видео)
Порыскав по Сети, без труда нашёл хорошее видео про работу пиролизного котла. На экране чётко видно, что дрова (топливо) загружают в верхнюю (пиролизную) камеру. Там древесина тлеет и разлагается под воздействием высокой температуры. При этом выделяется горючий пиролизный газ. Затем, уже в нижней камере – этот газ сгорает, как обычный природный газ. Остатки древесины догорают в верхней камере.
Как выбрать дровяной пиролизный котёл
Ныне, дровяные пиролизные котлы не делает и не продаёт только ленивый. Оно и немудрено. Во времена топливных кризисов, дровяное отопление – это есть лакомый кусочек и бальзам на сердце. Тем не менее, НАСТОЯЩИЕ пиролизные котлы не каждому производителю и продавцу «по зубам». Потому как, вещь эта – очень материалоёмкая и громоздкая. А поскольку, «зря переть за тридевять земель» груду металла и керамики – никто не будет, то покупая пиролизный котёл – нужно сразу настраиваться на работу с отечественным производителем или хорошо налаженной дилерской сетью.
Вот с ними и нужно будет согласовать следующие вопросы, архиважные при покупке дровяного пиролизного котла:
Футеровка дровяного пиролизного котла
Футеровка обязательна для дровяного пиролизного котла.
И дело здесь, вовсе не в защите металла от прогорания.
Металлу-то, как раз ничего и не угрожает.
А вот сам процесс пиролиза древесины может пострадать от переохлаждения. Потому что, активное термическое разложение древесного вещества возможно только при температуре, не менее 600…800ºС. И, если топливо будет контактировать со стальными водоохлаждаемыми стенками корпуса котла (t=120…250ºС) – оно просто погаснет или будет плохо гореть. Получается, что футеровка пиролизного котла защищает зону горения топлива (дров) от переохлаждения.
Кроме этого, комплект футеровки любого пиролизного котла содержит пренаиважнейшую деталь, без которой работа пиролизного отопительного агрегата просто немыслима – это керамическое СОПЛО!
Пояснение важности сопла
– Абсолютно все пиролизные котлы обязательно имеют две камеры – камеру загрузочную (для пиролиза древесины) и камеру сгорания (для сжигания пиролизных газов). Эти две камеры, всенепременно соединены керамическим соплом, которое является главным атрибутом горения пиролизных газов.
– Керамическое сопло дровяного отопительного пиролизного агрегата – это его «ахиллесова пята». Сопло пиролизного котла выдерживает тепловые удары с амплитудой, почти в 600ºС, очень быстро изнашивается, разрушается и выходит со строя. Срок службы сопла, максимум 3-4года. После этого его нужно будет заменить.
И, если срок службы корпуса котла составляет 15-20 лет, а срок службы деталей его футеровки 3-4 года, то это значит лишь одно – периодически детали футеровки пиролизного отопительного агрегата нужно будет покупать у его производителя и менять.
Отсюда вывод – нужно брать продукцию известных производителей, у которых налажена дилерская сеть и не должно возникать проблем с покупкой запчастей.
Совет
– Если решили приобрести дровяной пиролизный котёл – попробуйте сразу купить к нему комплект футеровки. Ответ продавца будет бальзамом на сердце. Или она (футеровка, сопло) есть в продаже, или её нет. В любом случае – это избавит от больших проблем в будущем, ибо футеровка дровяных пиролизных котлов уникальна по своей конфигурации и купить её можно только у производителя.
Таким образом получается, что пиролизные котлы привязаны к своему производителю, потому что только у производителя пиролизного котла можно купить его футеровку
Толщина металла корпуса дровяного пиролизного котла
Ныне, чугунный корпус котла – большая редкость. Все современные дровяные котлы имеют цельносварной стальной корпус из листового металла. При выборе пиролизного дровяного котла – интересуйтесь толщиной металла его корпуса.
Вот, ориентировочная информация по толщине металла корпуса пиролизного дровяного котла в зависимости от его мощности:
16-60 кВт | Наружные части 4мм, внутренние части 5мм |
80-100 кВт | Наружные части 5мм, внутренние части 6мм |
140-190 кВт | Наружные части 6мм, внутренние части 8мм |
200-300 кВт | Наружные части 8мм, внутренние части 10мм |
Прим. Информация взята из техотдела одного из ведущих производителей дровяных пиролизных котлов.
Вес дровяного пиролизного котла
Из первых двух вопросов вытекает третий. Коль скоро было решено, что пиролизный отопительный агрегат должен иметь толстые стенки своего корпуса и толстую футеровку, то и вес его должен быть не шуточный. Так оно и есть. Пиролизные котлы – тяжёлая штука. И, если вес дровяного пиролизного котла меньше, соответственно – производитель сэкономил на металле или футеровке изделия.
Хороших и лёгких дровяных пиролизных котлов – не бывает
Вот ориентировочный вес пиролизных котлов в зависимости от их мощности:
16 кВт | 25 кВт | 32 кВт | 40 кВт | 60 кВт | 80 кВт | 100 кВт | 140 кВт | 190 кВт | 250 кВт | 300 кВт |
420 кг | 530 кг | 610 кг | 680 кг | 1050 кг | 2130 кг | 2260 кг | 3470 кг | 3780 кг | 4800 кг | 5100 кг |
Прим. Информация взята из техотдела одного из ведущих производителей дровяных пиролизных котлов.
Размеры дровяного пиролизного котла
Размеры дровяного пиролизного котла слагается из совокупности размеров камер сгорания плюс размеры теплообменника. Должно быть, не менее:
Мощность котла (теплопроизводительность) кВт |
16 | 25 | 32 | 40 | 60 |
Габаритные размеры котла, мм: глубина |
1055 745 1255 |
1210 745 1255 |
1480 745 1255 |
1500 840 1360 |
2200 850 1370 |
Мощность котла (теплопроизводительность) кВт |
80 | 98 | 140 | 190 | 250 | 300 |
Габаритные размеры котла, мм: глубина |
2260 1150 1830 |
2400 1150 1830 |
2340 1460 2170 |
2550 1460 2170 |
2650 1700 2445 |
2820 1700 2445 |
Прим. Информация взята из техотдела одного из ведущих производителей дровяных пиролизных котлов.
Отапливаемая площадь для дровяного котла
Самое важное дело – это подобрать дровяной пиролизный котёл по размеру.
Советов и методик здесь может быть много. Самый простой и проверенный дедовский способ – это подбирать отопительный агрегат из расчёта 1кВт на 10 м2 отапливаемой площади. Выбирать нужно с запасом в 10%. Соответственно, на 120м2 нужен котёл 16кВт, на 160м2 нужен котёл 18кВт и так далее… Если производитель «не обдурил» с показателем мощности дровяного пиролизного котла – все будет работать.
Маленькая поправка на высоту помещения
– Если высота отапливаемого помещения больше 3м, то на каждый метр свыше нужно добавлять мощность выбираемого котла +1…3%.
Что делать после выбора дровяного котла
(шуточные советы от производителя)
После выбора и покупки дровяного котла возникает вопрос – а что с ним теперь, собственно делать?
Транспортировка дровяного пиролизного котла
Правильная транспортировка дровяного котла – это очень важно. Лучше всего, пиролизные котлы не перевозить, а кантовать к месту установки. При этом нужно не забывать, что, чем чаще котёл «гепнули» об матушку-землю, тем крепче стала футеровка и корпус котла. «Утряска», знаете-ли – дело нужное. Естественно, такой отопительный агрегат послужит дольше.
(Идеальный вариант перемещения котла в пространстве – это «волоком по бездорожью») Если при этом, слегка оцарапается облицовка, отвалится дверца или блок автоматики – не расстраивайтесь. Смело звоните в отдел технической поддержки производителя и требуйте замены некачественных деталей. При этом, не забудьте отрезать (оторвать) температурный датчик, типа – сам отвалился.
Установка и подключение дровяного пиролизного котла
При установке дровяного пиролизного котла смело игнорируйте любые сантехнические правила, СНИПы и, самое главное – здравый смысл! Помните, что дровяные котлы могут работать, даже «лёжа на боку»! Дровяным пиролизным котлам не нужна квалифицированная работа по их установке и обслуживанию. Это ведь ДРОВА. Позовите «шабашников», «присандальте» пиролизный котёл своей системе отопления и сразу звоните в службу техподдержки производителя.
Подбор персонала для обслуживания дровяного пиролизного котла
При подборе персонала, на роль оператора дровяного пиролизного котла выбирайте алкашей из подворотни. Они-то уж точно смогут колоть и запихивать дрова в топку котла. А, тискать кнопки автоматики – позовите кого-нибудь из своих знакомых, чтобы с высшим образованием был человек, значит.
Обслуживание дровяного пиролизного котла
Кто-то выдумал сервисное обслуживание дровяного пиролизного котла. Бред. Что там обслуживать? Напихал дров, поджёг и пусть горят. Ну, есть немного золы и пепла. Так они сами вываливаются из котла при открывании дверок.
Производитель напоминает о необходимости раз в сезон открыть теплообменник и очистить поверхность труб от сажи? Чепуха. Зачем пачкать руки, чтобы почистить то, что не видно?
Инструкция по эксплуатации, паспорт и гарантийный талон
К каждому пиролизному котлу прилагается «Инструкция по эксплуатации», «Паспорт» и «Гарантийный талон». Что это такое и для чего это делается?
Пояснение:
- Гарантийный талон
– Его можно повесить в рамочку, там красивые печати и подписи - Паспорт
– Ну, это на тот случай, если спецслужбы заинтересуются происхождением котла. Тогда нужно сунуть паспорт им в нос и послать куда подальше. - Инструкция по эксплуатации
– О, это важно! Только, читать её вовсе не обязательно.
На самом деле – это бумага для первого розжига котла.
Электронный блок управления (автоматика)
На нем всего шесть кнопок. Это гораздо меньше, чем на мобильном телефоне. Так что проблем не будет. Тискаем кнопки и смотрим, что получается. Кнопка «для самоуничтожения» производителем не предусмотрена, так что потребителю ничего не угрожает.
Первый розжиг дровяного пиролизного котла!
Песня! Очень важно, при первом розжиге, все свои проблемы списать на производителя! При этом нужно помнить, что звонить в службу технической поддержки нужно до полного самоудовлетворения! А куда им деваться. За то они деньги получают!
Кстати, отдел маркетинга и техническая служба завода, с большим удовольствием читают по телефону «Инструкцию по эксплуатации», которую прикладывают к каждому пиролизному котлу. Кроме того, за небольшое вознаграждение, та же «Инструкция по эксплуатации» читается в стихах и под аккомпанемент бубна.
Конденсат в корпусе дровяного пиролизного котла
Никому не верьте. Никакого конденсата в природе не существует! Это все выдумки производителя. Как только увидите лужу под своим пиролизным котлом – сразу начинайте звонить производителю. Причём, чем чаще – тем лучше. Пусть приезжают и забирают своё дырявое корыто. Потом, вдоволь наговорившись по телефону и приняв на веру утверждение про конденсат, можно будет немного расслабиться.
– Практикой доказано, что примерно, через сутки-трое, а в особо тяжёлых случаях – всего через неделю, все владельцы пиролизных котлов приноравливаются топить котёл так, что конденсатообразование сводится к нолю. Однако, при первом розжиге гарантировано море конденсата. В отдельных случаях его количество может достигать десятков литров.
Дрова для дровяного пиролизного котла
Дрова нужны сырые. Более того – мокрые или свежесрубленные.
Где-то вычитали, что пиролизные котлы позволяют сжигать дрова, влажностью до 70%? Правильно. Вот такие дрова и нужно пихать в топку. А если дрова ещё и мёрзлые да с кусками льда, так это вообще – класс. Именно такая древесина даст наибольшее количество тепла при сгорании. Что касается породы дерева, так выбираем тополь. Он дешевле дуба и даёт много прекрасной золы. К тому же, гораздо приятней смотреть на огромную кучу низкокалорийных тополиных чурбаков, нежели на пару высококачественных дубовых поленьев. Низкокалорийность нынче в моде. Все хотят похудеть. Теперь, и йогурты низкокалорийные, и сало. Стало быть, заготавливать на зиму низкокалорийные дрова – тоже модно. Типа – самый писк, по теме.
Лопата
Как известно, смеяться нужно после слова «лопата». В этом месте можно улыбнуться.
Ностальгия по газовой идиллии
Эх, хорошее было дело – газовое отопление.
Ах, какая это была песня – массовая газификация Советского Союза.
А слова-то в ней какие были – Уренгой-Помары-Ужгород.
Народ тогда принимал новшество «на ура!» и целыми улицами, городами и сёлами переходил с угольно-дровяного печного отопления на отопление газовое – цивилизованное. О! Газовые котлы и плиты очень быстро завоевали сердца потребителей и прочно вошли в бытовую и производственную жизнь. Теплоцентрали почти полностью перешли на газ. Все новые котельные проектировались и строились только под газ. Человечество вздохнуло с облегчением и на долгие годы газ стал одним из главных источников тепловой энергии.
Газовое отопление – непозволительная роскошь
В последнее время ситуация изменилась кардинально.
Природный газ подорожал. Причём, подорожал так сильно, что неожиданно наступающая зима портит настроение абсолютно всем, кто живёт не в шалаше. Газовые войны и газовые кризисы давно стали нормой и уже никого не удивляют. Внезапно перекрытые газопроводы и магистрали – любимые фишки нынешней власти. Неудержимый рост стоимости газового отопления отрицательно сказывается на «упитанности» кошелька, угрожая довести последнего до состояния ярко выраженной дистрофии. Расходы на газовое отопление увеличились настолько, что иногда – проще отключить его совсем и сидеть в валенках, нежели оплачивать баснословные счета
Газовое отопление, из предмета первой необходимости, постепенно превратилось в предмет роскоши
Ба, даже у новоявленных постсоветских буржуев бывают проблемы с газовым отоплением. Правда, по иной причине, нежели финансовой. Денег-то как раз, у буржуинов – навалом. Вот только газом можно пользоваться исключительно при наличии газопроводов. А их давно уже никто не строит. Нет массовой газификации – и все тут. Вот и сидят господа-с, при своих-то деньгах – и в нетопленных загородных домиках. Такие вот дела.
Выход напрашивается один – найти другой источник тепловой энергии и сказать «гуд бай» газу, как топливу
Дровяное отопление – как вариант
Об альтернативных энергоносителях сказано много, а написано – еще больше. Как вариант – дровяное отопление. Даже благополучная и сытая Европа не брезгует дровяным отоплением. Чего уж стесняться нам, сирым. Благо, научно-технический прогресс и господа производители обратили свои ясны очи на сию проблему и «наклепали» такое невероятное количество модификаций дровяных котлов, что глаза разбегаются. Да, ныне дровяные котлы не делает только ленивый. Вот это и сбивает с толку неискушённого потребителя. В этой статье автор рискнул обобщить свой опыт по работе с дровяными пиролизными котлами и дать несколько советов по их выбору-подбору. Часть советов изложена в шуточной форме, что отнюдь не умаляет их информационной ценности.
+
Альтернативное Отопление: отопление горение котёл дрова древесина теплота пиролиз
Котел на отопление своими руками
В данной публикации мы расскажем, как сделать котел на отопление своими руками, и какой из вариантов доступен для самостоятельного изготовления. Главной частью, сердцем любой системы отопления является котел. Многообразие их видов и конструкций способно поразить всякое воображение. И, надо отдать должное, многие современные котлы являются и экономичными, и эффективными устройствами. Они имеют тонкие регулировки, снабжены автоматикой и могут работать без участия человека. Некоторые модели даже могут отправить СМС хозяину и «доложить» о тепловой обстановке в доме, а хозяин по мобильному телефону или через интернет-соединение может заказать нужную температуру к своему приезду. Но бывают случаи, когда выгодно сделать котел на отопление своими руками. Например, для отопления дачного домика или теплицы.

