Основные работы, выполняемые на токарном станке / Кустарь
Основные работы, выполняемые на токарном станке
Элементы и режимы резания
Прежде чем говорить о способах обработки, познакомимся вкратце с элементами и режимом резания.
Здесь нам встретятся новые понятия: глубина резания, подача, скорость резания.
Все они связаны между собой, и величина их зависит от различных причин.
Глубиной резания называется толщина слоя металла, снимаемого за один проход резца. Она обозначается буквой t и колеблется от 0,5 до 3 и больше миллиметров при черновой обработке до десятых долей миллиметра при чистовой обточке.
Подача —это движение резца вдоль обрабатываемой поверхности. Численно она выражается в миллиметрах, обозначается буквой S и указывает на величину смещения резца за один оборот детали. В зависимости от прочности обрабатываемого материала, жесткости узлов станка и резца, величина подачи может меняться от 0,1—0,15 мм/об до 2—3 мм/об при скоростных режимах резания. Чем тверже металл, тем меньше должна быть подача.
Скорость резания зависит от числа оборотов шпинделя и диаметра детали и подсчитывается по формуле.
Выбирая ту или иную скорость резания, нужно учитывать твердость обрабатываемого материала и стойкость резца, которая измеряется временем непрерывной работы его до затупления в минутах. Она зависит от формы резца, его размеров, материала, из которого изготовлен резец, от точения с охлаждающей эмульсией или без нее.
Наибольшую стойкость имеют резцы с пластинками из твердых сплавов, наименьшую — резцы из углеродистой стали.
Вот, например, какие скорости резания можно рекомендовать при точении различных материалов резцом из быстрорежущей стали. Стойкость его без охлаждения равна 60 минутам.
Примерные данные о скорости резания металлов:
Материал | Скорость резания в м/мин. |
---|---|
Серый чугун | 25 |
Твердая сталь | 25 |
Мягкая сталь | 50 |
Бронза | 75 |
Латунь | 100 |
Алюминий | 250 |
Обтачивание гладких цилиндрических поверхностей
Гладкие цилиндрические поверхности деталей обтачивают проходными резцами в два приема. Сначала черновым резцом производят обдирку — грубое обтачивание, — быстро снимая основную массу лишнего металла. На рисунке изображен прямой резец для черновой обработки:

Черновые резцы: а — прямой; б — отогнутый; в — конструкции Чекалина.
Отогнутый резец удобен при протачивании поверхности детали около кулачков патрона и для подрезания торцов. Обычно резцы имеют рабочий ход только в одну сторону, чаще всего справа налево. Двухсторонний проходной резец конструкции токаря-новатора Н. Чекалина позволяет ликвидировать обратный холостой ход резца, сокращая время обработки.
После обточки черновым резцом на поверхности детали остаются крупные риски и качество обработанной поверхности поэтому невысоко. Для окончательной обработки служат чистовые резцы:
Чистовые резцы: а — нормальный; б — с широкой режущей кромкой; в — отогнутый, конструкции А. В. Колесова.
Нормальный тип чистового резца применяется при точении с небольшой глубиной резания и малой подачей. Чистовой резец с широкой режущей кромкой позволяет работать на больших подачах и дает чистую и гладкую поверхность.
Подрезание торцов и уступов
Для подрезания торцов и уступов на токарном станке пользуются обычно подрезными резцами. Такой резец изображен на следующем рисунке:
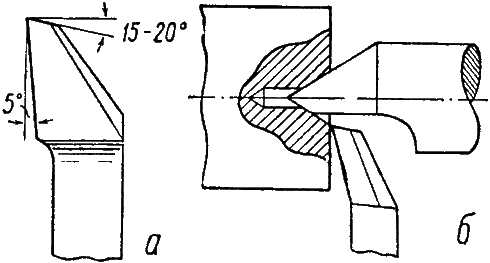
Подрезание в центрах: а — подрезной резец; б — подрезание торца с полуцентром.
Его лучше употреблять при точении детали в центрах. Для того, чтобы торец можно было обрабатывать целиком, в заднюю бабку вставляется так называемый полуцентр.
Если деталь закреплена только одним своим концом — при обработке в патроне, — то для проточки торца может быть использован и проходной отогнутый резец. Для этой же цели и для проточки уступов используются и специальные подрезные упорные резцы, которые работают с поперечной и с продольной подачей.

Подрезание торцов: а — подрезание проходным отогнутым резцом, б — подрезной упорный резец и его работа.
При подрезании торцов и уступов юный мастер должен следить за тем, чтобы вершина резца была всегда установлена строго на уровне центров. Резец, установленный выше или ниже уровня центров, оставит на середине сплошного торца неподрезанный выступ.
Вытачивание канавок
Для вытачивания канавок служат прорезные резцы. Их режущая кромка точно воспроизводит форму канавки. Так как ширина канавок обычно невелика, режущую кромку прорезного резца приходится делать узкой, поэтому она получается довольно ломкой. Для повышения прочности такого резца высоту его головки делают в несколько раз больше ширины.

Прорезной и отрезной резцы
По этой же причине головка имеет небольшой передний угол.
Отрезные резцы очень похожи на прорезные, но имеют более длинную головку. Более узкая головка делается с целью сократить расход материала при отрезании.
Длина головки должна подбираться по размерам детали и быть несколько больше половины ее диаметра.
При установке прорезных и отрезных резцов нужно тоже быть очень внимательным и точным. Небрежная установка резца, например небольшой его перекос, вызовет трение резца о стенки канавки, брак в работе, поломку инструмента.
Вытачивание узких канавок производится за один проход резца, который подбирается по ширине будущей канавки. Широкие канавки вытачивают в несколько проходов.

Последовательность операций при протачивании широкой канавки
Порядок работы таков: по линейке или другим мерительным инструментам намечают границу правой стенки канавки. Установив резец, протачивают узкую канавку, не доводя резец на 0,5 мм до нужной глубины — остаток для чистового прохода. Затем сдвигают резец вправо на ширину его режущей кромки и делают новую проточку. Выбрав таким образом канавку намеченной ширины, делают окончательный, чистовой проход резца, двигая его вдоль детали.
Установленную в центрах заготовку не следует разрезать до конца: обломившаяся часть может повредить инструмент. Короткую деталь, зажатую в патроне, можно отрезать начисто, пользуясь специальным отрезным резцом со скошенной кромкой.
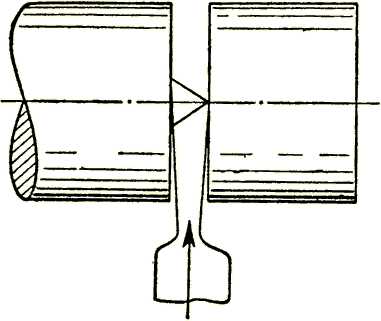
Прорезание детали до центра отрезным резцом со скошенной кромкой
Величина подачи и скорость резания при вытачивании канавок и отрезании должны быть меньше, чем при обработке цилиндров, потому что жесткость проходных и отрезных резцов не велика.
Вытачивание конусов
В практике юного токаря вытачивание конусов будет встречаться реже, чем другие работы. Наиболее простой способ— точение небольших конусов (не более 20 мм) специальным широким резцом.
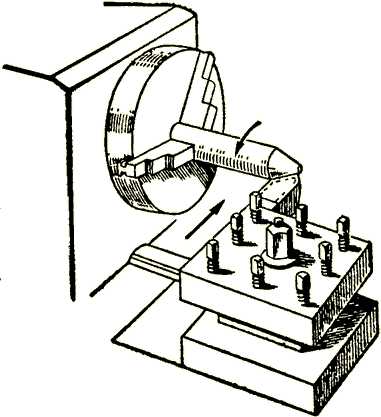
Вытачивание конуса широким резцом
При изготовлении наружного или внутреннего конуса на детали, закрепленной в патроне, пользуются другим приемом. Повернув верхнюю часть суппорта на угол, равный половине угла конуса при его вершине, протачивают деталь, двигая резец с помощью верхних салазок суппорта. Так точат относительно короткие конусы.
Для изготовления длинных и пологих конусов нужно сместить задний центр, передвинуть на определенное расстояние к себе или от себя заднюю бабку.

Если деталь закреплена в центрах таким образом, что широкая часть конуса будет у передней бабки, то заднюю бабку следует сместить к себе, и наоборот, при перемещении задней бабки от работающего широкая часть конуса будет находиться слева — у задней бабки.
Этот способ точения конусов имеет серьезный недостаток: вследствие смещения детали происходит быстрый и неравномерный износ центров и центровых отверстий.

Проверка выточки шаблоном
Обработка внутренних поверхностей
Обработка отверстий может производиться различными инструментами, в зависимости от требуемой формы поверхности и точности обработки. На производстве встречаются заготовки с отверстиями, сделанными при отливке, ковке или штамповке. У юного металлиста готовые отверстия будут встречаться главным образом в отливках. Обработку отверстий в сплошных заготовках, не имеющих подготовленных отверстий, всегда придется начинать со сверления.
Сверление и рассверливание
Неглубокие отверстия на токарном станке сверлят перовыми и спиральными (цилиндрическими) сверлами.
Перовое сверло имеет плоскую лопатку с двумя режущими кромками, переходящую в стержень. Угол при вершине сверла обычно имеет 116—118°, однако он может быть, в зависимости от твердости материала, от 90 до 140°— чем тверже металл, тем больше угол. Точность отверстия при обработке перовым сверлом невелика, поэтому его употребляют тогда, когда большой точности не требуется.

Перовое сверло
Спиральные сверла — основной инструмент для сверления. Точность обработки этими сверлами достаточно высока. Спиральное сверло состоит из рабочей и части конического или цилиндрического хвостовика, которым сверло крепится в пиноли задней бабки или в патроне.

Спиральные сверла: а — с коническим хвостовиком; б — с цилиндрическим хвостовиком
Рабочая часть сверла — цилиндр с двумя винтовыми канавками, образующими режущие кромки сверла. По этим же канавкам выводится наружу стружка.
Головка сверла имеет переднюю и заднюю поверхности и две режущие кромки, соединенные перемычкой. Идущие вдоль винтовых канавок фаски направляют и центрируют сверло. Величина угла при вершине спирального сверла одинакова с перовым и может изменяться в тех же пределах. Изготовляются сверла из легированной или быстрорежущей стали. Иногда сверла из легированной стали оснащаются пластинками твердого сплава.

Передняя часть спирального сверла
Закрепление сверла производится двумя способами, в зависимости от формы хвостовика. Сверла с цилиндрическим хвостовиком закрепляются в пиноли задней бабки при помощи специального патрона, сверла с коническим хвостовиком вставляются прямо в отверстие пиноли.

Патрон для закрепления сверл с цилиндрическим хвостовиком
Может случиться, что конический хвостовик мал по своим размерам, не подходит к отверстию. Тогда придется воспользоваться переходной втулкой, которая вместе со сверлом вставляется в пиноль.
Переходная втулка к сверлам с коническими хвостовиками: 1 — хвостовик сверла; 2 — втулка.
Чтобы вытолкнуть сверло из пиноли, нужно вращением маховичка затянуть ее в корпус задней бабки. Винт упрется в хвостовик сверла и вытолкнет его. С помощью специальной державки можно закрепить сверло и в резцодержателе.
При сверлении нужно внимательно следить за тем, чтобы сверло не уводило в сторону, иначе отверстие будет неправильным, а инструмент может сломаться. Подачу сверла производят медленным и равномерным вращением маховичка задней бабки или перемещением суппорта, если сверло с державкой закреплено в резцодержателе.
Высверливая глубокие отверстия, нужно время от времени выводить сверло из отверстия и убирать из канавки стружку.
Глубина отверстия не должна превышать длины рабочей части сверла, в противном случае стружка не будет выводиться из отверстия и сверло сломается. При сверлении глухих отверстий на заданную глубину можно проверять глубину сверления по делениям на пиноли. Если их нет, то отметку ставят мелом на самом сверле. Когда при сверлении слышится характерный визг, это значит, что либо сверло имеет перекос, либо оно затупилось. Сверление нужно немедленно прекратить, убрав сверло из отверстия. После этого можно остановить станок, выяснить и устранить причину визга.
Рассверливание — это то же сверление, но сверлом большего диаметра по уже имеющемуся отверстию. Поэтому все правила сверления относятся и к рассверливанию.
Другие методы обработки внутренних поверхностей
В практике юного токаря может встретиться и такой случай, когда диаметр нужного отверстия гораздо больше диаметра самого большого сверла в его наборе, когда в отверстии нужно выточить канавку или сделать его конусным. Для каждого из этих случаев существует свой метод обработки.
Растачивание отверстий ведется специальными расточными резцами — черновыми и чистовыми, в зависимости от нужной чистоты и точности обработки. Черновые резцы для проточки глухих отверстий отличаются от черновых резцов для точения сквозных отверстий. Чистовую обработку сквозных и глухих отверстий проводят одним и тем же чистовым резцом.

Расточные резцы: а — черновой для сквозных отверстий; б — черновой для глухих отверстий; в — чистовой
Растачивание имеет свои трудности по сравнению с наружным точением. Расточные резцы обладают малой жесткостью, их приходится значительно выдвигать из резцодержателя. Поэтому резец .может пружинить и гнуться, что, конечно, отрицательно влияет на качество обработки. Кроме того, затруднено наблюдение за работой резца. Скорость резания и величина подачи резца должны быть поэтому меньше, чем при наружной обработке, на 10—20%.
Особую трудность представляет обработка тонкостенных деталей. Зажимая такую деталь в патроне, ее легко деформировать, и резец выберет на вдавленных частях более толстую стружку. Отверстие не будет строго цилиндрическим.

Измерение глубины расточенного отверстия
Для правильной обработки при растачивании резец устанавливается на уровне центров. Затем нужно расточить отверстие на 2—3 мм в длину и замерить диаметр.

Неправильное растачивание детали, сильно зажатой в патроне
Если размер верен, можно растачивать отверстие на всю длину. При растачивании глухих отверстий или отверстий с уступами, так же как и при сверлении, на резце делают мелом отметку, указывающую глубину растачивания.
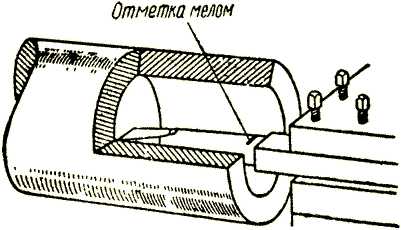
Подрезание внутреннего торца

Вытачивание внутренней канавки
Подрезание внутренних торцов производится подрезными резцами, а вытачивание внутренних канавок — специальными прорезными канавочными резцами, у которых ширина режущей кромки в точности соответствует ширине канавки. Резец устанавливается на соответствующую глубину по меловой риске на теле резца.
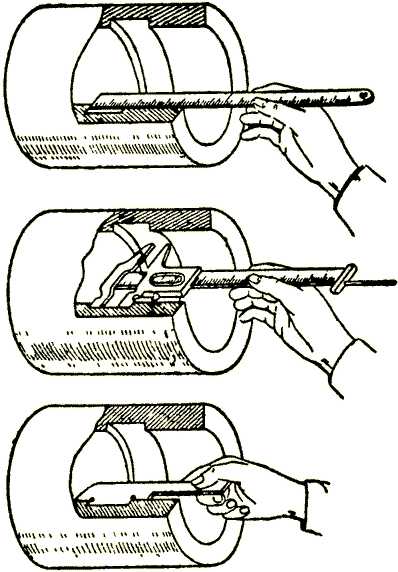
Измерение внутренней канавки: линейкой, штангенциркулем и шаблоном
Кроме расточных резцов, для растачивания цилиндрических отверстий употребляются зенкеры. Они похожи на спиральные сверла, но имеют три или четыре режущие кромки и не годятся для получения отверстий в сплошном материале.
Спиральные хвостовые зенкеры: а — из быстрорежущей стали; б — с пластинками из твердого сплава
Очень чистые и точные цилиндрические отверстия делают развертками. Оба эти инструмента применяют не для расширения отверстия, а для подгонки под точный размер и форму.