Интернет буквально перегружен различной информацией по самостоятельному изготовлению котлов отопления. Применяются совершенно неожиданные комплектующие, которые никак не задумывались ранее быть частью котла; некоторые технические решения могут поспорить с изобретениями конструкторских бюро; КПД некоторых котлов не уступают лучшим котлам именитых производителей. Но к сожалению, в интернете и немало «мусорной» информации, которая не может ничем помочь, а в некоторых случаях способна и навредить. Авторы некоторых обзоров хвастливо заявляют, что нет ничего проще, чем самостоятельно изготовить котел отопления, хотя на самом деле это непростая задача. Цель этой статьи разобраться, какие именно котлы отопления достойны того, чтобы сделать их самостоятельно и каковы особенности технологического процесса их изготовления.
Виды котлов отопления и возможность их самостоятельного изготовления
Задача котла отопления – нагреть при помощи какого-либо топлива теплоноситель и передать его в систему отопления, которая уже распределяет тепло потребителям. Именно по виду применяемого топлива котлы делятся на несколько больших классов. Рассмотрим эти классы и сразу определим целесообразность самостоятельного их изготовления.
- Газовые котлы отопления – в настоящее время — это наиболее экономически выгодный вид топлива. Современные газовые котлы имеют высокий КПД, легко управляются, работают без вмешательства человека. Самостоятельное изготовление газовых котлов возможно, но категорически не рекомендуется. Во-первых, из-за того, что газ – это опасный вид топлива и любое несанкционированное вмешательство может привести к печальным последствиям, а, во-вторых, никакая газоснабжающая организация не даст разрешения на эксплуатацию самодельного газового котла. И правильно сделает.

- Жидкотопливные котлы применяются там, где нет газификации и других видов топлива. Эти котлы имеют очень высокий КПД, они легко поддаются автоматизации, но их применение связано с определенными трудностями по хранению больших количеств топлива: солярки или мазута. Самостоятельное изготовление жидкотопливных котлов запрещено, никакой пожарный инспектор не поставит свою подпись при сдаче дома в эксплуатацию, если он будет оборудован не сертифицированным оборудованием. Да и, наверное, мало кто захочет жить на пороховой бочке.

- Электрические котлы отопления имеют явное преимущество перед всеми остальными в простоте своей конструкции, малым габаритным размерам, удобству управления. Эти котлы сравнительно просто сделать самостоятельно. Но все эти преимущества нивелируются высокими ценами на электроэнергию. К сожалению, отопление электричеством экономически невыгодно. Оно и понятно, ведь значительную часть электроэнергии получают путем сжигания углеводородного топлива. Еще одним существенным ограничением является то, что не всегда электроснабжающие организации дадут разрешение на выделение большой мощности.

- Твердотопливные котлы отопления, несмотря на заверения скептиков об их скором уходе на второй план, продолжают успешно работать и поныне. Мало того – они испытывают настоящее второе рождение. В качестве топлива в них используются дрова, каменный уголь, торфяные брикеты, горючие сланцы и другие виды твердого топлива. Очень интересны котлы, которые используют особый род топлива – пеллеты, изготавливаемые из отходов древесины. Эти котлы поддаются автоматизации, имеют высокий КПД, но производство и логистика пеллет пока находится на зачаточном уровне. Для самостоятельного изготовления более всего подходят именно твердотопливные котлы, поэтому будем рассматривать именно их. Но особого внимания достойны одни из представителей твердотопливных котлов – пиролизные.

Твердотопливные пиролизные котлы отопления
Классический твердотопливный котел представляет собой емкость определенного объема, выполненная из металла: стали или чугуна. В ней происходит сгорание твердого топлива, при этом выделяется тепловая энергия, передаваемая теплоносителю при помощи теплообменников. При этом в камеру сгорания постоянно подается наружный воздух для поддержания горения топлива. Если прикрывать подачу воздуха, то процесс горения замедлится, а если открыть, то оно будет идти быстрее именно так регулируют мощность классических твердотопливных котлов.
Существуют котлы, приспособленные только для определенного вида топлива: дрова, уголь, пеллеты, — но есть модели, которые работают на любом топливе. Твердотопливные котлы могут быть как с естественной тягой, так и с принудительной. КПД хорошо спроектированного и выполненного классического твердотопливного котла может достигать 71—79%.

Преимуществами таких котлов являются:
- Доступность и низкая цена на топливо.
- Возможность использовать несколько видов топлива.
- Способность сжигать отходы деревообрабатывающего производства и сельскохозяйственной переработки.
- Полная автономность работы, независимость от электроэнергии.
Однако классические твердотопливные котлы обладают и рядом недостатков, с которыми невозможно не считаться:
- На одной загрузке топлива котлы работают не более 4—6 часов.
- Необходимость хранения больших запасов топлива требует дополнительных площадей.
- Загрузка в основном происходит в ручном режиме.
- Классические твердотопливные котлы требуют постоянной очистки от продуктов сгорания.
- Процесс сгорания обладает инерционностью, его трудно контролировать.
В категории твердотопливных котлов стоит выделить в отдельную группу так называемые пиролизные котлы, работа которых происходит за счет раздельного сгорания топлива и выходящих из него продуктов распада – пиролизных газов. Рассмотрим работу такого котла на примере.

Топливо (это чаще всего дрова) через верхнюю загрузочную дверку загружают в газифицирующую камеру. Дроссель дымохода полностью открывают и дрова поджигают. При этом включают вентилятор, который подает в камеру воздух. Естественно, дрова начинают гореть как в обычном твердотопливном котле.
После того как дрова разгорелись, закрывают верхнюю дверку и перекрывают дроссель дымохода. Воздух продолжает поступать к топливу, но в ограниченном количестве, поэтому дрова начинают тлеть при температуре от 200 до 800 °C. При этих условиях происходит реакция пиролиза: разложения древесины на твердую часть в виде угля и легкую — пиролизных газов, которые через форсунку подаются в камеру сжигания. Туда же подается через канал подачи вторичного воздуха подогретая смесь. В условиях высоких температур пиролизные газы воспламеняются и окисляются подаваемым воздухом. Температура их сгорания при этом составляет около 1100 °C.
Раскаленные газы проходят через множественные дымовые каналы, которые находятся в среде теплоносителя системы отопления – воде. Происходит передача тепловой энергии. Высокая температура в камере сжигания поддерживает процесс пиролиза в газифицирующей камере. Если необходимо доложить дрова в газифицирующую камеру, то для этого полностью открывают дроссель дымохода, выжидают несколько минут, чтобы камера проветрилась от пиролизных газов и начался обычный процесс горения. После этого открывают дверцу, докладывают дрова, закрывают дверцу и заслонку (дроссель) дымохода. Процесс пиролиза и дожигания газов в нижней камере возобновляется.
Внимание: в котлах с нагнетанием первичного и вторичного воздуха открывать дверцу загрузки можно только после открытия заслонки дымохода и паузы. В ином случае, при открытии дверцы пиролизные газы, скопившиеся в камере газификации, могут воспламениться. Этого недостатка лишены пиролизные котлы не с нагнетанием воздуха, а с дымососом, где в камерах создается разрежение.
Пиролизные котлы отопления обладают следующими преимуществами:
- В пиролизных котлах происходит полное сгорание топлива, что позволяет гораздо реже очищать зольник и высокотемпературные газоходы.

- Горением пиролизных газов можно легко управлять, что позволяет сделать управление котлом автоматизированных.
- Процесс горения в газифицируемой камере управляемый при помощи подачи первичного воздуха. Горение замедленное, а это позволяет на одной закладке дров работать от 5—7 часов до нескольких суток (у котлов верхнего горения).
- В пиролизных котлах можно сжигать крупные не колотые дрова.
- В качестве топлива могут быть использованы древесные отходы, обрезки фанеры, ДСП, ДВП, МДФ.
- Пиролизные котлы в 3 раза меньше выбрасывают в атмосферу вредных веществ.
Недостатки пиролизных котлов:
- Для работы вентилятора или дымососа необходима электроэнергия, поэтому следует озаботиться оснащением котла мощным источником бесперебойного питания.
- При влажности топлива более 20% резко падает КПД котла.
- В случае малых нагрузок возможны перепады в работе котла, что сказывается на отложении дегтя в газоходных каналах. Для постоянной нагрузки котла может потребоваться теплоаккумулятор – для запасания тепловой энергии.

- Чтобы в газоходах котла не выпадал конденсат, необходимо поддерживать температуру обратки не менее 60 °C. Конденсат приводит к ускоренной низкотемпературной коррозии котла.
- Невозможность организации автоматической подачи топлива.
- Пиролизные котлы очень материалоемкие, поэтому стоят в 1,5—2 раза выше, чем классические твердотопливные.
Масальский А.В.
Редактор категории «строительство» на портале Stroyday.ru. Специалист по инженерным системам и водоотведению.
Задать вопрос экспертуТак как в пиролизных котлах происходит высокотемпературное горение (1100—1200 °C), то нижнюю часть камеры газификации и всю камеру сжигания, включая и дверцу, нужно особым образом защитить при помощи футеровки – специальной жаропрочной облицовки. Учитывая высокие температуры, футеровка делается либо шамотным кирпичом, либо специальными жаростойкими муллитокорундовыми бетонами.
Какие функции выполняет футеровка:

- Защита металлических поверхностей камер котла от воздействия высоких температур, что предотвращает металл от прогорания.
- Для успешного течения реакции выделения газов и горения пиролизных газов необходим определенный температурный режим. При контакте пламени с охлаждаемым металлом может пойти обильное выделение конденсата, а футеровка позволяет удерживать температуру реакции постоянной.
Цены на модельный ряд отопительных котлов
Отопительные котлы
Котел на отопление своими руками
Прежде чем начинать изготовление пиролизного котла, необходимо точно определиться с его размерами, которые во многом зависят от необходимой мощности. Недостаточная мощность котла не позволит компенсировать все теплопотери, а избыточная потребует сброса излишков в теплоаккумулятор.
Обычно при расчетах принимают, что для отопления 10 м2 площади жилья требуется 1 киловатт мощности котла. Допустим, требуется отопить 250 м2 площади загородного дома. Получается, что котел должен иметь мощность не менее 25 КВт. В следующих рисунках приведены чертеж котла и таблица соответствия размеров — мощности котла.


Эти данные будут являться ориентиром для расчета будущей конструкции. Лучше всего воспользоваться готовыми чертежами уже сделанных и успешно работающих не один сезон котлов. На этих котлах уже отработаны типичные ошибки и их авторы охотно могут поделиться чертежами с подробнейшей спецификацией именно того котла, который будет отвечать всем потребностям. Естественно — это не бесплатно, но сумма в 50—70 $ просто смехотворна по сравнению с тем, что может ждать горе-самоделкина на пути к вожделенному котлу.
Масальский А.В.
Редактор категории «строительство» на портале Stroyday.ru. Специалист по инженерным системам и водоотведению.
Задать вопрос экспертуНастоятельно рекомендуется самому сделать 3D-визуализацию всех узлов котла в AutoCAD или любой другой подходящей программе, чтобы лучше понять внутреннее устройство и выработать правильную стратегию изготовления котла.

Необходимый инструмент и материалы для изготовления котла
Для изготовления пиролизного котла понадобится следующий инструмент:
- Сварочный инвертор.
- Электродрель с набором сверел по металлу разного диаметра.
- Углошлифовальная машина (болгарка) под круг диаметром 230 мм.
- Углошлифовальная машина под круг 125 мм.
- Для проделывания отверстий большого диаметра желателен газовый резак или (что идеально) плазморез. Если их нет, то при определенном навыке это можно сделать болгаркой.

- Стандартный набор слесарного инструмента: молоток, зубила, напильники, струбцины и другое.
Материалы для изготовления котла:
- Для изготовления газифицирующей камеры и камеры сжигания лучше использовать листовую сталь 5 мм, а для внешней обшивки 4 мм. Всего понадобится примерно 7—10 м2 листа, в зависимости от конкретной модели. В крайнем случае можно обойтись для всего котла листом 4 мм.
- Труба диаметром 57 мм толщиной стенки 3,5 мм для теплообменников – 8—10 м.
- Труба диаметром 159 мм с толщиной стенки 4,5 мм для борова (горизонтального выхода дымохода из котла) – 0,5 м.
- Шамотный огнеупорный кирпич ША-8 – 15-25 шт.

- Труба диаметром 32 мм с толщиной стенки 4,5 мм – 2 м.
- Профильная труба 60*30*2 мм – 2 м.
- Профильная труба 80*40*2 мм – 2 м.
- Полоса стальная 30*4 мм – 2 м.
- Электроды – 5—6 пачек.
- Круги отрезные 230 мм – 10 шт.
- Круги отрезные 125 мм – 10 шт.
- Круги шлифовальные 125 мм – 5 шт.
- Вентилятор центробежный дутьевой.

- Датчик температуры.
Приведенный перечень весьма приблизителен и не является точной инструкцией для исполнения. Все должно закупаться на основе индивидуальных расчетов. Наверняка что-то придется докупать, а что-то останется в излишках.
Изготовление пиролизного котла
Лучше всего составить оптимальный план раскроя стального листа на заготовки заранее, по уже имеющимся чертежам и нарубить его на прямоугольные заготовки сразу при закупке на металлобазе. Эта услуга, конечно, стоит денег, но дает преимущества во времени и качестве. Болгаркой такой ровный срез, как при рубке, сделать практически невозможно. Стандартные размеры стального горячекатанного листа толщиной 3—5 мм составляют 1,5*6 м.