Развертки: а — хвостовая; б — назадная
Изготовление конических отверстий
Вытачивание внутренних конусов, пожалуй, наиболее трудное дело. Обработка ведется несколькими способами. Часто конические отверстия делают растачиванием резцом с поворотом верхней части суппорта.
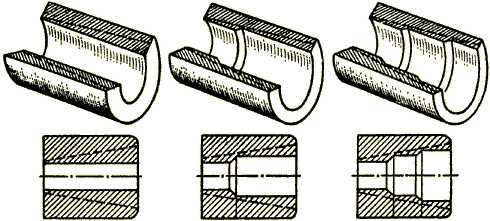
Высверливание ступенчатого отверстия под конус
В сплошном материале предварительно нужно высверлить отверстие. Для облегчения растачивания можно высверлить ступенчатое отверстие. Следует помнить, что диаметр сверла нужно подбирать с таким расчетом, чтобы оставался припуск в 1,5—2 мм на сторону, который затем снимается резцом. После точения можно воспользоваться коническим зенкером и разверткой. Если уклон конуса невелик, сразу же после сверления применяют набор конических разверток.

Изготовление конического отверстия набором разверток
Последняя из основных операций, производимых на токарном станке, — нарезание резьбы.
Механическое изготовление резьбы возможно только на специальных винторезных станках. На простых станках эта операция производится вручную. Приемы ручного изготовления наружной и внутренней резьбы изложены выше.
Измерительный инструмент
В токарных работах используется тот же инструмент, что и при слесарной обработке: стальная линейка, кронциркуль, штангенциркуль и другие. О них уже было сказано раньше. Новыми здесь могут быть различные шаблоны, которые юный мастер будет изготовлять сам. Они особенно удобны при изготовлении нескольких одинаковых деталей.
Помните, что все измерения можно производить только после полной остановки станка. Будьте осторожны! Не производите замеров вращающейся детали!
Меры предосторожности
При работе на токарном станке нужно руководствоваться следующими правилами:
1) начинать работать на станке можно только после детального ознакомления со станком и методами обработки;
2) не работать на неисправном станке или негодным (тупым) инструментом;
3) прочно закреплять деталь и следить за исправностью ограждающих устройств;
4) не работать в свободной одежде: рукава завязывать у кисти, длинные волосы прятать под головной убор;
5) своевременно убирать стружку и следить за порядком на рабочем месте;
6) не останавливать руками вращающийся патрон;
7) в случае неисправности немедленно выключить станок.

Применение защитного щитка при точении
Уход за станком
Чем тщательнее уход за станком, тем лучше и дольше он будет работать. Это простое правило следует твердо запомнить и аккуратно его выполнять. Уход за токарным станком сводится к следующему.
Основное — это смазка всех трущихся частей. Перед началом работы необходимо осмотреть станок и проверить, достаточно ли смазки. Наиболее внимательно нужно следить за смазкой подшипников, заполняя масленки и смазочные отверстия машинным маслом. Станок в это время, во избежание несчастного случая, должен быть остановлен.
После работы нужно вычистить станок, убрать стружку, протереть направляющие станины и суппорта, и смазать их тонким слоем масла.
Абсолютно чистыми должны быть и конические отверстия шпинделя и пиноли задней бабки. Точность работы станка будет зависеть от их хорошего состояния.
До начала работы нужно также проверить состояние приводного ремня. Его нужно оберегать от масляных брызг и капель, так как замасленный ремень проскальзывает и быстро срабатывается. Натяжение ремня должно быть не слишком сильным, но и не слишком слабым: слабо натянутый ремень проскальзывает, а при сильном его натяжении сильно греются и быстро изнашиваются подшипники. Ограждение приводного ремня тоже должно быть в порядке.
Автор: П.В. Леонтьев
Читайте еще:
www.sdelaysam.info
Токарный станок по металлу: конструкция, параметры при обработке
Устройство самого современного станка для токарных работ несмотря на многовековую историю развития и сегодня не сильно отличается от своих прародителей. Практически все приспособления по-прежнему основаны на принципе вращения обрабатываемой детали, зажатой в патрон с одной стороны, и заднюю бабку с другой. Такая компоновка применяется и для деревообрабатывающих станков, и для оборудования для обработки металла. При этом, токарный станок по металлу, несмотря на сложность конструкции, вполне реально собрать и в гаражных условиях, ведь, как показывает практика, ничего невозможного нет.
Теория станков и оборудования насчитывает несколько видов устройств для обработки металла которые могут именоваться токарным станком. Самым простым является токарно-винторезный вид устройства, в основе которого лежит принцип вращения обрабатываемой детали вокруг своей оси в горизонтальной плоскости. Обработка детали проводится резцом или другим приспособлением, рабочая часть которого способна передвигаться как вдоль детали, так и перпендикулярно оси вращения. Само устройство токарного станка по металлу имеет ряд элементов, имеющих специальное название, эти названия идентичны для всех конструкций оборудования.
Основные узлы
В состав конструкции входит два вида узлов те, без которых невозможна работа называются основными, те, которые можно опустить при создании или которые могут быть выполнены в виде дополнительного оборудования обычно именуются неосновными.
Станина
Станина самая массивная часть станка. Она выступает в роли несущей рамы, на нее крепится все оборудование. Это, должно быть массивное и прочное сооружение, по весу станина может достигать 70% массы станка. Вместе с тем, все элементы корпуса станины должны быть максимально точно подогнаны друг к другу и иметь жесткую фиксацию. Большая масса способствует уменьшению вибрации при работе, а точность дает возможность повысить качество обработки детали.
Суппорт токарного станка
Один из самых важных и сложных узлов. В промышленных моделях суппорт имеет несколько регулировок, позволяет перемещать резцедержатель как вдоль оси вращения детали, так и перпендикулярно ей. Подача резца может иметь и вертикальное направление. Для токарного станка, изготавливаемого своими руками этот узел обычно конструируют упрощенным – резец передвигается на салазках только горизонтально, поперек оси вращения детали. Поднятие и опускание осуществляется с последующей фиксацией при выключенном двигателе. А перемещение вдоль оси обычно осуществляется по резьбовой шпильке, установленной вдоль станины.
Вместе с тем, у многих умельцев упрощенная конструкция встречается только в первой собранной модели, в дальнейшем суппорт постоянно модернизируется и усовершенствуется. Но главной задачей этого узла остается все-таки надежная фиксация режущего инструмента и плавная его подача в ходе работы.
Передняя и задние бабки
Для того чтобы придать вращательное движение детали используется передняя бабка. Это сложная конструкция имеющая в своем составе узел фиксации детали, вал, на который крепится этот узел и коробку передач, для изменения скорости вращения. В промышленных станках коробка передач обслуживает не только вращающийся патрон с зажатой деталью, в ней имеется привод и для подачи суппорта. В мини станках, изготавливаемых своими руками передняя бабка, представляет собой вал с патроном для фиксации детали, с одной стороны, а с другой на него насажен шкив для ременной передачи. Вся эта конструкция помажена на пару подшипников и надежно зафиксирована на станине.
Задняя бабка представляет собой подвижный узел, в который крепится неподвижный конусный центр для поддержания детали на весу. Важным моментом выступает то, что центр задней и передней бабки находятся на одном уровне как в горизонтальной, так и вертикальной плоскости. Эти соосно расположенные детали позволяют с одной стороны обеспечить вращение детали вокруг одной оси, с другой обеспечить выполнение и других технологических операций токарных работ, например, сверление отверстий или нарезание внутренней резьбы.
Коробка подач
В самодельных станках по металлу коробка передач часто конструируется как отдельный узел. Основная задача коробки передач обеспечить вращение шпинделя станка с заданной скоростью в нужном направлении. Коробка передач как уже упоминалось раньше может иметь привод еще и на суппорт, эта опция особенно важна при нарезке резьбы и получении максимально качественной обработанной поверхности. Конструктивно коробка может быть выполнена:
- В виде нескольких шестеренок на валах;
- В виде шкивов разного диаметра, на которые движение передается при помощи ременной передачи.
Для мини станков самым простым решением является использование двухскоростной электродрели в качестве привода – здесь в одном корпусе сразу совмещены и двигатель, и коробка передач.
Шпиндель
Шпиндель предназначен для надежной фиксации обрабатываемой заготовки. В таком токарном станке эту роль может выполнять:
- Токарный патрон промышленного производства;
- Планшайба;
- Цанговый патрон;
- Патрон от электродрели;
- Другие виды зажимных устройств.
Другие конструктивные элементы
Перечень узлов и элементов, предназначенных для обеспечения работы самодельного токарного станка по металлу может иметь много пунктов, но наиболее важные в нем будут:
- Салазки;
- Пиноль;
- Резцедержатель;
- Фартук.
Салазки
Салазки предназначены для плавного перемещения резцедержателя. Для самодельных мини станков обычно используются только поперечные салазки, по которым при вращении маховика происходит плавное движение резцедержателя перпендикулярно оси вращения шпинделя. Продольное движение осуществляется при помощи суппорта. Такое решение не дает возможности выполнять большое количество операций, поэтому при конструировании станка стоит предусмотреть еще и поперечные для более точной работы. Ну а для станков, претендующих на высокий результат, не помешают устройства для перемещения резца под углом в 45 градусов к оси вращения.
Пиноль
Используется для закрепления заготовки в задней бабке. Эта деталь должна иметь высокую прочность и надежность, поскольку испытывает постоянное трение о металл заготовки.
Резцедержатель
Назначение резцедержателя – фиксация режущего инструмента на салазках суппорта. В процессе работы в этот узел могут фиксироваться и другие типы инструмента, например, накатки и шарошки. Резцедержатель должен обеспечивать, с одной стороны, надежное крепление резца, а с другой, оперативное изменение положение инструмента относительно обрабатываемой поверхности.
Фартук
Назначение этого элемента конструкции – сбор металлической стружки. Он располагается под станиной и при обработке металла стружка падает на фартук, а не на пол.
Электрическое оснащение станка
К электрооборудованию токарно-винторезного станка относится основное оборудование – электродвигатель с пусковыми конденсаторами и блоком защиты. И вспомогательное электрооборудование – лампа освещения и другие элементы, например, вытяжной вентилятор.
Особе внимание в электрооборудовании следует уделить приборам защиты от поражения электрическим током. Здесь прежде всего необходимо установить реле защиты, сделать вывод защитного заземления и обеспечить пульт управления специальной большой кнопкой выключения электропитания. Наличие этих защитных устройств в составе электрооборудования важное требование правил техники безопасности при работе с таким травмоопасным оборудованием.
Процесс изготовления токарного станка по металлу своими руками, как и процесс промышленного производства имеет несколько этапов. Каждый этап по-своему важен, как важна и последовательность этапов при создании конструкции.