Отметим основные этапы изготовления пиролизного котла:
- После раскроя заготовок можно начинать изготавливать внутреннюю часть котла, а именно сваривать камеры: газифицирующую и сжигания. Монтаж лучше делать из двух половинок.

- После того как будет сварен каркас камер, можно приварить заднюю стенку и воздуховоды в камере газификации. На фотографии они сделаны из швеллера, но это совершенно необязательно, достаточно профильной трубы 60*30*2 мм, в которой предварительно насверлить отверстий диаметром 10 мм. Обратите внимание на вырез в задней стенке под дымоходный канал.

- В камеру сжигания выводится трубка подачи вторичного воздуха, которая связана с фасадом котла при помощи профильной трубы 20*20 мм.

- Настало время готовить теплообменник. Для этого в заготовленной пластине по разметке выжигаются газовым резаком отверстия под газоходные трубы диаметром 57 см. При отсутствии резака можно прожечь большим током электродом, но этот способ хуже.

- Нарезаются трубы теплообменника, насаживаются на опорные пластины, прихватываются сваркой. После проверки размеров, все стыки обвариваются. Теплообменник готов.

- На свое штатное место приваривается теплообменник. На этом же этапе изготавливается и монтируется дроссельная заслонка дымохода.

- Приваривается передняя стенка камер котла, предварительно в ней делаются отверстия для трубок подачи первичного и вторичного воздуха.

- В месте дроссельной заслонки и выхода газохода приваривается задняя крышка и боров.

- Внутренняя часть котла собрана. Теперь необходимо тщательно зачистить сварные швы шлифовальным диском и проверить их качество.
- В качестве внешней обшивки котла применяется листовая сталь 4 мм. Для ее крепления на корпус котла навариваются отрезки уголка №25.

- На предварительно размеченном и раскроенном листе обшивки делают сквозные отверстия диаметром 10—12 мм в месте расположения уголков.

- Все отверстия обвариваются, чтобы лист обшивки надежно скрепился с основанием.

- Подобным образом обшиваются все стороны котла кроме верхней крышки. Все стыки тщательно провариваются и зачищаются.

- Настало время проверки герметичности всех сварных швов. Для этого все отверстия входа, выхода и слива теплоносителя заглушаются и котел наполняется водой через верхнюю крышку. Проверяется отсутствие течей. Если течь обнаружена, то это место помечается мелом для дальнейшего исправления.

- Для ревизии дымоходов делается туннель для верхней крышки, изолированный от водяной рубашки котла и только потом заваривается верхняя часть котла.

- Регулировку воздушных заслонок делают при помощи резьбовых шпилек.

- Все воздушные отверстия закрывают общим кожухом, из которого выводят общий воздуховод из профильной трубы.

- Изготавливают и навешивают дверцы для камер котла. В качестве футеровки дверцы можно применять либо чугунные пластины, либо шамотный кирпич. Уплотнение делают керамическим шнуром.

- Футеровку нижней части камеры газификации до воздуховодов делают из шамотного кирпича. Для этого кирпич пилят при помощи болгарки с камнерезным диском. Доводят кирпич до нужного размера вручную на шлифовальном камне.

- От геометрических размеров щели в нижней части камеры газификации зависит генерируемая мощность пиролизного котла. Поэтому при изготовлении камней футеровки надо принимать во внимание приведенные в таблице размеры, чтобы мощность котла соответствовала проектной.

- На профильную трубу главного воздуховода приваривается фланец, а затем крепится центробежный вентилятор.

- Шамотным кирпичом делают футеровку камеры сжигания.

- Для улучшения теплопередачи котла рекомендуется помещать в каналы газохода теплообменника так называемые завихрители (турбулизаторы), которые, во-первых, замедляют движение раскаленных газов и тем самым улучшают теплопередачу, а, во-вторых, служат для очистки труб газохода от отложений.

- Для прочистки завихрители прикрепляют к коромыслу, которое связано с рычагом, выведенным наружу. Покачивая рычаг можно быстро прочистить каналы.

- Перед запуском котла следует проверить его герметичность и опрессовать его давлением в 4 бар. Для этого заглушаются все отверстия в котле, кроме подачи и обратки системы отопления. Котел наполняется водой полностью и к нему подключается опрессовщик.

- Опрессовщиком давление доводится до 3 бар. Если давление сразу падает, значит, где-то есть течь, которую надо обнаружить и устранить. Если же давление в течение получаса не меняется, то можно считать, что котел герметичный и его можно интегрировать в систему отопления.
- Для обеспечения безаварийной работы котла, на трубе подачи в систему отопления через резьбовой штуцер монтируется группа безопасности котла, которая включает аварийный клапан, автоматический воздухоотводчик и манометр. При возникновении нештатных ситуаций, клапан, настроенный на давление 3 бар, сбросит избыточное давление.

- Пиролизный котел желательно оснастить блоком автоматики, который при помощи термодатчиков будет отслеживать режим работы котла и в случае необходимости производить его остановку и запуск. О том, как реализовано автоматическое управление в котлах, показано в видео.
Видео: Автоматика для пиролизного котла
Ввод пиролизного котла в эксплуатацию
Перед тем как производить первый запуск котла, необходимо его соединить с дымоходом и наполнить водой. Пустой котел запускать категорически запрещено – это приведет к перегреву. Помимо этого на каждом котле должен быть термометр, контролирующий температуру теплоносителя, который вкручивается в специально отведенное для этого место. Во всех проектах котлов обязательно предусмотрены отверстия для термометра, а также термодатчиков.
- Вентилятор через выключатель соединяется с питающей сетью, проверяется его работа. Все воздушные заслонки ставятся в среднее положение.
- На дно камеры газификации кладется бумага, чтобы она выглядывала из-под форсунки в камеру сжигания, а на нее уже укладываются дрова. Первая загрузка дров не должна быть большой, достаточно нескольких небольших поленьев. Дверь камеры газификации плотно закрывается.
- Полностью открывается дроссельная заслонка дымохода камеры газификации, включается вентилятор и поджигается бумага.
- Когда горение дров станет уверенным, через несколько минут, закрывается дроссельная заслонка дымохода. Дрова должны перейти в режим медленного горения (тления), которое сопровождается выделением пиролизных газов. Через нижнюю дверцу камеры сжигания производится контроль зажигания факела горения пиролизных газов. Если он не загорелся, надо попробовать уменьшить подачу воздуха в камеру газификации и увеличить в камеру сжигания.
- После загорания пламени, заслонками регулируется его интенсивность и цвет. Бело-желтый цвет пламени говорит о правильной настройке котла.
- Дверца отсека сжигания закрывается и засекается время, в течение которого котел доведет воду до кипения. По термометру контролируют повышение температуры. Как только, вода достигнет 100 °C – вентилятор отключают. Факел в камере сжигания должен погаснуть. Температура воды после этого должна снижаться.
- При открытии дроссельной заслонки дымохода пламя в камере сжигания тоже должно погаснуть.
Заключение
- Пиролизные котлы длительного горения являются сложными устройствами, поэтому их самостоятельное изготовление должно производиться только по чертежам тех котлов, которые уже показали себя в эксплуатации.
- Самостоятельное изготовление требует неукоснительного соблюдения технологии с проверкой каждого этапа.
- Пиролизные котлы очень материалоемкие, даже на их самостоятельное изготовление уходит очень много дорогостоящего металла. Окупятся они только тогда, когда будут находиться в постоянном пользовании в течение нескольких сезонов.
Видео: Изготовление пиролизного котла для отопления дома
ТОП-5 лучших пиролизных котлов
СИВ-100
Этот пиролизный котел может обогреть помещения до 900 м2. Для данной модели котла можно использовать любой вид топлива, но важно понимать, что от качества используемого топлива будет зависеть и эффект работы котла. КПД СИВ-100 — 92%, мощность — 100 кВт.

Плюсы
- подходит любое топливо;
- управление автоматика;
- высокий уровень КПД;
- большая топка;
- длительный срок службы.
Минусы
- изъянов пока не обнаружено.
Буржуй-К МОДЕРН-12
Энергонезависимый котел Буржуй-К МОДЕРН-12 способен обогреть помещение до 200 кв.м. Для обогрева можно использовать различный вид топлива: дрова, брикеты из опилок, уголь и др. Одной загрузки может хватить до 8 часов, все зависит от используемого вида топлива. Коэффициент полезного действия котла 92%, мощность 12 кВт.

Плюсы
- малогабаритный;
- энергонезависимый;
- коэффициент полезного действия 92%.
Минусы
- не экономичный.
Твердотопливный котел Буржуй-К МОДЕРН-12
Гейзер ПК-20
Пиролизный котел Гейзер ПК-20 отлично подойдет для обогрева больших помещений от 120 до 250 кв.м. Простой в обслуживании, достаточно одной закладки дров на 12 часов, КПД до 87%. Котел имеет автоматическую систему.

Плюсы
- экономичный;
- автономный;
- простой в обслуживании.
Минусы
- слишком габаритный (для установки нужно подготовить фундамент).
Viessmann Vitoligno 100 VL1A025 30 кВт
Модель котла, работающая только на дровах. Топка вмешает поленья до 50 см. Может хорошо обогреть помещение размерами до 300 кв.м., выделяет КПД до 88%. Наличие электронного дисплея упрощает регулировку окружающей среды.

Плюсы
- длительное горение;
- коэффициент полезного действия 88%;
- экономичен;
- имеет теплоизоляцию.
Минусы
- нужна мягкая древесина.
Буржуй К ТА 20
Очень экономичная модель пиролизного котла. Имеет очень большой эксплуатационный срок и отличную производительность. Отличное решение для людей, которые целесообразно используют денежные средства.

Плюсы
- длительный срок службы;
- экономичен;
- высокоэффективен;
- наличие качественного терморегулятора
Голосование: какой пиролизный котел самый лучший?
Что бы вы выбрали из пиролизных котлов или посоветовали бы приобрести?
Буржуй-К МОДЕРН-12
Viessmann Vitoligno 100 VL1A025 30 кВт
Сохраните результаты голосования, чтобы не забыть!
Чтобы увидеть результаты, вам необходимо проголосовать
Твердотопливные котлы для отопления частного дома, дачи: каталог, цены в Москве
Наиболее совершенной конструкцией на сегодня являются котлы новой серии «Суворов Ультра». По своим характеристикам они значительно превзошли котлы более ранних серий, по некоторым характеристикам не имеют аналогов и поэтому найдут своих потребителей, отдающих предпочтение котлам с предельно высокими техническими и эксплуатационными характеристиками.
В конструкции котлов «Суворов Ультра», как и в котлах «Суворов Эко» и «Суворов — М», используются системы высокоточного управления объёмом поступающего в котёл воздуха и управления температурой дымовых газов.
В тоже время в конструкцию котлов серии «Суворов Ультра» внесен целый ряд новых технических решений, позволяющих значительно улучшить их технические и эксплуатационные характеристики, а также реализовать не имеющие аналогов функции. К числу этих решений относятся:
- реализация принципа нижнего горения, при котором происходит горение не всего объёма топлива, находящегося в бункере, а сравнительно небольшого объёма топлива в нижней части бункера. Что позволяет более оптимально и, следовательно, экономично сжигать топливо в течение длительного интервала времени;
- организация распределённой подачи подогретого воздуха, что обеспечивает более равномерное горение топлива в необходимом объёме основания бункера и формирование достаточно объёмного топочного ядра;
- увеличение длины газового тракта. Он сделан трёх оборотным с изменяемой длиной и специальным образом сконфигурирован. Это обеспечивает регулировку в широком диапазоне теплосъёма от газового потока к теплоносителю;
- теплоизоляция части газового тракта в зоне высоких температур и дожигание в ней (с помощью нагретого вторичного воздуха) пиролизных газов, а также летучих компонентов топлива в жидкой и твёрдой фазе. За счёт этого температура в восходящем канале может увеличиваться до 1200 0С. Высокоэффективное сжигание компонентов топлива в жидкой и твёрдой фазах на мощностях выше средней существенно уменьшает рост отложений на теплообменных поверхностях, что увеличивает период между чистками котла. Кроме того, возможно самоочищение теплообменных поверхностей от смолистых отложений после работы котла на близких к минимальным мощностям путём перевода котла в режим номинальной или максимальной мощности. В другой части газового тракта размещён турбулизатор, обеспечивающий дополнительное повышение теплосъёма от газового потока дымовых газов;
- футеровка шамотными плитами части основание бункера и газового тракта, что обеспечивает увеличение объёма горячего ядра горящего топлива, уменьшение объёма относительно холодных периферийных зон, повышение температуры в топке (до 900 – 1000 0С) и более полное сгорание компонентов, содержащихся в топливе;
- изменение соотношения первичного и вторичного воздуха при работе котла на различных мощностях, что обеспечивает снижение тепловых потерь и дополнительное повышение его экономичности;
- установка заслонки дымоудаления большой площади с системой блокировки загрузочной дверцы, которая обеспечивает при дозагрузке топлива более удобную и безопасную эксплуатацию котла;
- расширение типов используемого топлива. Кроме дров, опилочных и торфяных брикетов могут быть использованы опилки, уголь и пеллеты.
Совокупность новых технический решений позволила реализовать в твёрдотопливном котле принципиально новую функциональную возможность – работу котла в режимах ожидания и сверх малых мощностей с автоматическим переходом в этот режим и выходом из него. В ждущий режим котёл переходит автоматически в случае аварийной ситуации (прекращение работы циркуляционных насосов), либо переведён вручную путём их отключения и может находится в нём в течение длительного времени, генерируя небольшую мощность (сотни ватт) равную тепловым потерям котла через его корпус и за счёт небольшой циркуляции теплоносителя в системе отопления (в основном через гидрострелку). При возобновлении работы циркуляционных насосов или отборе тепловой энергии контуром горячего водоснабжения котёл автоматически переходит в режим генерации потребляемой мощности. В котле может быть реализован режим генерации сверхмалой мощности и электронной перестройки тепловой мощности в широком диапазоне, который может быть использован в летний период для получения горячей воды или для поддержания требуемой температуры в доме в периоды похолодания или осеннее весенний периоды. Указанные функциональные возможности повышают надёжность системы отопления и безопасность эксплуатации котла, а также расширяет его эксплуатационные характеристики.
В целом наращивание объёма загружаемого в котёл объёма топлива и высокоэффективное его сжигание позволяют обеспечить большую продолжительность горения от одной закладке топлива, как на максимальной, так и на минимальной мощности. В частности, на опилочных брикетах время работы котла составляет до 28 ч. на номинальной мощности и до 126 ч. – на минимальной, при использовании дров, соответственно до 10 и 69 часов, что значительно больше чем у аналогов. При этом на дровах получен коэффициент использования топлива 95,7% (процент извлекаемой тепловой энергии, содержащейся в топливе). В режиме сверх малой мощности продолжительность работы котла может увеличиться в несколько раз. Большая длительность работы котла в автоматическом режиме, в том числе в режиме ожидания существенно упрощает обслуживание котла при его эксплуатации.
Таким образом, разработанные серии котлов торговой марки «Суворов» обладают высокими техническими и эксплуатационными характеристиками, не уступающими известным аналогам, а по некоторым параметрам превосходит их.
Тепло и энергия от пиролизного масла