Начальный этап – проектирование. Он начинается с разработки концепции компоновки устройства, его технических параметров и создания технической документации.
Этап практического изготовления включает в себя разметку материала, резку, подгонку и создание первоначальной модели. Далее, идет процесс наладки и подгонки узлов и деталей. Так что говорить о конкретных сроках, за которые можно самостоятельно собрать рабочий токарный станок своими руками не стоит.
Проектирование и чертежи настольного токарного станка
Проектирование подобного рода изделий рекомендуется делать на основе тех задач, которые планируется выполнять на это оборудовании. Чаще всего за основу берутся простые, не требующие высокой квалификации и дорогостоящего оборудования виды работ:
- Гладкая черновая и чистовая обработка цилиндрических деталей;
- Точение ступенчатых фасонов заготовок;
- Обработка конусных поверхностей;
- Формирование уступов, канавок с прямыми и наклонными поверхностями;
- Расточка цилиндров и конусов;
- Нарезание различного вида резьбы;
- Обработка кромок отверстий;
- Формирование рифлёной поверхности;
- Отрезание заготовок.
Определяем необходимые размеры
Вторым важным моментом выступает то, каких размеров заготовки будут обрабатываться при помощи этого станка. Для того чтобы заниматься моделированием достаточно небольших размеров, этот вариант мини станка может иметь небольшие размеры, и целиком помещаться на обычном письменном столе.
Для оборудования, которое планируется применять для обработки заготовок диаметром 50 мм и длиной до 500 необходима будет станина минимальной длины в 750 мм. А для работы с заготовками большей длины потребуется еще и отдельное основание. Простой деревянный стол устройство массой 50-70 кг попросту не выдержит.
Создаем необходимую проектную документацию
Увы, без разработки чертежей при постройке станка своими руками не обойтись. В принципе профессионально вычерчивать все узлы и детали смысла нет, а вот сделать технический рисунок, в котором учесть расположение деталей, способ их соединения и крепления все-таки стоит. При разработке отдельно нужно просчитать размеры станины и всех деталей, которые будут собираться из металлопроката. На рисунках нужно отметить точки соединений, места сверления отверстий и способ фиксации отдельных подвижных узлов. В качестве отдельного документа нужно оформить кинетическую схему станка и схему подключения электрооборудования. Кинетическая схема подразумевает то, как будут расположены шестерни или шкивы коробки передач, и как будет осуществляться изменение скорости вращения шпинделя. А электрическая схема даст возможность правильно подключить электрооборудование.
Совет: отличным подспорьем в качестве наглядного пособия по разработке чертежей могут служить старые советские технические журналы для технического творчества.
Именно в них часто публиковались чертежи оборудования для оснащения домашней мастерской.
Выбор электродвигателя для станка
Среди узлов самодельного станка электродвигатель один из немногих элементов который все-таки придется приобретать в уже собранном виде. Для оснащения маломощных мини-станков для моделирования и несложных работ подойдут небольшие электродвигатели мощностью до 500 вт. Более мощные и высокооборотистые типы двигателей можно устанавливать на станки для серьезных гаражных работ. А вот что касается типа мотора, то здесь лучше отдать предпочтение асинхронным видам. Они надежны, неприхотливы к перепадам напряжения и изменению нагрузки при работе.
Двигатель от стиральной машинки
Использование двигателя от стиральной машины в самодельном металлообрабатывающем станке дает несколько преимуществ – эти моторы доступны, имеют большой ресурс, отдельные модели можно использовать с установленными на них шкивами. Двигатели от современных стиральных машин, кроме всего прочего, можно использовать с автоматическим регулятором оборотов, это упростит конструкцию, поскольку не потребуется мудрить над коробкой передач.
Токарный станок на основе дрели
Для небольших работ в формате настольного токарного станка может подойти и бытовая электродрель. Преимущество этой простой конструкции в том, что узел передней бабки имеет уже готовый вид с регулятором оборотов, переключателем скоростей (для двухскоростных моделей) и патроном для зажима заготовки. Минус этого варианта заключается в том, что фиксировать можно детали максимального диаметра 10 или 13 мм, это максимальный размер детали, которые можно зажать в сверлильном патроне.
2.3. Порядок сборки
Сборка узлов и механизмов станка производится в определенном порядке, позволяющем постепенно собрать нужную конструкцию и при этом в процессе работы избежать крупных ошибок. Рекомендуется начинать работы со сборки основания рабочего стола, станины и суппорта, передней и задней бабки, резцедержателя и установки дополнительного оборудования.
Рама стола
Настольный вариант токарного станка по металлу рекомендуется собирать на специально изготовленном для этого столе. Рамная конструкция из уголка 40х40 или 45х45 отлично выдержит массу станка в 50 и даже 70 кг. В качестве крышки лучше использовать массивную доску из твердых пород дерева толщиной 50 и более мм. Раму стола лучше сразу фиксировать сварным швом.
Станина и суппорт
Станину для небольших станков можно сделать из профильной или обычной толстостенной водопроводной трубы. Для массивных проектов, с мощным двигателем и патроном диаметром 100мм станину лучше собрать из тавра или швеллера.
Суппорт лучше сделать из массивного швеллера. Втулки для движения по направляющим изготавливаются из бронзы, а вот для перемещения суппорта привариваются усиленные гайки. При опоре суппорта на станину делается широкая шлифованная подошва. Поверхность скольжения смазывается литолом или солидолом.
Изготавливаем переднюю и заднюю бабки
Сборка этих узлов требует особой точности и аккуратности. Перед сборкой передней бабки проверяется параллельность оси вала и горизонтальной плоскости станины. Вал не должен иметь ни горизонтального ни вертикального биения. Подшипники жестко насаживаются на вал и также фиксируются на корпусе. Вращение вала должно иметь легкое и свободное. Корпус передней бабки лучше собрать из швеллера, при этом предусмотреть возможность доступа к подшипникам для смазки.
Задняя бабка проверяется на точность по центру пиноли и зажимного патрона. Корпус можно выполнить из профильной трубы. Фиксация пиноли осуществляется при помощи зажимных болтов.
Резцедержатель своими руками
Для резцедержателя нужно использовать металлические пластины толщиной не менее 10 мм. Классическая форма резцедержателя квадратная, сам резец фиксируется прижимными болтами. А собранный держатель прикрепляется к салазкам большим болтом, с приваренной к головке рукояткой.
Направляющие для станка
Направляющие могут быть выполнены из трубы диаметром 15 мм, квадрата 10х10 мм или круглого прута. В качестве вала подачи суппорта и салазок можно использовать шпильки диаметром 18 мм и более.
Что нужно учесть во время сборки?
Для всех видов самодельных станков использование сварных соединений используется как самое надежное. Однако при работе электросваркой металл может деформироваться, из-за чего точность может быть нарушена. Для того чтобы сварка была прочной и правильной рекомендуется сначала сделать несколько пробных швов и только после проверки приступать к окончательному соединению деталей.
Особенности работы на самодельных станках
Для успешной работы на любом оборудовании прежде всего необходим опыт. Поэтому прежде чем приступать к обработке ответственных деталей рекомендуется сначала опробовать оборудование и приспособления станка для простых изделий. Ведь обработка сложной детали, как правило, состоит из ряда простых операций выполнение которых позволяет получить из простой заготовки деталь сложной формы.
Техника безопасности
Приступая к работе нужно:
- Убедится в правильности установки заготовки и надежности фиксации резца;
- Проверить, что убраны все инструменты и посторонние вещи;
- Одеть защитные очки и опустить защитное стекло.
Во время работы:
- Нельзя прикасаться к вращающимся деталям;
- Снимать очки и убирать защитное стекло;
- Останавливать шпиндель рукой.
После окончания работ нужно обязательно обесточить станок и дополнительное оборудование.
Правильный уход за станком
Уход за оборудованием не требует сложных приспособлений и операций. Достаточно взять за правило работать заточенным инструментом, убирать после работы стружку и пыль, проводить хотя бы раз в месяц смазку трущихся поверхностей и если это необходимо менять масло в коробке передач станка.
vseochpu.ru
Работа на токарном станке или управление токарным станком
Эта статья посвящена правилам и технике управления токарным станком. От соблюдения правил работы на токарном станке зависит ваша безопасность. Уверенная техника управления токарным станком влияет на качество изделия и производительность управляемых работ. Если ваша цель узнать больше о токарном деле, следуйте руководству.
Шаг 1. Проверка токарного станка перед пуском
Прежде, чем запустить токарный станок, должен быть произведен допусковой контроль, а именно:
- При сменной работе на производстве сменщик, передающий вам токарный станок, обязан доложить о замеченных в нем неполадках (устно, письменно, по телефону). Отсутствие замечаний подразумевает, что токарный станок находится в исправном состоянии.
На производстве устранением неисправностей токарного станка занимается ремонтная служба. Станочник должен только информировать их об возникновении неисправности.
Перед включением токарного станка в электропитание убедитесь:
- Что на станке нет какого-либо предупреждения, типа (токарный станок в ремонте не включать);
- Кожухи, дверки, люки, которые закрывают основные детали, и механизмы токарного станка должны быть закрыты.
- Рукоятки управления шпинделем, подачами, маточной гайкой должны находятся в нейтральном положении.
- Подача охлаждения выключена, сопла подачи жидкости направлены вниз.
- Частоты оборотов и шаги подач установлены такие, какими вы их хотите увидеть, после запуска шпинделя.
- Установленная вами деталь, которую следует обработать должна быть надежна закреплена.
- Пол возле токарного станка должен быть чистым, а под ногами не должно быть лишних предметов.
- Одежда токаря должна быть аккуратно (без свисающих лоскутов).
- Не забыть ключ в патроне (всегда следить за выемкой ключа из патрона).
Выполнив допусковой контроль: включаем главный рубильник токарного станка, дополнительные включатели, если такие имеются. Далее проводится смазка токарного станка.
Шаг 2. Управление шпинделем.
Перед запуском шпинделя или главного двигателя, обязательно убеждаемся, что у вращающихся элементов на нем, в частности патрона, не будет препятствий вращению со стороны неподвижных частей станка. Особую опасность при запуске шпинделя на высоких оборотах представляют собой выступающие за его пределы тонкие прутковые заготовки.
Также это касается деталей больших диаметров со значительным вылетом из патрона и не поджатым с другого конца центром задней бабки.
Как уже говорилось в первом уроке «Устройство токарного станка», настройки частот оборотов шпинделя производят установкой переключателей и рычагов на его узлах в определенное положение согласно таблице, расположенной на станке.
Правила переключение можно обобщить так – «Нельзя переключать или доводить до конца переключения, если таковые вызывают характерный звук не входящих в зацепление зубьев шестерен. В таком случае нужные переключения следует делать при полной остановке.
На всех токарных станках прямые обороты включаются подачей рукоятки включения на себя, а обратные от себя. У рукоятки с вертикальным ходом (на себя это вверх), а у рукоятки с горизонтальным перемещением (на себя это соответственно вправо).
Прямые обороты на всех токарных станках соответствуют вращению шпинделя по часовой стрелке, если смотреть с задней стороны шпинделя. Торможение шпинделя на высоких оборотах за счет реверсирования фрикционов или обратной тяги главного двигателяэто недопустимо, так как ведет к перегрузке и перегреву механизма. Торможение должно выполняться тормозом. А если эффективности тормоза недостаточно, то ее следует восстановить регулировкой или ремонтом.
Для крепления в трехкулачковом патроне деталей обычно используется одно гнездо «0» для введения в него ключа, что требует установки этого гнезда в верхнее положение зажима и отжима. В станках с механическим фрикционом это действие (при некоторых навыках) можно выполнять рукояткой управления фрикционов.
При обработке резцом нельзя останавливать шпиндель при включенной подаче и не отведенном от детали резце (это приводит к поломке резца).
Шаг 3. Управление подачей токарного станка
Ручное управление подачей станка подразумевает подачу инструмента на небольшие длины (при обработках, настройках, подводках).
Ручное управление подачей позволяет быстро вести, прерывать и возобновлять подачу, а также мгновенно изменять ее скорость (в зависимости от изменения условий и ситуаций обработки). Ручная подача в продольном направлении приводится маховиком с горизонтальной ручкой или без нее. Вращение маховика против часовой стрелки приводит движение суппорта влево, а по часовой стрелке вправо.
Продольное перемещение суппорта на токарном станке осуществляется за счет шестеренно реечной передачи. У таких передач есть люфты или зазоры в контактах деталей и ее механизмах.
Ручное управление поперечной подачей (выполняется Т-образной рукояткой с горизонтальной ручкой). Вращение рукоятки по часовой стрелке подает салазки инструмент вперед, то есть от себя, вращение рукоятки против часовой стрелки подает инструмент к себе. На нашем станке есть ускоренное включение перемещения салазок. Существуют разные техники вращения маховика одной и двумя руками, которые применяются в зависимости от выполняемой работы на токарном станке.
Подача верхними салазками
На верхних салазках вращение рукоятки по часовой стрелке двигает салазки вперед, а вращение против часовой стрелки назад. Быстрое холостое перемещение таких рукояток можно делать за одну из ручек. При этом салазки должны быть отрегулированы на легкое перемещение. Более подробно о регулировке механизмов, салазок, токарного станка мы рассмотрим в следующем уроке по токарному делу.
Шаг 4. Управление механическими подачами
Механические подачи работают от привода через ходовой вал, а управление ими делается ручкой 4-х позиционного переключателя. Направление перемещение рукоятки переключателя соответствует направлению движения инструмента на суппорте.
Перед включением механической подачи в любом направлении нужно визуально убедиться в отсутствии у всех точек суппорта препятствий со стороны других узлов станка особенно вращающихся. Частой оплошностью начинающих токарей является попытка приблизить суппорт к патрону при сдвинутых вправо салазок, что приводит к сталкиванию. Поэтому следует проверять беспрепятственное перемещение суппорта заранее.
Нужно отработать техники ручной подачи так, чтобы не происходила остановка резца или остановка была минимальной.
Шаг №5. Ускоренная подача токарного станка
На станках имеющих ускоренную подачу необходимо соблюдать такие требования:
- Для исключения случайного нажатия кнопки ускоренной подачи управление рычагом переключения подач необходимо производить приложением руки сбоку, но не сверху.
- До пуска ускоренной подачи нужно надежно убедиться в отсутствии препятствий для продвижения у любых точек на суппорте, в том числе и у инструмента, в направлении, куда вы хотите подать.
- Нельзя применять ускоренную подачу для коротких перемещений, особенно при подводам к вращающимся элементам.
- Тяжелые суппорты средних станков имеют инерцию, которую усиливается при ускоренной подаче механизмом его привода.
Бывают совмещенные подачи токарных станков (по виду привода, по направлениям). Такие токарные станки применяются для обработки неответственных конусов (неответственных фасок) и фасонных поверхностей.
Резьбовые подачи
Для нарезания резьб подача суппорта проводится за счетсмыкания маточной гайки с ходовым винтом. Включение и выключения маточной гайки делается отдельным рычагом. Шпиндель и ходовой винт вне зависимости от настроенного шага резьбы вращаются синхронно. Изменения направления вращения шпинделя приводит к изменению направления движения суппорта. Также изменение частоты вращения шпинделя приводит к изменению скорости перемещения суппорта. Попадание резца в ранее нарезанную канавку обеспечивается синхронизацией вращения шпинделя и ходового винта и соответственно хода суппорта.
Можно нарезать, как правую, так и левую резьбу с помощью переключателя на передней бабке, который изменяет направление движения винта относительно шпинделя. При нарезании резьб, не рекомендуется увлекаться высокими оборотами шпинделя, так как его вращение напрямую связано с перемещением суппорта.
Управление задней бабкой токарного станка
Фиксация задней бабкой токарного станка выполняется рычагом, по мере рабочего хода которого, нарастает усилие прижима. При обработках с большими нагрузками, требующей лучшей фиксации задней бабкой воздействие на рычаг должно быть энергичным. Важно не спутать сопротивление рычага при зажиме с его жестким упором в конце рабочего хода. Когда задняя бабка используется с минимальными нагрузками, ее максимальная фиксация со станиной не нужна. Зажим задней бабки рационально соизмерять с предстоящей нагрузкой.
Пиноль задней бабки приводится ручной подачей путем вращения маховика. Закрепление инструмента и приспособлений в конусе пиноли производится в следующем порядке:
- Проверка конусов пиноли и инструмента на отсутствие загрязнений;
- Введение наружного конуса в конус пиноли и нахождение положения совпадения разъема замка в пиноли с лапкой на конусе инструмента (для инструментов, не имеющих лапки, не требуется).
Управление резцедержателем