Замена ископаемого топлива пиролизным маслом может быть произведена уже сегодня путем среднего или крупномасштабного (совместного) сжигания природного газа, угля или топочного мазута в котлах, печах и турбинах. Модернизация этих систем требует ограниченных инвестиций, а благодаря снижению выбросов парниковых газов на уровне около 90% пиролизное масло предлагает уникальную возможность сделать ваше энергоснабжение более устойчивым, а также снизить вашу зависимость от цен на ископаемое топливо.Еще более интересным является его использование в децентрализованных решениях ТЭЦ, например, в системах централизованного теплоснабжения или в крупных промышленных компаниях, которые производят собственное электричество, тепло и / или пар.
При прямом сжигании в котле или печи пиролизное масло можно использовать для получения тепла. Это наиболее простое и понятное приложение. В этом случае пиролизное масло может заменить природный газ, а также тяжелое и легкое жидкое топливо, снижая выбросы углерода примерно на 90%.
Различные производители теперь могут гарантировать производительность при использовании пиролизного масла в своих горелках, например, Dreizler в Германии и Stork Thermeq в Нидерландах.Горелку котла необходимо заменить на многотопливную горелку, чтобы пиролизный мазут можно было смешивать с природным газом / мазутом, а трубы и резервуар для хранения должны быть изготовлены из нержавеющей стали (сам котел не требует замены. ). Многотопливная горелка обеспечивает полную гибкость, поэтому она может работать на 100% ископаемом топливе, если нет пиролизного масла.
Благодаря замене природного газа возобновляемым пиролизным маслом на заводе Empyro на заводе по производству сухого молока FrieslandCampina в Боркуло прямые выбросы углерода снизились на 15 процентов.Ежегодно экономится 10 миллионов кубометров природного газа, что эквивалентно потреблению 8000 голландских домашних хозяйств.
Это приложение предлагает компаниям возможность перейти (полностью или частично) с природного газа, сжиженного нефтяного газа или топочного мазута на возобновляемые альтернативные виды топлива. Пиролизное масло конкурентоспособно по цене на топочный мазут. Пиролизное масло неконкурентоспособно с текущими низкими ценами на природный газ в большинстве стран Европы и США. В таких странах, как Швеция (налог на углерод), Финляндия и Бразилия с низкими ценами на биомассу и более высокими ценами на пиролизное масло из ископаемого топлива могут конкурировать по цене.Кроме того, все большее число стран используют стимулы (или предписания в отношении передовых видов биотоплива) для пиролизного масла для замены ископаемого топлива (SDE + в Нидерландах, Renewable Heat Incentive в Великобритании и т. Д.), Чтобы сократить разрыв в ценах, а в Европе переход на пиролизное масло также принесет значительную часть углеродных кредитов ETS.
Если ваша компания использует природный газ, сжиженный нефтяной газ или топочный мазут в своих котлах для производства пара или горячей воды для промышленных процессов или (централизованного) отопления, и вы ищете экологически чистую альтернативу, пожалуйста, свяжитесь с нами для получения дополнительной информации.

Газовые турбины могут использоваться для производства электроэнергии и тепла (ТЭЦ), например, в удаленных местах. OPRA turbines в Хенгело поставляет газотурбинные генераторные установки для клиентов по всему миру в нефтегазовом, промышленном, коммерческом и морском секторах. Недавно газовая турбина OP16 мощностью 2 МВт была адаптирована для работы на пиролизном мазуте.
OP16 имеет промышленную радиальную конструкцию, обеспечивающую прочность, надежность, высочайшую эффективность в своем классе и сверхнизкие выбросы.После обширной серии испытаний и некоторых модификаций камеры сгорания OPRA теперь может поставить эти турбины с гарантией, что они будут бесперебойно работать на пиролизном масле BTG-BTL. Это открывает сегодня возможность производить 100% экологически чистое тепло и электроэнергию в любом месте.