Резцедержатель представляет из себя, достаточно точный механизм, обеспечивающий жесткость крепления резца в заданных позициях. Правильное положение рукоятки резцедержателя в зажатом виде должно соответствовать положению часовой стрелки на 3-4 часа. Это положение обеспечивается положением проставной шайбы под гайкой рукоятки резцедержателя. Зажим рычага производится средним локтевым усилием. А отжис рукоятки нельзя делать давлением своего веса во избежание потери веса. Отжим рукоятки делается одним или несколькими короткими толчками основанием ладони в направлении против часовой стрелки. Перед поворотом резцедержателя убедитесь в отсутствии препятствий для него самого и закрепленного в нем инструмента. Большую опасность представляют препятствия со стороны вращающихся элементов станка.
Неисправности токарного станка
В процессе работы любому токарю рано или поздно придется столкнутся с непредвиденными ситуациями при работе на токарном станке.
Возможные ситуации при работе на токарном станке:
- Самопроизвольная остановка токарного станка во время работы, во время отключения электропитания или механической неисправности;
- Сталкивания вращающихся элементов с элементами суппорта;
- Проворот детали в патроне;
- Вырыв детали из зажимных приспособлений токарного станка;
Неисправности токарного станка могут быть выражены в посторонних шумах, запахом горящей электропроводки и т.д.
Отлучатся от токарного станка запрещено (нельзя оставлять токарный станок без внимания).
Для экстренной остановки обработки детали следует быстро отвести резец от детали, отключить подачу, остановить шпиндель и выключить главный двигатель. При остановке шпинделе главное не включить обратные обороты, а включить именно нейтральное положение. О неисправностях токарного станка следует сразу же доложить руководству.
www.autoezda.com
История токарного станка
История относит изобретение токарного станка к 650 гг. до н. э. Станок представлял собой два соосно установленных центра, между которыми зажималась заготовка из дерева, кости или рога. Раб или подмастерье вращал заготовку (один или несколько оборотов в одну сторону, затем в другую). Мастер держал резец в руках и, прижимая его в нужном месте к заготовке, снимал стружку, придавая заготовке требуемую форму. Позднее для приведения заготовки в движение применяли лук со слабо натянутой (провисающей) тетивой. Тетиву оборачивали вокруг цилиндрической части заготовки так, чтобы она образовала петлю вокруг заготовки. При движении лука то в одну, то в другую сторону, аналогично движению пилы при распиливании бревна, заготовка делала несколько оборотов вокруг своей оси сначала в одну, а затем в другую сторону. В XIV — XV веках были распространены токарные станки с ножным приводом. Ножной привод состоял из очепа — упругой жерди, консольно закрепленной над станком. К концу жерди крепилась бечевка, которая была обернута на один оборот вокруг заготовки и нижним концом крепилась к педали. При нажатии на педаль бечевка натягивалась, заставляя заготовку сделать один — два оборота, а жердь — согнуться. При отпускании педали жердь выпрямлялась, тянула вверх бечевку и заготовка делала те же обороты в другую сторону. Примерно к 1430 г. вместо очепа стали применять механизм, включающий педаль, шатун и кривошип, получив, таким образом, привод, аналогичный распространенному в XX веке ножному приводу швейной машинки. С этого времени заготовка на токарном станке получила вместо колебательного движения вращение в одну сторону в течение всего процесса точения. В 1500 г. токарный станок уже имел стальные центры и люнет, который мог быть укреплен в любом месте между центрами.
На таких станках обрабатывали довольно сложные детали, представляющие собой тела вращения, — вплоть до шара. Но привод существовавших тогда станков был слишком маломощным для обработки металла, а усилия руки, держащей резец, недостаточными, чтобы снимать большую стружку с заготовки. В результате обработка металла оказывалась малоэффективной. необходимо было заменить руку рабочего специальным механизмом, а мускульную силу, приводящую станок в движение, более мощным двигателем. Появление водяного колеса привело к повышению производительности труда, оказав при этом мощное революционизирующее действие на развитие техники. А с середины XIV в. водяные приводы стали распространяться в металлообработке. В середине XVI Жак Бессон (умер в 1569 г.) — изобрел токарный станок для нарезки цилиндрических и конических винтов. В начале XVIII века Андрей Константинович Нартов (1693-1756), механик Петра Первого, изобретает оригинальный токарно-копировальный и винторезный станок с механизированным суппортом и набором сменных зубчатых колес. Чтобы по-настоящему понять мировое значение этих изобретений, вернемся к эволюции токарного станка. В XVII в. появились токарные станки, в которых обрабатываемое изделие приводилось в движение уже не мускульной силой токаря, а с помощью водяного колеса, но резец, как и раньше держал в руке токарь. В начале XVIII в. токарные станки все чаще использовали для резания металлов, а не дерева, и поэтому проблема жесткого крепления резца и перемещения его вдоль обрабатываемой поверхности стола весьма актуальной. И вот впервые проблема самоходного суппорта была успешно решена в копировальном станке А. К. Нартова в 1712 г.
К идее механизированного передвижения резца изобретатели шли долго. Впервые эта проблема особенно остро встала при решении таких технических задач, как нарезание резьбы, нанесение сложных узоров на предметы роскоши, изготовление зубчатых колес и т.д. Для получения резьбы на валу, например, сначала производили разметку, для чего на вал навивали бумажную ленту нужной ширины, по краям которой наносили контур будущей резьбы. После разметки резьбу опиливали напильником вручную. Не говоря уже о трудоемкости такого процесса, получить удовлетворительное качество резьбы таким способом весьма трудно. А Нартов не только решил задачу механизации этой операции, но в 1718-1729 гг. сам усовершенствовал схему. Копировальный палец и суппорт приводились в движение одним ходовым винтом, но с разным шагом нарезки под резцом и под копиром. Таким образом было обеспечено автоматическое перемещение суппорта вдоль оси обрабатываемой заготовки. Правда, поперечной подачи еще не было, вместо нее было введено качание системы «копир-заготовка». Поэтому работы над созданием суппорта продолжались. Свой суппорт создали, в частности, тульские механики Алексей Сурнин и Павел Захава. Более совершенную конструкцию суппорта, близкую к современной, создал английский станкостроитель Модсли, но А. К. Нартов остается первым, кто нашел путь к решению этой задачи. Вообще нарезка винтов долго оставалась сложной технической задачей, поскольку требовала высокой точности и мастерства. Механики давно задумывались над тем, как упростить эту операцию. Еще в 1701 году в труде Ш. Плюме описывался способ нарезки винтов с помощью примитивного суппорта. Для этого к заготовке припаивали отрезок винта в качестве хвостовика. Шаг напаиваемого винта должен был быть равен шагу того винта, который нужно было нарезать на заготовке. Затем заготовку устанавливали в простейших разъемных деревянных бабках; передняя бабка поддерживала тело заготовки, а в заднюю вставлялся припаянный винт. При вращении винта деревянное гнездо задней бабки сминалось по форме винта и служило гайкой, вследствие чего вся заготовка перемещалась в сторону передней бабки. Подача на оборот была такова, что позволяла неподвижному резцу резать винт с требуемым шагом. Подобного же рода приспособление было на токарно-винторезном станке 1785 года, который был непосредственным предшественником станка Модсли. Здесь нарезка резьбы, служившая образцом для изготавливаемого винта, наносилась непосредственно на шпиндель, удерживавший заготовку и приводивший ее во вращение. (Шпинделем называют вращающийся вал токарного станка с устройством для зажима обрабатываемой детали.) Это давало возможность делать нарезку на винтах машинным способом: рабочий приводил во вращение заготовку, которая за счет резьбы шпинделя, точно так же как и в приспособлении Плюме, начинала поступательно перемещаться относительно неподвижного резца, который рабочий держал на палке. Таким образом ни изделии получалась резьба, точно соответствующая резьбе шпинделя. Впрочем, точность и прямолинейность обработки зависели здесь исключительно от силы и твердости руки рабочего, направлявшего инструмент. В этом заключалось большое неудобство. Кроме того, резьба на шпинделе была всего 8-10 мм, что позволяло нарезать только очень короткие винты.