Во многих регионах мира дизельное топливо и природный газ до сих пор используются в дизельных двигателях для выработки электроэнергии и тепла. Если в этих районах имеется биомасса, пиролизное масло можно производить на месте и использовать на месте для производства электроэнергии и тепла.Еще одно интересное приложение — движение корабля. В этой области применение пиролизного масла является одной из немногих альтернатив ископаемому топливу, которые являются коммерчески привлекательными. Пиролизное масло успешно прошло испытания на стационарных дизельных двигателях. Требуются некоторые изменения в двигателях, в основном для предотвращения повреждения двигателя и топливной системы из-за содержания воды и кислотности пиролизного масла. Электрический КПД дизельных двигателей очень высок (> 40%) по сравнению со всеми другими децентрализованными альтернативами, включая газовые турбины и прямое сжигание биомассы для производства электроэнергии.Более подробную информацию можно найти в нашем разделе загрузок.
Мы ожидаем появления на рынке дизельных двигателей, которые могут работать на пиролизном мазуте в ближайшие годы. Это открывает новый большой рынок для продажи пиролизного масла, поскольку эти двигатели могут использоваться как на судах, так и для тепло- и энергетических применений. Пиролизное масло можно производить по цене, конкурентоспособной с ценой на дизельное топливо. В ситуациях, когда в настоящее время используется дизельное топливо или мазут, пиролизное масло будет наиболее привлекательной экологически безопасной альтернативой.
Для дальнейшего развития как дизельных, так и газовых турбин головная компания BTG-BTL, BTG, участвует в европейском проекте «Bioliquids CHP Power Generation из биомассы». В наши услуги входит консультирование по применению пиролизного масла, включая помощь в получении разрешений и субсидий. Пожалуйста, не стесняйтесь обращаться к нам и обсуждать возможности технологии пиролиза, которые может предложить ваша организация.
.Пиролиз: путь к технологиям очистки угля
1. Введение
Что такое пиролиз: пиролиз — это термохимическое разложение углеродистых материалов, таких как биомасса, пластик, шины, уголь и т. Д., При повышенных температурах 200 ° C и выше в отсутствие кислорода. Это необратимая химическая реакция, в которой происходит одновременное изменение химического состава и физической фазы вещества. Эта реакция включает молекулярный распад более крупных молекул (полимера) на более мелкие молекулы в присутствии тепла.Пиролиз также называют термическим крекингом, термолизом, деполимеризацией и т. Д.
Что такое пиролиз угля: пиролиз угля включает подвергание угля воздействию высокой температуры 400–450 ° C в отсутствие кислорода. Когда присутствует кислород или пар, уголь начинает гореть, и этот процесс больше не известен как пиролиз, а скорее называется сжиганием и газификацией. Преимущества пиролиза угля огромны и перечислены ниже:
Преобразует отходы (уголь) в энергию.
Продукт может использоваться в качестве топлива в существующих промышленных котлах и печах.
Конечные продукты также могут использоваться для выработки электроэнергии.
Предлагает возобновляемые источники энергии.
Управление твердыми отходами.
Уголь и угольные продукты будут по-прежнему играть все более важную роль в удовлетворении энергетических потребностей и экономики стран. Это связано с большими запасами угля и его низкой стоимостью [1, 2].На уголь приходится примерно 25% мирового энергоснабжения и 40% выбросов углерода, но даже с учетом высокого процента выбросов очень маловероятно, что какая-либо из этих стран, которые занимаются разведкой и добычей угля, очень скоро откажется от угля. [3]. Экономический рост требует роста энергии [4]. В связи с недавней заботой об окружающей среде и возобновлением интереса к исследованиям альтернативной энергии из возобновляемых источников, таких как топливные элементы и ветер, водород из угля через комбинированный цикл интегрированной газификации был рассмотрен для предлагаемой водородной экономии [5, 6].Газификация считается экологически чистой технологией преобразования угля в двадцать первом веке, чем другие процессы использования угля, такие как сжижение и сжигание, потому что она является энергоэффективной [7], экологически чистой [8] и экономичной [9]. Он также имеет то достоинство, что выходит за рамки использования угля для производства электроэнергии [10], обработки металлов и производства химикатов [11], поскольку уголь может быть преобразован в полезные газы и жидкости [12]. Уголь — сложный углеродистый материал, состоящий из органических и неорганических веществ [13].В процессе газификации органическое и неорганическое вещество претерпевает различные химические и физические превращения [14]. Чтобы максимизировать эффективность газификации, необходимо понять механизм химического и физического превращения, так как это поможет снизить выбросы углерода в процессе, особенно при газификации низкосортного угля [15–17]. Несколько вариантов используются для управления скоростью подачи угля во время газификации: неподвижный слой, псевдоожиженный слой и газификаторы с увлеченным потоком [18].Газификаторы с псевдоожиженным слоем имеют потенциальное преимущество, заключающееся в том, что низкосортные угли, богатые золой и инертинитами, такие как южноафриканские угли, могут обрабатываться более эффективно, чем в обычных котлах, работающих на пылевидном угле [19–21].
Следовательно, разработка процессов утилизации угля потребует более глубокого понимания внутренних свойств угля и способов его химического преобразования в условиях процесса [22, 23]. Один из способов понять это — пиролиз, который проходит через все процессы утилизации угля [19].Следовательно, в этом сообщении оценка шести углей южного полушария будет использоваться для иллюстрации промежуточной роли, которую пиролиз играет в процессах утилизации угля.
2. Влияние изменений химических и физических свойств на характеристики угля
В настоящее время исследования по использованию угля и угольных продуктов направлены на чистую угольную технологию (CCT) [20, 24]. Предыдущие исследования CCT за последние 30 лет касались химической очистки угля, а недавние исследования — улавливания и хранения углерода (CCS) [20, 25].Исследовательские усилия были ограничены лабораторным масштабом при определении молекулярных и структурных параметров, таких как ароматичность, степень конденсации, которая определяет технические характеристики угля в процессе его утилизации [20, 26–28]. Суть химической очистки угля заключается в удалении или уменьшении содержания минералов в угле, поскольку сообщалось, что минеральное содержание в угле расплавляется, когда он подвергается термообработке во время процессов конверсии угля [20, 29], что приводит к блокированию активные центры углерода [30], тем самым снижая реакционную способность угля и уменьшая выбросы загрязняющих веществ [20, 31].
Уголь — сложный углеродистый полимер, состоящий из органических и неорганических веществ [32, 33]. Органические материалы известны как мацералы, а неорганические примеси считаются минералами [34]. При термической обработке; физические, химические, термические, механические и электрические свойства угля претерпевают трансформации [20, 35]. Одним из ключевых параметров, которые используются для измерения химической стабильности этого превращения, является ароматичность [20, 36]; это дает хорошее представление о превращении мацерала в полукокс, что является хорошим индикатором зрелости угля из-за перестройки углерода [20, 37].
Изменение углеродистой структуры из-за модификации органических и неорганических компонентов в угле и его последующем обугливании считается одним из основных факторов, влияющих на реакционную способность угля / полукокса в процессах конверсии угля [20, 38, 39 ]. Химическое преобразование включает изменение органической химической структуры (таблицы 1–3), в то время как физическое преобразование включает изменение морфологии и пористости угля (таблица 4, рисунки 1–12).
Уголь | SPL | SM | BCH | SSL | NGR | GER |
---|---|---|---|---|---|---|
мас.% Собственной влаги (осушенная на воздухе) | 1.5 | 1,0 | 2,1 | 4,2 | 9,6 | 15,4 |
мас.% Золы (воздушная сушка) | 11,2 | 17,3 | 16,2 | 29,1 | 9,0 | 12,4 |
мас.% летучих веществ (высушенные на воздухе) | 5,3 | 7,6 | 26,7 | 21,4 | 37,6 | 45,7 |
мас.% связанного углерода (высушенные на воздухе) | 82 | 74,1 | 55.0 | 45,3 | 43,8 | 26,4 |
вес.% Углерода (daf) | 90,2 | 90,4 | 81,6 | 77,5 | 75,6 | 70,5 |
вес.% Водорода (daf) | 2,7 | 3,5 | 4,6 | 4,5 | 5,2 | 6,6 |
мас.% Азота (daf) | 2,2 | 2,0 | 2,0 | 2,2 | 1,7 | 0.6 |
мас.% Кислорода (daf) | 2,7 | 3,3 | 10,7 | 15,4 | 16,9 | 18,5 |
мас.% Серы (daf) | 2,3 | 0,9 | 1,2 | 0,4 | 0,7 | 3,7 |
Общая теплотворная способность (МДж / кг) | 29,6 | 28,7 | 26,8 | 20,0 | 24,6 | 21,2 |
H / C | 0.4 | 0,5 | 0,7 | 0,7 | 0,8 | 1,1 |
f a | 0,91 | 0,85 | 0,73 | 0,72 | 0,65 | 0,49 |
Приблизительный анализ, окончательный анализ, теплотворная способность и расчетные значения H / C и ароматичности для необработанного угля.
Уголь | SPL | SM | BCH | SSL | NGR | GER |
---|---|---|---|---|---|---|
мас.% Присущей влажности (осушенная на воздухе) | 2.5 | 2,3 | 2,7 | 1,3 | 1,9 | 1,7 |
мас.% Золы (воздушная сушка) | 1,5 | 1,8 | 1,2 | 3,3 | 2,0 | 0,8 |
вес.% летучих веществ (воздушная сушка) | 6,8 | 9,6 | 27,2 | 25,0 | 43,2 | 60,3 |
вес.% связанного углерода (воздушная сушка) | 89,2 | 86,3 | 68.9 | 70,4 | 53,0 | 37,3 |
вес.% Углерода (daf) | 85,6 | 89,0 | 83,4 | 80,9 | 75,1 | 69,2 |
вес.% Водорода (daf) | 2,4 | 3,3 | 4,6 | 4,2 | 5,2 | 6,2 |
мас.% Азота (daf) | 2,0 | 1,8 | 2,0 | 2,3 | 1,8 | 0.6 |
мас.% Кислорода (daf) | 7,7 | 5,0 | 9,1 | 12,3 | 17,4 | 20,3 |
мас.% Серы (daf) | 2,1 | 0,7 | 1,0 | 0,3 | 0,1 | 2,7 |
Общая теплотворная способность (МДж / кг) | 32,7 | 33,3 | 32,0 | 30,0 | 29,3 | 28,9 |
H / C | 0.3 | 0,4 | 0,7 | 0,6 | 0,8 | 1,1 |
f a (CA) | 0,92 | 0,86 | 0,74 | 0,76 | 0,65 | 0,52 |
f a (FTIR) | 0,98 | 0,84 | 0,72 | 0,74 | 0,58 | 0,40 |
f a (C-ЯМР) | 0,98 | 0,94 | 0.76 | 0,80 | 0,58 | 0,43 |
f a (XRD) | 0,89 | 0,87 | 0,78 | 0,74 | 0,70 | 0,66 |
Таблица 2.xim анализ, окончательный анализ, теплотворная способность и расчетные значения H / C и ароматичности для обработанного кислотой угля. Таблица. Расчетные значения H / C и ароматичности для термообработанного угля.
Уголь 450 500 550 600 650 700 GER 9057 Х / К 0.5 0,4 0,3 0,3 0,2 0,1 f a (CA) 0,86 0,89 0,95 0,95 0,99 1,00 f a (FTIR) 0,66 0,69 0,73 0,74 0,76 0,79 f a (XRD) 0,66 0,67 0.68 0,72 0,74 0,76 NGR H / C 0,5 0,4 0,3 0,3 0,2 0,1 f a (CA) 0,86 0,90 0,93 0,96 1,00 1,03 f a (FTIR) 0,75 0,78 0.81 0,84 0,87 0,90 f a (XRD) 0,67 0,69 0,70 0,74 0,78 0,80 SSL H / C 0,4 0,4 0,3 0,3 0,2 0,1 f a (CA) 0,87 0,91 0,93 0.96 1,00 1,05 f a (FTIR) 0,84 0,88 0,90 0,93 0,97 1,00 f a (XRD) 0,91 0,94 0,96 0,97 0,97 0,97 BCH H / C 0,5 0,4 0,3 0.3 0,2 0,1 f a (CA) 0,86 0,89 0,92 0,95 0,98 1,03 f a (FTIR) 0,83 0,86 0,89 0,92 0,95 1,00 f a (XRD) 0,93 0,94 0,97 0,98 0,99 0.99 SM H / C 0,4 0,4 0,3 0,3 0,2 0,1 f a (CA) 0,88 0,89 0,92 0,95 0,99 1,03 f a (FTIR) 0,94 0,95 0,98 1,00 1,00 1,00 f a ( XRD) 0.96 0,98 0,99 0,99 0,99 0,99 SPL H / C 0,3 0,3 0,3 0,3 0,2 0,1 f a 0,94 0,95 0,95 0,97 0,98 1,03 f a (FTIR) 0,97 0.98 1,00 1,00 1,00 1,00 f a (XRD) 0,96 0,97 0,98 0,99 0,99 0,99
0,076 0,071 0,048 0,048 Уголь 450 500 550 600 650 700 GER O / C 0.132 0,103 0,092 0,073 0,064 0,056 Площадь поверхности BET (м 2 / г) 169,96 193,97 230,41 241,82 262,61 NGR O / C 0,130 0,110 0,083 0,075 0,067 0,061 Площадь поверхности BET (м 2 / г) 155 .78 182,61 183,19 234,10 238,14 239,74 SSL O / C 0,081 0,076 0,063 0,052 0,063 0,052 BET площадь поверхности (м 2 / г) 136.60 153,47 199,72 200,38 214,46 224,19 BCH O / .064 0,057 0,044 0,039 0,037 0,029 Площадь поверхности BET (м 2 / г) 130,17 158,68 183,89 206,40 215,4071 206,40 215.4071 900 SM O / C 0,039 0,042 0,033 0,033 0,037 0,032 Площадь поверхности BET (м 2 / g) 137 .94 148,17 170,35 186,54 194,60 196,99 SPL O / C 0,039 0,048 0,063 0,039 0,063 0,039 Площадь поверхности BET (м 2 / г) 113,93 135,18 136,74 150,98 162,47 164,40
Таблица 4.
Расчетные атомные значения площади поверхности O / C и BET по SEM и ASAP 2020 для термообработанного угля.
Рис. 1. Микрофотографии
, полученные с помощью SEM, перехода угля BCH в полукокс.
Рис. 2. Микрофотографии
, полученные с помощью СЭМ, перехода угля SM в полукокс.
Рис. 3. Микрофотографии
СЭМ перехода SPL угля в полукокс.
Рис. 4. Микрофотографии
SEM перехода угля SSL в полукокс.
Рис. 5. Микрофотографии
, полученные с помощью SEM, перехода угля NGR в обугливание.
Рис. 6. Микрофотографии
, полученные с помощью СЭМ, перехода угля из ГЭР в обугленный.
Рис. 7.
Петрографические снимки перехода угля в обугливание для свит ГЭР.
Рис. 8.
Петрографические снимки перехода угля в обугленный для свит ЯГР.
Рис. 9.
Петрографические снимки перехода угля в обугливание для комплексов SSL.
Рис. 10.
Петрографические снимки перехода угля в полуголь для свиты БЧХ.
Рис. 11.
Петрографические снимки перехода угля в обугливание для свиты СМ.
Рис. 12.
Петрографические снимки перехода угля в полуголь для свиты SPL.
. Каталитический пиролиз биомассы | IntechOpen
В зависимости от типа используемой биомассы низкая теплотворная способность, высокое содержание воды, высокая вязкость (из-за больших молекул), высокое содержание кислорода (из-за содержания кислородсодержащих углеводородов), а также нестабильность, несовместимость с другими ископаемыми видами топлива делают биологические -масло трудно использовать непосредственно в качестве топлива без модернизации [24, 55]. Чтобы улучшить биомасло для использования в топливных приложениях, были использованы два разных метода: гидродеоксигенация и каталитический крекинг.При гидродеоксигенации биомасляные соединения реагируют с водородом под высоким давлением и умеренной температурой с образованием углеводородных соединений и воды. Каталитический крекинг используется для улучшения биомасла через каталитическую среду, удаляя кислород из биомасляных соединений в форме H 2 O и CO 2 , включая химические реакции разрыва связей C – C посредством дегидратации, декарбоксилирование и декарбонилирование [1, 16, 24, 55]. Каталитический крекинг имеет несколько преимуществ перед гидродеоксигенацией, включая работу при атмосферном давлении и в окружающей среде, не требующей дополнительной подачи водорода [1].
3.1. Конфигурации системы для катализаторов, используемых в пиролизе биомассы
Используются два метода каталитического пиролиза: каталитический слой и смешивание катализатора. В методе с каталитическим слоем, который также называется « in-situ » или методом облагораживания вне слоя, пары пиролиза, поступающие из первого реактора, проходят через каталитический реактор, который называется каталитическим слоем, в результате чего получают биомасло, уголь, и газообразные продукты. Однако в методе смешения катализатора (в слое) образцы биомассы и катализатора физически смешиваются перед тем, как поместить в реактор пиролиза [1, 30, 37].
3.1.1. Метод слоя катализатора ( in situ, )
Метод слоя катализатора, также называемый пиролизом in-situ, , включает каталитическую модернизацию после термической конверсии паров пиролиза биомассы [1]. В общем, каталитический пиролиз in situ биомассы можно проводить с использованием различных конфигураций реакторов: одностадийных и двухступенчатых конфигураций реакторов. Одностадийный пиролиз включает каталитический пиролиз биомассы в том же реакторе с катализатором, тогда как двухступенчатая конфигурация включает реактор с неподвижным слоем / псевдоожиженным слоем, за которым следует каталитический реактор с неподвижным слоем.Первый производит больше кокса, чем второй [33]. В исследовании Mante и Agblevor [33] с использованием двухступенчатой конфигурации реактора для каталитического пиролиза гибридной древесины тополя с HZSM-5 сообщается о низком выходе кокса, составляющем 3,8% по отношению к массе биомассы. Преимущество состоит в том, что каталитический пиролиз выделяющихся паров из биомассы может осуществляться при температуре, отличной от температуры основного реактора пиролиза, в случае использования конфигурации двухступенчатого реактора [18]. Однако, по сравнению со смешиванием катализатора, метод слоя катализатора также приводит к большому количеству полукокса, что приводит к закупорке пор катализатора, что предотвращает диффузию паров через поры [1].
В исследовании Thangalazhy-Gopakumar et al. Было отмечено, что при использовании метода слоя катализатора были обнаружены некоторые некаталитические биомасляные соединения, что позволяет предположить, что соединения первичной смолы превращались во вторичные и третичные соединения смолы до того, как достигли слоя катализатора в будет расщепляться на ароматические углеводороды [1]. Узун и Сарыоглу сообщили, что использование метода слоя катализатора с несколькими типами катализаторов снижает выход жидкости по сравнению со способом смешивания катализаторов [39]. Iliopoulou et al. изучили каталитический пиролиз лигноцеллюлозной биомассы и объяснили эффект in-situ модифицированного металлом ZSM-5 с различным процентным содержанием.Было высказано предположение, что переходные металлы способствуют образованию водорода, который приводит к углеводородным реакциям на кислотных центрах цеолита в режиме слоя катализатора [31].
3.1.2. Метод смешивания катализатора (в слое)
Метод смешивания катализатора может осуществляться либо путем добавления катализатора в биомассу в определенных количествах, либо путем влажной пропитки биомассы. Благодаря лучшему физическому поверхностному контакту между биомассой и катализатором в реакторе пиролиза, смешивание обеспечивает немедленное взаимодействие выделяющихся паров пиролиза с катализатором, что позволяет предположить, что выделившиеся пары могут адсорбироваться на поверхности катализатора и диффундировать в поры для каталитического крекинга [1, 39] .Недостатком является то, что каталитические условия необратимы, поэтому биомасса и катализатор должны работать в одинаковых условиях [18].
Содержание ароматических веществ в биомасле имеет первостепенное значение, и использование катализаторов является одним из альтернативных способов усиления реакций ароматизации (таким образом, повышения качества биомасла). Исследования показали, что метод каталитического смешения обеспечивает лучший массоперенос для крекинга бионефтяных соединений с точки зрения ароматизации и деоксигенации [1, 39].
Thangalazhy-Gopakumar et al.исследовали каталитическое действие цеолита ZSM-5 при пиролизе древесной щепы сосны в среде гелия. Было обнаружено, что использование метода смешивания катализатора с соотношением биомассы к катализатору 1: 9 дает 41,5% выхода ароматических веществ по сравнению с 9,8% при использовании метода слоя катализатора с соотношением биомассы к катализатору 1: 5. В этом исследовании отсутствие соединений гваякола в биомасле показывает, что смешивание катализаторов является эффективным методом крекинга соединений, производных лигнина, до ароматических углеводородов [1]. Pütün et al. изучили пиролиз семян хлопчатника с добавлением MgO в определенных пропорциях к образцам биомассы.По сравнению с обычными результатами пиролиза, содержание ароматических и алифатических соединений было увеличено до значений 35 и 23%, а содержание кислорода было снижено с 9,56 до 4,90% [37]. Результаты пиролиза рисовой шелухи с ZnO, изученные Zhou et al. показали, что смешивание катализатора с различными количествами значительно улучшает качество биомасла с точки зрения содержания водорода, отношения H / C, более высокой теплотворной способности и снижения содержания карбоновых кислот в биомасле [17]. Таким образом, для проектирования крупномасштабных пиролизных установок необходимы эффективные и однородные системы смешения.
3.2. Катализаторы на основе оксидов металлов
Катализаторы на основе оксидов металлов широко изучались в литературе с использованием различных видов биомассы в отношении их влияния на качество и количество продуктов пиролиза. Известно, что оксиды металлов, как и любые катализаторы, влияют на температуру разложения. Соответственно, в термогравиметрическом исследовании, проведенном Chattopadhyay et al. При использовании Cu / Al 2 O 3 в качестве катализатора было отмечено, что оксид алюминия, нанесенный на переходный металл, оказывает сильное влияние на снижение температуры улетучивания летучих веществ [15].Забети и др. применяется аморфный оксид кремния (ASA) на подложке из щелочных или щелочноземельных металлов при пиролизе сосновой древесины. Максимальное количество бионефти было получено с аморфным оксидом кремния без носителя в количестве 42,4 мас.%. Однако фракция с Cs / ASA показала лучшие характеристики с точки зрения удаления кислорода из ароматических углеводородов, что повысило теплотворную способность биомасла [20]. Wang et al. [68] исследовали каталитический эффект на пиролиз лигноцеллюлозной биомассы с использованием катализаторов, включая NiMo / Al 2 O 3 , CoMo / Al 2 O 3 , CoMo-S / Al 2 O 3 , активированный оксид алюминия и пористый диоксид кремния.Для увеличения производства промежуточных продуктов пиролиза (бензола, толуола, ксилола, нафталина) было высказано предположение, что CoMo-S / Al 2 O 3 был наиболее благоприятным среди всех. Однако NiMo / Al 2 O 3 дал самый высокий выход CH 4 со значением 51,82%. Шаданги и Моханти [69] изучили CaO и Al 2 O 3 в пиролизе Hyoscyamus niger L. и подтвердили, что, в соответствии с другими исследованиями, упомянутыми выше, добавление катализаторов в процесс пиролиза значительно снижает выход бионефти, тем не менее, удаляются кислородсодержащие группы, присутствующие в биомасле, что улучшает качество его топлива.Айсу и Кучук исследовали пиролиз восточного гигантского фенхеля ( Ferula orientalis L. ), сравнивая действие катализаторов ZnO и Al 2 O 3 [35]. Al 2 O 3 со значением 79,94% оказался более эффективным, чем ZnO, с точки зрения преобразования биомассы. Однако влияние катализатора на выход бионефти отличалось друг от друга. ZnO увеличивает выход биомассы с увеличением отношения катализатора к биомассе, тогда как выход биомассы снижается с увеличением добавки Al 2 O 3 .Это указывает на то, что Al 2 O 3 способствует образованию газа. В исследовании Йоргуна и Шимшека активированный оксид алюминия использовался в пиролизе Miscanthus × giganteus , и было отмечено, что при высоких скоростях нагрева 60 мас.% Загрузки катализатора в биомассу является эффективным для максимального производства жидкости с значение 51 мас.%. Было обнаружено, что содержание кислорода в бионефти выше, чем в некаталитическом бионефти [70]. Nguyen et al. исследовали пары пиролиза древесной щепы сосны более 20 мас.% Na 2 CO 3 / γ-Al 2 O 3 . Сообщалось, что выход жидкости был снижен, но декарбоксилированию карбоновых кислот способствовал катализатор, в результате чего значение pH составляло 6,5, что позволяет предположить, что катализатор на основе оксида алюминия на основе натрия эффективен для повышения кислотности биомасла. Концентрация углеводородов была увеличена с 0,5 до 17,5%, что свидетельствует о более высокой плотности энергии бионефти [36]. Chen et al. представили распределение газообразных продуктов пиролиза биомассы (рисовая солома и опилки) при температуре 800 ° C с использованием различных оксидов металлов, таких как Cr 2 O 3 , MnO, FeO, Al 2 O 3 , CaO и CuO.Было отмечено, что за исключением CuO и Al 2 O 3 , все катализаторы заметно улучшили газообразование [56]. Чжоу и др. [17] исследовали пиролиз рисовой шелухи с добавлением ZnO. Результаты этого исследования показали, что ZnO демонстрирует тенденцию к снижению выхода бионефти с увеличением соотношения биомассы к катализатору. Однако ZnO улучшил композиционное качество биомасла с точки зрения низкомолекулярных соединений, включая алканы, алкены, стирол и алкилфенолы (таким образом, повышая стабильность биомасла).Ноккосмаки и др. также исследовали тот же катализатор для превращения паров пиролиза сосновых опилок, и было показано, что вязкость каталитического биомасла снижается на 40% по сравнению с результатами некаталитического пиролиза [34]. Pütün et al. [37] показали, что использование MgO в качестве катализатора пиролиза семян хлопка в реакторе с неподвижным слоем улучшило качество биомасла за счет удаления кислородсодержащих соединений, повышения теплотворной способности и увеличения содержания ароматических веществ в биомасле.
3.3. Цеолитные катализаторы
Цеолиты, имеющие тетраэдрическую структуру и кислотную природу, представляют собой трехмерные алюмосиликаты, связанные через атомы кислорода и поддерживаемые каналами и полостями, в результате чего пористая структура обладает исключительной каталитической активностью.Каждый тип этих тетраэдрических цеолитов с общим балансом заряда минус один имеет Si или Al в центре и атомы кислорода в углах структуры [71].
Цеолиты обладают следующими характеристиками: (1) крекинг деоксигенированных соединений за счет избирательности формы, (2) большая площадь поверхности, (3) различные размеры каналов и пор и (4) высокая адсорбционная способность [22, 72]. Физические свойства цеолитов зависят от условий синтеза, включая температуру, гелевые предшественники, структурно-регулирующий агент [73].Размер пор и каркас цеолитов имеет тенденцию влиять на состав продукта через несколько реакций, ограничивающих образование углеводородов, размер которых превышает размер пор цеолитов. Это называется селективностью формы и является одним из наиболее важных факторов, отличающих цеолиты от других типов катализаторов. Селективность основана на том, могут ли ароматические соединения, полученные из паров пиролиза, входить, образовываться и диффундировать из пор цеолита [22, 23]. Селективность формы цеолитов подробно обсуждается в разделе 3.3.1.1, демонстрирующий ZSM-5 как цеолитный тип.
Основная причина, по которой цеолиты обычно используются в пиролизе биомассы, заключается в том, что их различная кислотность и избирательность по форме обеспечивают преимущество перед алюмосиликатными катализаторами аморфной структуры с точки зрения реакций ароматизации. Кислотность зависит от отношения Si / Al в структуре цеолита и может быть обусловлена кислотными центрами Бренстеда и Льюиса [22]. Кислотность влияет на каталитические реакции, обеспечивая повышенную крекирующую активность при уменьшении отношения Si / Al [23].Следовательно, распределение кислотных центров в порах цеолитов имеет большое значение с точки зрения предотвращения реакций образования кокса во внутренних порах цеолита. Низкое отношение Si / Al приводит к увеличению количества кислотных центров в непосредственной близости. По этой причине количество реакций образования кокса, которые превращают ароматические углеводороды в соединения кокса, увеличиваются. Следовательно, для цеолитов требуется оптимальная кислотность, если они используются в пиролизе биомассы [19].
Помимо распределения кислотных центров, пористая структура отдельного цеолита играет важную роль для селективности продуктов и с точки зрения содержания ароматических веществ в бионефти.Поры цеолитов характеризуются размером кольца, определяющего поры, то есть n-числом кольца, которое называют числом атомов Si или Al в кольце [74]. Длина углеводородной цепи продуктов пиролиза и, следовательно, распределение ароматических соединений по размерам зависит от размера пор цеолита и площади внутренней поверхности пор. Как правило, более крупные поры и площадь поверхности приводят к образованию углеводородов с длинной цепью. Площадь микропористой поверхности катализатора определяет выход газообразных продуктов пиролиза, а площадь макропористых частиц определяет выход жидкости [24, 37].Ряд цеолитов с различным размером пор изучен в литературе [39, 75, 76]. Y цеолит (фожазит), имеющий кубическую структуру с системой пор, состоящей из 12-членных кольцевых кольцевых каналов, имеет самый большой средний размер пор (7,4 Å) и внутреннее поровое пространство (11,24 Å) [22, 23]. Такой относительно большой размер пор влияет на катализируемые реакции, приводя к меньшему контакту между поверхностью пор и парами пиролиза, тем самым приводя к меньшему крекингу оксигенатов, полученных из биомассы. Кроме того, прямые каналы с большим размером пор не обеспечивают избирательности формы по сравнению с другими цеолитами, которые имеют меньшие и синусоидальные каналы, которые обеспечивают избирательность формы [23].Несмотря на большой размер пор [73], бета-цеолит имеет тетрагональную кристаллическую структуру и имеет 12-членные прямые каналы, пересекаемые 10-членными кольцевыми каналами, что делает его более эффективным для производства ароматических углеводородов, чем Y-цеолиты [23]. Ферриерит, как цеолит со средним размером пор, имеет ромбическую структуру с 8- и 10-членными каналами с внутренним пространством пор 6,31 Å [23, 73].
Благодаря наличию двух параллельных каналов, соединенных с 12-членными кольцами и 8-членными кольцами, морденит классифицируется как цеолит с крупными порами и имеет орторомбическую структуру [22, 23, 73].ZSM-5, состоящий из орторомбической структуры MFI, состоит из 10-членных прямых каналов, соединенных 10-членными синусоидальными каналами [71]. Общие физико-химические свойства цеолитов представлены в Таблице 2.
12151 –8 Внутреннее поровое пространство (Å) 643,1 Катализатор ZSM-5 Морденит Бета-цеолит I1413 906 908 цеолит Y1413A 908 цеолит 906 MFI MOR BEA FAU FER Размер пор 3 2 3 3 12–12 12–12 8–10 Размер пор (Å) 5.1 × 5,5 7,0 × 6,5 7,6 × 6,4 7,4 × 7,4 4,2 × 5,4 5,3 × 5,6 5,7 × 2,6 5,6 × 5,6 3,5 × 4,8 5,2–5,5 4,2–6,7 6,1–6,68 11,24 6,31 Площадь поверхности BET (м 2 / г) 395,5 9015,72 395,5 9015,72 809.1 *
Таблица 2.
Физико-химические свойства наиболее часто используемых цеолитов [22, 72, 76, 77].
* Информация отсутствует.
Цеолиты со средним и большим размером пор способствуют более быстрой диффузии реагентов по сравнению с цеолитами с меньшим размером пор, что приводит к увеличению количества ароматических соединений в жидкой фракции продукта пиролиза. Однако цеолиты с большим размером пор производят менее ароматические вещества, чем цеолиты со средним размером пор, поскольку большие поры способствуют образованию кокса [22].Соответственно, недавнее исследование подтвердило, что ZSM-5 со средним размером пор и средней площадью внутренней поверхности пор способствует более высокому производству ароматических углеводородов и более низкому выходу кокса [19].
3.3.1. Цеолит ZSM-5
ZSM-5, как один из наиболее часто используемых цеолитов при пиролизе биомассы [23], состоит из звеньев пентасила и имеет орторомбическую структуру [74]. Состоящий из 10-членных прямых каналов, соединенных 10-членными синусоидальными каналами, ZSM-5 обладает значительно большей крекирующей активностью, чем другие цеолиты [23, 27].ZSM-5 широко используется в качестве катализатора в нефтяной промышленности из-за его селективности формы, исключительного размера пор с стерическими затруднениями, термической стабильности и кислотности твердых веществ [78].
По сравнению с другими цеолитами, поры среднего размера ZSM-5 затрудняют образование внутри пор более крупных предшественников ароматического кокса [79]. Исследования показали, что, независимо от сырья, использование ZSM-5 в пиролизе биомассы снижает содержание кислородсодержащих соединений в бионефти и одновременно увеличивает количество ароматических соединений [80–84].Деоксигенация кислородсодержащих органических соединений происходит внутри пор цеолита ZSM-5 посредством таких реакций, как дегидратация, декарбоксилирование и декарбонилирование [27, 31, 32]. Установлено, что при более низких температурах кислород удаляется в виде H 2 O, тогда как при более высоких температурах основными продуктами удаления кислорода являются CO и CO 2 [31]. Удаление кислорода, в первую очередь в форме CO и CO 2 , более предпочтительно, поскольку оно приводит к меньшему осаждению углерода на цеолите и большему образованию водорода и, следовательно, меньшему содержанию воды в бионефти [31].
3.3.1.1. Селективность формы ZSM-5
Явление избирательности формы можно объяснить совместным действием молекулярного сита и каталитической реакции, которая происходит на внешних и внутренних кислотных центрах цеолитов [85]. ZSM-5, имеющий пористую структуру, может быть использован для избирательного катализа при условии, что не только размер пор, но и размеры реагирующих и диффундирующих молекул аналогичны порам цеолита [19]. Таким образом, влияние размера пор и стерических затруднений ZSM-5 на каталитические реакции должно быть исследовано, если цеолиты с лучшими характеристиками должны быть разработаны для преобразования биомассы [73].
Образование продуктов пиролиза с избирательным катализом формы зависит от двух типов селективности: (1) селективность реагента и продукта и (2) селективность переходного состояния, которые описываются их эффектами массопереноса и внутренними химическими эффектами соответственно [22, 73, 85]. Основная идея избирательности реагентов и продуктов заключается в том, что диффузия реагентов и продуктов внутри пор цеолита затруднена. Определенный размер пор ZSM-5 влияет на диффузию реагентов внутри пор, за исключением тех, размер которых превышает размер пор ZSM-5, тем самым предотвращая их достижение каталитически активных центров и, следовательно, позволяя каталитическому разложению только на внешних активных центрах. [73, 85].Из-за геометрии пор ZSM-5 образование определенных продуктов ограничено, что влияет на химическую реакцию и, таким образом, вызывает селективную гомогенизацию продуктов пиролиза [85].
Селективность ZSM-5 была тщательно изучена, и чаще обнаруживается, что она вызывает селективность по сравнению с ароматическими соединениями [49]. Михалчик и др. [23] изучали различные цеолиты для преобразования нескольких типов биомассы и компонентов биомассы. По результатам этого исследования было обнаружено, что ZSM-5 способствует образованию p -ксилола в изобилии во всех случаях пиролиза биомассы.В исследовании Foster et al. [19], HZSM-5 для превращения фурана показал тенденцию к селективности по ароматическим соединениям, давая более высокий выход ароматических соединений в виде нафталина, имеющего самый высокий процент 30,4% от общего количества ароматических соединений. Fogassy et al. [86], исследуя селективность формы цеолитов по отношению к фрагментам лигнина, выявили, что большинство фенольных соединений, полученных в результате разложения лигнина, слишком велики для проникновения через поры цеолита, поэтому преобразование этих соединений происходит во внешних активных центрах.Как Yu et al. [22] предположили, однако, что при более высоких температурах эффективный размер пор ZSM-5 увеличивается, позволяя молекулам большего размера, чем размер пор ZSM-5, достигать внутренних каталитических активных центров. Jae et al. исследовали роль размера пор нескольких типов цеолитов в пиролизе глюкозы (используя кинетические диаметры продуктов и реагентов в качестве влияющих параметров), чтобы определить, происходит ли каталитическая реакция внутри пор или на внешней поверхности [73]. Кинетический диаметр оценивался по свойствам в критической точке.Было обнаружено, что ZSM-5 позволяет промежуточным продуктам и продуктам пиролиза (таким как бензол, толуол, инден, этилбензол, p -ксилолы) диффундировать в поры из-за их значительно меньшего кинетического диаметра, чем у ZSM-5.
При повышении температуры до 600 ° C из-за термической деформации такие соединения, как нафталин, который дает самый высокий выход ароматических углеводородов, вероятно, будут образовываться внутри пор, а также на поверхности. Согласно этому исследованию, был сделан вывод, что помимо размера пор внутреннее поровое пространство ZSM-5 влияет на каталитическую реакцию.Это говорит о том, что на конверсию биомассы с ZSM-5 влияют ограничения массопереноса, а также эффекты переходного состояния [73].
3.3.1.2. Кислотность ZSM-5
Помимо избирательности формы, кислотность ZSM-5 играет важную роль в превращении оксигенатов в ароматические соединения. Принято считать, что кислотные центры Бренстеда являются активными центрами, которые превращают кислородсодержащие соединения в ароматические соединения, а не кислотные центры Льюиса. Крекинг крупных кислородсодержащих соединений происходит на кислотных центрах внешней поверхности ZSM-5, тогда как превращение более мелких в ароматические соединения происходит на кислотных центрах внутри пор [22, 87].Следовательно, необходимо исследовать количество как внешних, так и внутренних кислотных центров, чтобы разработать лучший способ образования ароматических углеводородов. Как объяснил Ван Сантен, кислотные центры Бренстеда образуются в результате замены кремнезема с валентностью четыре атомом металла, чаще всего алюминия с валентностью три [88]. Таким образом, это делает кислотные центры Бренстеда донорами протонов. Si и Al связаны с присоединенным к протону атомом кислорода, что приводит к химически более стабильной структуре [88, 89].С другой стороны, кислотные центры Льюиса являются акцепторами электронных пар, и природа этих центров связана с атомами алюминия, расположенными в каркасе [89, 90].
Помимо природы кислотных центров, молярное соотношение между SiO 2 и Al 2 O 3 в цеолитном каркасе также влияет на реакционную способность и характеристики ZSM-5. Оптимальное соотношение Si / Al необходимо для обеспечения высокой доступности кислотных центров Бренстеда для адекватной кислотности и для поддержания расстояния между кислотными центрами, чтобы ограничить реакции образования кокса [19].По мере уменьшения отношения Si / Al (увеличения кислотности ZSM-5) кислотные центры будут находиться в непосредственной близости друг от друга, что приведет к вторичным реакциям превращения ароматических соединений в частицы кокса [19]. Foster et al. [19] исследовали влияние ZSM-5 с различным соотношением Si / Al на пиролиз глюкозы. Это исследование показало, что уменьшение отношения Si / Al способствует образованию дополнительных кислотных центров ZSM-5 с увеличением выхода кокса. В исследовании Carlson et al. [79], ZSM-5 (SiO 2 / Al 2 O 3 = 15) способствовал образованию кокса в основном на поверхности катализатора, давая самый высокий выход кокса 33% (где соотношение катализатора к биомассе составляло 19 ).Также было указано, что образование кокса на внешних порах ZSM-5 не приводит к значительному снижению выхода ароматических углеводородов, но влияет на селективность по отношению к легким углеводородам, что приводит к более низким выходам бензола и толуола и более высоким выходам нафталина и индана.
3.4. Общее воздействие катализаторов на биомасло
Известно, что катализаторы оказывают сильное влияние на пиролиз с точки зрения распределения продуктов, химической гомогенизации и увеличения фракционного выхода продукта, повышая качество продуктов пиролиза.Среди катализаторов цеолиты и оксиды металлов в основном исследовались для преобразования биомассы и оказались эффективными в изменении состава биомасла за счет снижения содержания кислородсодержащих соединений посредством реакций деоксигенации и увеличения выхода ароматических соединений, таким образом производя более гомогенную и стабильную органическую фракцию. которые могут быть переведены на дизельное топливо [30, 39]. Чтобы рассматривать продукты пиролиза, особенно бионефть, для стационарного применения топлива или выработки тепла / электроэнергии, необходимо оценить свойства, включая кислотность, вязкость, стабильность и содержание ароматических веществ в биомасле [20].Таким образом, влияние катализаторов на бионефть необходимо рассматривать, как подробно обсуждается ниже, чтобы лучше понять преобразование биомассы.
3.4.1. Выход ароматических веществ в биомасле
Содержание ароматических веществ в биомасле имеет большое значение с точки зрения производства дизельного топлива из сырья биомассы и отходов биомассы. Среди ароматических углеводородов количество бензола, толуола, этилбензола и ксилолов (компоненты BTEX) являются наиболее важными исходными материалами, которые необходимо учитывать в нефтехимической промышленности [68, 87].
Было показано, что использование катализаторов увеличивает выход биомасла, а также увеличивает содержание ароматических углеводородов в биомасле, что является хорошим индикатором качества топлива. Kim et al. [87] изучали каталитический пиролиз остатков мандарина с высоким содержанием лигнина и обнаружили, что использование HZSM-5 с кислотностью 23 и 80 повышает выход моноароматических соединений с 3,4 до 36,0 и 41,0% соответственно. Из исследования Zheng et al. [76], изменение размера кристаллов ZSM-5 влияло на выход ароматических соединений и селективность по БТК, так что меньший размер кристаллов давал максимальный выход ароматических соединений и самую низкую селективность по БТК со значениями 38.4 и 36,3% соответственно. Однако кристаллы большего размера демонстрировали самый низкий выход ароматических соединений и самую высокую селективность по БТК со значениями 31,1 и 42,6% соответственно. Таким образом, меньший размер кристаллов (200 нм) оказался оптимальным для высокого выхода ароматических веществ.
Zhang et al. [83] сравнили поведение пиролиза лигнина осины под действием катализатора H-Y и HZSM-5. При соотношении катализатора к сырью 3: 1 получение ароматических углеводородов показало максимальное значение 23% при использовании HZSM-5 в качестве катализатора, где содержание кислорода в ароматических соединениях снизилось примерно до 4%, а ВТС фракции была оценена приблизительно как 46 МДж / кг, что ближе к бензину и дизельному топливу.Было указано, что HZSM-5 более эффективен, чем H-Y, в превращении фенольных соединений в ароматические углеводороды [83] из-за его более высокой кислотности и меньшего размера пор по сравнению с HY [83]. Точно так же Паттия и др. [75] изучили ZSM-5 и два мезопористых материала, включая Al-MCM-41 и Al-MSU-F, чтобы исследовать быстрый пиролиз корневища маниоки. Выявлено, что из всех протестированных в исследовании катализаторов ZSM-5 дает самый высокий выход ароматических углеводородов в следующем порядке: толуол> бензол> 4,7-диметилиндан> p -этилстирен> 5-метилиндан> ксилолы. .
Помимо цеолитов, влияние оксидов металлов на ароматизацию изучалось исследователями [7, 49, 91, 92]. По результатам исследования Ateş и Işıkdağ [91], использование оксида алюминия в качестве катализатора при пиролизе кукурузного початка продемонстрировало тенденцию к ускорению образования 1,1,3,3-тетраметилиндана, бензола и 1-метил-4- (пенилметил). ), являющиеся наиболее важными моноароматическими соединениями. Было обнаружено, что образование нафталина, 1- (2-пропенил) -, соединения ПАУ, увеличивается при умеренной температуре с использованием катализатора.Сметс и др. [93] сравнили различные катализаторы, включая HZSM-5, γ-Al 2 O 3 и Na 2 CO 3 . Карбонат натрия был наиболее эффективным катализатором для увеличения выхода ароматических углеводородов после HZSM-5. Wang et al. [92] также провели сравнительное исследование каталитической конверсии остатков трав по сравнению с оксидом алюминия, ZSM-5 и Al-SBA-15, где оксид алюминия дает самый высокий выход биомасла. Таким образом, исследователи этого исследования исследовали влияние оксида алюминия на выход ароматических соединений в терминах соединений толуола, этилбензола и p -ксилола и обнаружили, что процентное содержание ароматических фракций увеличилось с 8.02 до 10,93%.
3.4.2. Кислотность биомасла
Кислотность биомасла обусловлена летучими кислотами, в основном карбоновыми кислотами, то есть муравьиной кислотой и уксусной кислотой [58]. Фенольные соединения также повышают кислотность биомасла [20]. Определение кислотности биомасла осуществляется путем измерения значения pH или общего кислотного числа. Значение pH является показателем для оценки коррозионной активности бионефти, тогда как общее кислотное число используется в качестве показателя качества для использования бионефти при совместной переработке нефтеперерабатывающих предприятий и относится к уровню кислотных компонентов в масло [58].
Исследования ясно показали, что органические кислоты восстанавливаются катализаторами [36], тем самым облегчая использование биомасла в топливных приложениях. Главный вопрос заключается в том, чтобы найти наиболее подходящее сочетание катализатора и биомассы с учетом условий процесса для систем пиролиза, чтобы заменить бионефть эквивалентами ископаемого топлива (такими как дизельное топливо и бензин).
Забети и др. [20] изучали аморфный оксид кремния, модифицированный щелочными или щелочноземельными металлами, такими как Na, K, Cs, Mg и Ca.Был сделан вывод, что среди всех катализаторов, испытанных в исследовании, K / ASA был наиболее эффективным катализатором для снижения содержания карбоновых кислот и карбонилзамещенных фенолов в биомасле. Чжоу и др. [17] исследовали влияние ZnO на физико-химические свойства биомасла рисовой шелухи. Значение pH каталитического биомасла было зарегистрировано как 4,35, тогда как значение pH некаталитического биомасла было 4,15. Таким образом, это указывает на влияние катализатора ZnO на снижение кислотных соединений в биомасле. Абу Бакар и Титилойе [32] изучали пиролиз рисовой шелухи на различных катализаторах, включая ZSM-5, Al-MCM-41, Al-MSU-F и BRHA (зола брунейской рисовой шелухи).Было показано, что катализаторы снижают кислотное число с 55 мг / КОН до 39–47 мг / КОН, при этом ZSM-5 и BRHA имеют самое низкое значение. Кроме того, значение pH каталитического биомасла рисовой шелухи было зарегистрировано в диапазоне 2,7–3,0. Большинство кислотных соединений составляли карбоновые кислоты, причем уксусная кислота имела самый высокий процент. Mante и Agblevor [33] изучали HZSM-5 в качестве дезоксигенирующего катализатора для превращения гибридной древесины тополя в биосинхронизирующее масло. Как указано в исследовании, значение pH легкой биосинкрудированной нефти, содержащей в основном ароматические углеводороды, было увеличено с 2.60 до 4,05 из-за HZSM-5.
3.4.3. Вязкость биомасла
Высокая вязкость биомасла по сравнению с обычным топливом является одним из недостатков его использования в топливных приложениях. Наиболее важно то, что в случае биомасла, использующего двигатели внутреннего сгорания, высокая вязкость увеличивает размер капель распыляемой форсунки, тем самым влияя на воспламенение капель [94]. Следовательно, уменьшение вязкости биомасла для улучшения свойств топлива имеет важное значение. Исследования показали, что использование катализаторов улучшает топливные свойства биомасла за счет снижения вязкости [53, 95].
Azargohar et al. провели эксперименты по некаталитическому пиролизу для нескольких отходов биомассы, и было обнаружено, что вязкость бионефти в диапазоне от 63 до 418 сП была намного выше, чем у сырой нефти (~ 23 сП), что потребовало дальнейшего процесса повышения качества. . Также было обнаружено, что причина высокой вязкости в основном связана с производными лигнина углеводородами с большой молекулярной массой [96]. Однако в исследовании Fan et al. при пиролизе рапсовой соломы над нанокристаллическим HZSM-5 динамическая вязкость составила 5.12 мм 2 с −1 , что находится в пределах допустимых пределов для дизельного топлива, как указано в исследовании [95]. Mante et al. исследовали гибридный пиролиз древесины тополя с аддитивным действием катализатора FCC на основе Y-цеолита по отношению к ZSM-5. Было обнаружено, что катализатор FCC / ZSM-5 более эффективен, чем чистый ZSM-5, в снижении вязкости образцов бионефти, что указывает на синергетический эффект гибридного катализатора, а также предполагает, что углеводороды с меньшей массой образуются за счет присутствия катализатора [ 53].Mante и Agblevor [33] изучали пиролиз древесины гибридных тополей с добавкой ZSM-5. Они классифицировали жидкую фракцию продукта пиролиза как LBS (низкобиосинкрудную) нефть, содержащую в основном ароматические углеводороды, и HBS (высокобиосинкрудную) нефть, которая состоит в основном из фенолов, метилзамещенных фенолов, нафталинов, бензолдиолов и нафталенола. Вязкость масла LBS, которая была значительно ниже, чем вязкость некаталитического биомасла (285 сСт), составляла 4,90 сСт. Было высказано предположение, что более низкая вязкость объясняется каталитическим крекингом левоглюкозана и деполимеризацией продуктов, полученных из лигнина [33].Шаданги и Моханти провели несколько исследований с использованием различных видов биомассы над CaO, каолином и Al 2 O 3 [69, 97, 98]. Было обнаружено, что независимо от типа биомассы СаО производит бионефть с более низкой вязкостью, чем некаталитическое биомасло, по сравнению с другими катализаторами, используемыми для их исследований. Вязкость биомасла, полученного с использованием СаО, составляла 0,019629 Па [98] и 9,007 сП [69], что указывает на то, что использование катализатора способствует снижению вязкости примерно на 62 и 74,5% соответственно.Абу Бакар и Титилойе изучали ZSM-5, Al-MCM-41, Al-MSU-F и BRHA (зола брунейской рисовой шелухи) на предмет превращения рисовой шелухи в биомасло, а вязкость биомасла была такой, как указано, 1,55, 1,65, 1,49 и 1,57 сСт соответственно. Все катализаторы, использованные в исследовании, снизили вязкость примерно на 1,7–11,3% и немного увеличили содержание воды, что указывает на то, что катализаторы способствовали реакции дегидратации [32].
3.4.4. Стабильность биомасла
Биомасло не так химически или термически стабильно, как ископаемое топливо, из-за высокого содержания кислородсодержащих соединений [94].Сообщается, что при температурах выше 40 ° C или во время длительного хранения вязкость биомасла увеличивается из-за химических реакций между такими компонентами, как кетоны и альдегиды, что приводит к образованию соединений с высокой молекулярной массой [20]. Таким образом, ожидается, что бионефть с более низким содержанием карбонильных групп будет более стабильной. Использование катализаторов для облегчения транспортировки и хранения бионефти приводит к усилению реакций крекинга тяжелых молекул, а также удалению кислородсодержащих соединений, что приводит к производству бионефти с высокой стабильностью [99].Не существует стандартного метода определения стабильности биомасла; однако исследователи разработали несколько методов [100–102].
В исследовании Zabeti et al., Где Cs / ASA был признан наиболее эффективным катализатором для удаления кислородсодержащих соединений и увеличения выхода ароматических веществ, сравнивали все катализаторы, испытанные в исследовании. Результаты эксклюзионной хроматографии (SEC) показали, что молекулярная масса биомасла смещается в области более высоких масс после старения [20]. Мант и Агблевор провели испытание на стабильность каталитических биомасел (масла с низкой и высокой биосинхронизацией), полученных из гибридной древесины тополя.Испытания на стабильность и старение проводили в гравитационной печи при 90 ° C в течение 24 часов. Также была измерена вязкость образцов биомасла, хранящихся при 40 ° C в течение более 10 месяцев, и было обнаружено, что изменение вязкости составило 5% для масла с низким содержанием биосинкрудии и 27,9% для масла с высоким содержанием биосинкрудирования. Был сделан вывод, что каталитические биомасла термически стабильны и могут храниться при комнатной температуре более 10 месяцев без какого-либо значительного увеличения вязкости [33]. Ноккосмаки и др. исследовали пиролиз сосновых опилок с добавкой ZnO в качестве катализатора.Тест стабильности был проведен при 80 ° C в течение 24 часов и показал, что вязкость изменялась при использовании ZnO. Изменение вязкости составило 55%, что значительно ниже, чем у некаталитического биомасла (129%) [34]. Думан и др. исследовали влияние добавления метанола на стабильность биомасла, полученного из сафлорового жмыха, с использованием FCC в качестве катализатора. Добавление метанола снижает вязкость. Вязкость была намного ниже при более высоких температурах, что указывает на более стабильное биомасло. После испытания на старение при 40 ° C в течение 168 ч вязкость увеличилась на 46.63 и 21,08% в случае сырого бионефти и биомасла с добавлением метанола, соответственно [57].
. Установка для пиролиза шин / резины / котел — Купить установка для пиролиза шин, котел центрального отопления, котел для домашнего отопления продукт на Alibaba.com
Установка для пиролиза шин / резины / котел
Котел для вулканизации / резервуар для шин / восстановления протектора шин
9000 Контроллер количество вулканизируемых шин каждый раз:
spec: 16,20,22.5,24
* Полуавтоматический
Количество вулканизируемых шин каждый раз:
1.Упаковка корпуса резервуара: высококачественная минеральная вата, стекловолокно
5 мм2, достоинства: защита от ржавчины, высокая стойкость к ударам, хороший эффект сохранения тепла (каждый раз вулканизации может быть экономия энергии на 15% по сравнению с резервуаром из оцинкованного листа толщиной 0,05 мм)
2.Встроенный: Защита от высоких температур, двигатель высокого давления, Приводные велосипедные вентиляторы,
3.Масло, электрическое.Установка подогрева трех видов воздуха (свободный выбор)
4. Автоматическое управление температурой, временем сигнализация
5. Мин. бак можно загружать в 6 шин каждый раз
Макс. бак можно загружать в 24 шины каждый раз
Может быть настроен в соответствии с вашими потребностями.
Котел вулканизации / резервуар для шин / оборудования для восстановления протектора шин
1. Шины помещаются в эту камеру вулканизации, и предварительно отвержденный протектор прилипает к шине в результате вулканизации. обработать.
2. Мощность 64 кВт может быть рассчитана по вашему совету.
3. Давление в баке и оболочке упаковки падает до давления окружающей среды, которое контролируется переключателем нулевого давления.
Технический параметр
RT-1500
RT-1500
2000 5
Классификация / модель
RT-1200
RT-1500
RT-2200
1
2
3
4
5
1500
1800
2000
2200
Эффективная длина (мм)
3 3000-10000
3000-10000
-15000
3000-15000
3000-20000
Материал
16MnR / Q235B
Расчетная температура
180 ° C
Экспериментальное давление
.0 МПа
.Пиролизные котлы обогрева: виды, устройство, обзор лучших производителей
Классификация / модель
RT-1200
RT-1500
RT-2200
1
2
3
4
5
1500
1800
2000
2200
Эффективная длина (мм)
3 3000-10000
3000-10000
-15000
3000-15000
3000-20000
Материал
16MnR / Q235B
Расчетная температура
180 ° C
Экспериментальное давление
.0 МПа
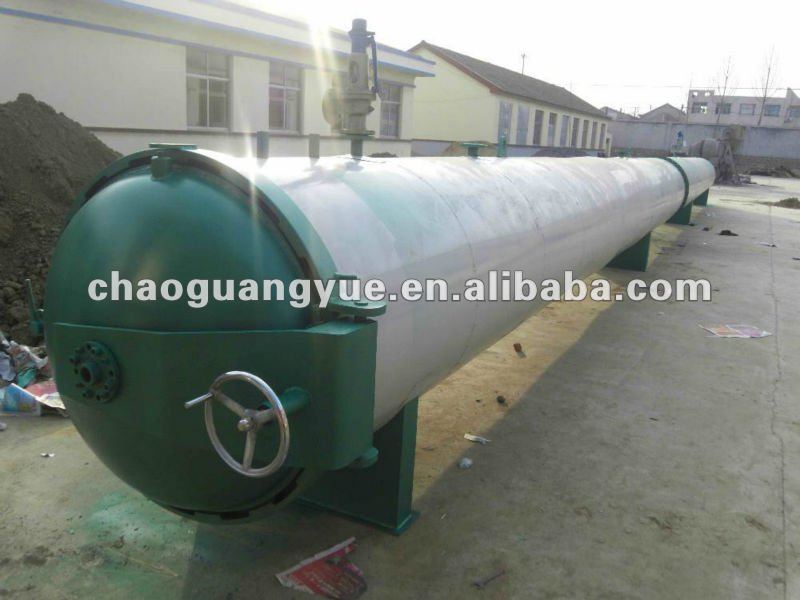
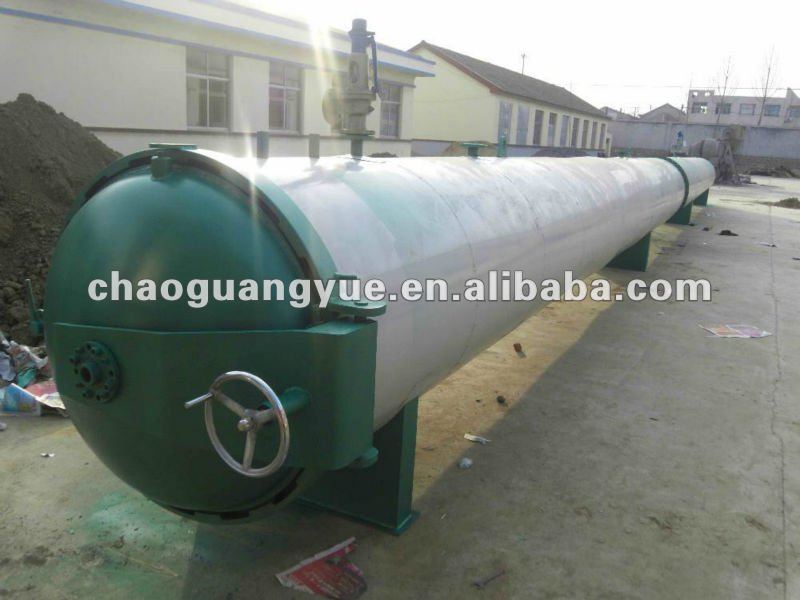
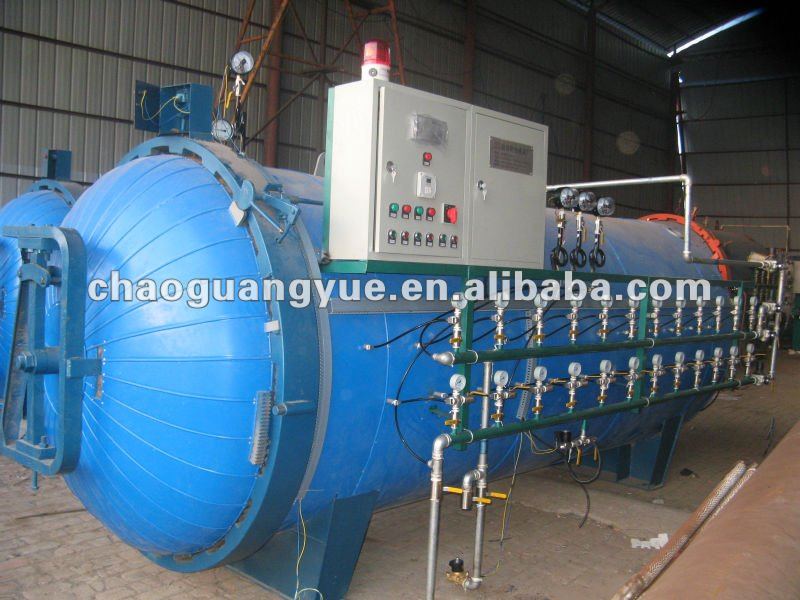
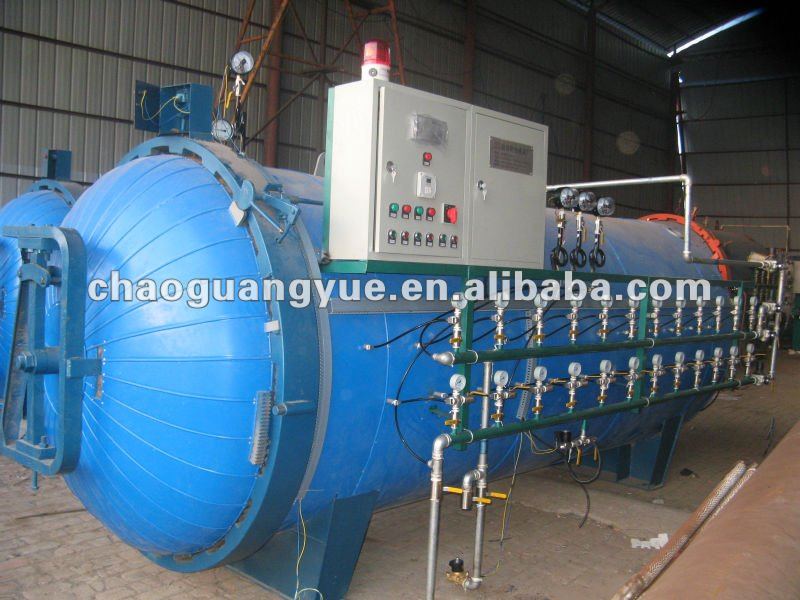
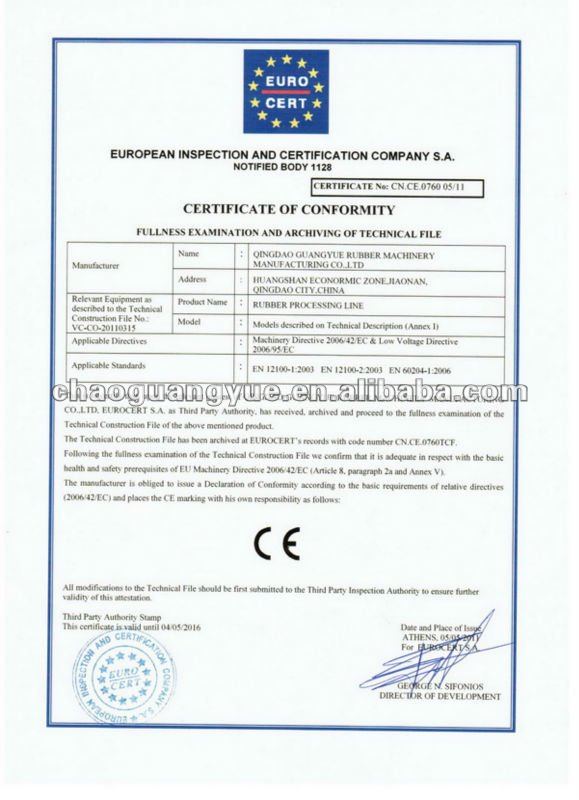
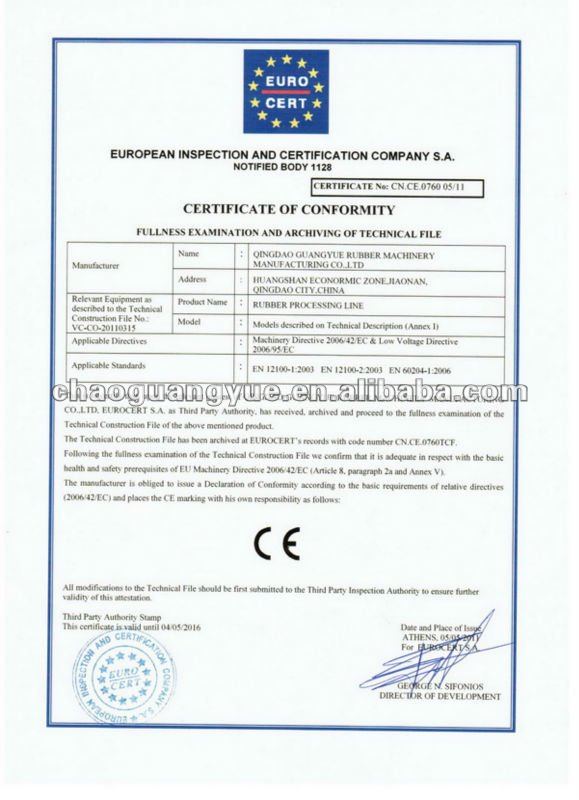
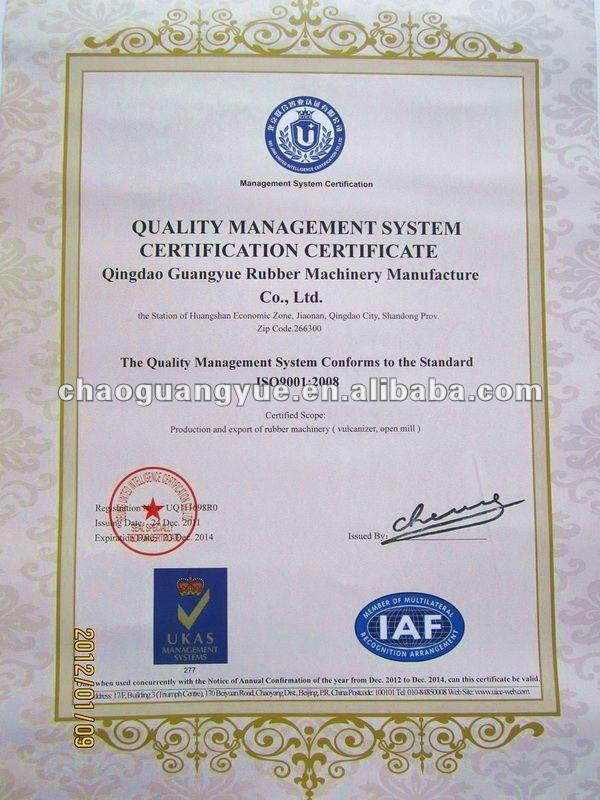
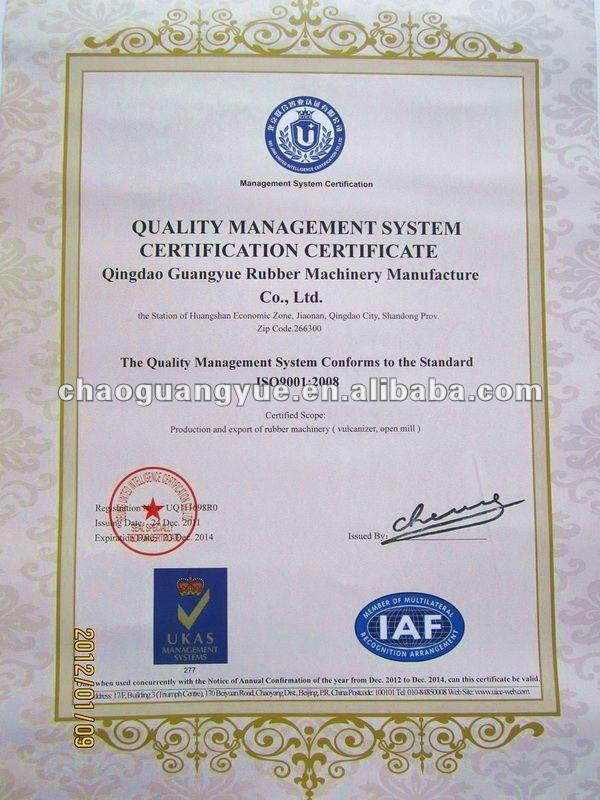