Вторая половина XVIII в. в станкостроении ознаменовалась резким увеличением сферы применения металлорежущих станков и поисками удовлетворительной схемы универсального токарного станка, который мог бы использоваться в различных целях. В 1751 г. Ж. Вокансон во Франции построил станок, который по своим техническим данным уже походил на универсальный. Он был выполнен из металла, имел мощную станину, два металлических центра, две направляющие V-образной формы, медный суппорт, обеспечивающий механизированное перемещение инструмента в продольном и поперечном направлениях. В то же время в этом станке отсутствовала система зажима заготовки в патроне, хотя это устройство существовало в других конструкциях станков. Здесь предусматривалось крепление заготовки только в центрах. Расстояние между центрами можно было менять в пределах 10 см. Поэтому обрабатывать на станке Вокансона можно было лишь детали примерно одинаковой длины. В 1778 г. англичанин Д. Рамедон разработал два типа станков для нарезания резьб. В одном станке вдоль вращаемой заготовки по параллельным направляющим передвигался алмазный режущий инструмент, скорость перемещения которого задавалась вращением эталонного винта. Сменные шестерни позволяли получать резьбы с разным шагом. Второй станок давал возможность изготавливать резьбу с различным шагом на детали большей длины, чем длина эталона. Резец продвигался вдоль заготовки с помощью струны, накручивавшейся на центральную шпонку. В 1795 г. французский механик Сено изготовил специализированный токарный станок для нарезки винтов. Конструктор предусмотрел сменные шестерни, большой ходовой винт, простой механизированный суппорт. Станок был лишен каких-либо украшений, которыми любили украшать свои изделия мастера прежде.
Накопленный опыт позволил к концу XVIII века создать универсальный токарный станок, ставший основой машиностроения. Его автором стал Генри Модсли. В 1794 г. он создал конструкцию суппорта, довольно несовершенную. В 1798 г., основав собственную мастерскую по производству станков, он значительно улучшил суппорт, что позволило создать вариант универсального токарного станка. В 1800 г. Модсли усовершенствовал этот станок, а затем создал и третий вариант, содержавший все элементы, которые имеют токарно-винторезные станки сегодня. При этом существенно то, что Модсли понял необходимость унификации некоторых видов деталей и первым стал внедрять стандартизацию резьб на винтах и гайках. Он начал выпускать наборы метчиков и плашек для нарезки резьб. Токарный станок Робертса Одним из учеников и продолжателей дела Модсли был Р. Робертс. Он улучшил токарный станок тем, что расположил ходовой винт перед станиной, добавил зубчатый перебор, ручки управления вынес на переднюю панель станка, что сделало более удобным управление станком. Этот станок работал до 1909 г. Другой бывший сотрудник Модсли — Д. Клемент создал лоботокарный станок для обработки деталей большого диаметра. Он учел, что при постоянной скорости вращения детали и постоянной скорости подачи по мере движения резца от периферии к центру скорость резания будет падать, и создал систему увеличения скорости. В 1835 г. Д. Витворт изобрел автоматическую подачу в поперечном направлении, которая была связана с механизмом продольной подачи. Этим было завершено принципиальное совершенствование токарного оборудования.
Следующий этап — автоматизация токарных станков. Здесь пальма первенства
принадлежала американцам. В США развитие техники обработки металлов началось
позднее, чем в Европе. Американские станки первой половины XIХ в. значительно
уступали станкам Модсли. Во второй половине XIХ в. качество американских
станков было уже достаточно высоким. Станки выпускались серийно, причем
вводилась полная взаимозаменяемость деталей и блоков, выпускаемых одной
фирмой. При поломке детали достаточно было выписать с завода аналогичную
и заменить сломанную деталь на целую без всякой подгонки. Во второй половине
XIХ в. были введены элементы, обеспечивающие полную механизацию обработки
— блок автоматической подачи по обеим координатам, совершенную систему
крепления резца и детали. Режимы резания и подач изменялись быстро и без
значительных усилий. В токарных станках имелись элементы автоматики — автоматический
останов станка при достижении определенного размера, система автоматического
регулирования скорости лобового точения и т.д. Однако основным достижением
американского станкостроения было не развитие традиционного токарного станка,
а создание его модификации — револьверного станка. В связи с необходимостью
изготовления нового стрелкового оружия (револьверов) С. Фитч в 1845 г.
разработал и построил револьверный станок с восемью режущими инструментами
в револьверной головке. Быстрота смены инструмента резко повысила производительность
станка при изготовлении серийной продукции. Это был серьезный шаг к созданию
станков-автоматов. В деревообработке первые станки-автоматы уже появились:
в 1842 г. такой автомат построил К. Випиль, а в 1846 г. Т. Слоан. Первый
универсальный токарный автомат изобрел в 1873 г. Хр. Спенсер.
turner.narod.ru
Токарный станок — принцип работы, описание :: ТОЧМЕХ
Современные токарные станки и токарные обрабатывающие центры.
Все части токарного станка установлены на прочной основе — станине. Та часть станка, которая держит и вращает деталь, называется передней бабкой. В ее корпусе имеется шпиндель со ступенчатым шкивом на одном конце и патроном — на другом. У мощных скоростных станков, которыми оснащены наши заводы, шкив заменен коробкой скоростей. На другом конце станины находится задняя бабка, которая удерживает правый конец детали при обработке в центрах. В верхней части корпуса задней бабки находится пиноль, двигающаяся влево и вправо с помощью маховичка с винтом и гайки.
В коническое отверстие в передней части пиноли вставляется центр. В случае надобности сюда же можно устанавливать сверла, развертки и другой инструмент. Заднюю бабку можно передвигать по направляющим станины, устанавливая ее на нужное расстояние, в зависимости от размеров обрабатываемой детали.
Между передней и задней бабками помещается суппорт с резцедержателем. Нижняя часть суппорта, называемая кареткой или продольными салазками, скользит по направляющим станины, перемещая резец вдоль обрабатываемой детали. Поперечное движение резца осуществляется с помощью поперечных салазок, в верхней части которых помещается поворотная часть суппорта. Она, как и станина, имеет направляющие, по которым двигаются верхние салазки суппорта с резцедержателем. Резцедержатель может быть устроен по-разному, это зависит от величины нагрузки, действующей на резец.
Для хорошего натяжения ремня у легкого настольного станка можно сделать приспособление, изображенное на рисунке. Ролик удерживает ремень в натянутом состоянии с помощью сильной пружины. Длина шпилек, соединяющих основание приспособления, должна быть несколько больше ширины шкива или равна ей. Ролик с боковинами перемещается по одной из шпилек, как по оси.
Современные токарные станки и токарные обрабатывающие центры
Токарные станки уже много веков являются основным производственным оборудованием. По статистике более 60% всех обрабатываемых деталей проходят через токарные станки. В последнее время эта доля стала еще больше — теперь на токарных станках проводится полная обработка деталей, включая фрезерование, сверление, нарезание резьбы и многое другое (например, гидростатическое накатывание). Таким образом, фактически на рынке начинают доминировать токарные обрабатывающие центры.
Токарные центры предназначены для комплексной обработки современным режущим инструментом с высокой скоростью сложных деталей различного профиля за одну установку: токарная, сверлильная, фрезерная обработка в одной операции. В автоматическом цикле на них можно обрабатывать наружные и внутренние поверхности деталей типа тел вращения со ступенчатым и криволинейным профилем: точение, растачивание конических и фасонных поверхностей, подрезка торцов, точение канавок, нарезание резьбы резцами, метчиками, плашками и др. в деталях типа крышек, фланцев, втулок, валиков, коротких осей, мелких корпусов, стаканов. Кромеобычной токарной обработки позволяют обрабатывать внецентровые отверстия (с продольным и поперечным расположением оси), фрезеровать канавки, лыски, криволинейные поверхности и др.
Основные технологические параметры токарных центров
Для современных токарных центров характерно:
- наибольший диаметр и длина обрабатываемой заготовки;
- наибольший диаметр проката, проходящего через отверстие шпинделя;
- диапазоны регулирования главного привода и подач.
Другие статьи по сходной тематике
tochmeh.ru
Итак, токарный станок в наши дни является довольно популярным оборудованием. С его помощью производится различного рода обработка материалов путём заточки или резки. На токарном станке профессиональный рабочий способен выполнить работу любой сложности, будь это обыкновенная обточка поверхности или иная чуть более сложная операция. При этом стоит понимать, что расточке подвергаются детали любой геометрической формы. С его помощью обрабатываются торцы и нарезается резьба любого типа и размера. Помимо относительно простых операций токарные станки могут выполнять операции, которые стоит называть высокоточными. Например, станок может с лёгкостью высверливать отверстия, а также выполнять такие операции как зенковка, снятие фаски, расточка и полировка деталей. Однако, это далеко не все возможности токарного станка. На станок можно крепить дополнительные приспособления и насадки, благодаря которым можно осуществлять фрезеровку и нарезание зубьев. Многие люди просто не понимают, каким образом функционируют такие станки. Об этом чуть подробнее. Головка, которая крепится непосредственно на станок, начинает производить вращательные движения после включения станка работником. Резец, который установлен на насадке, начинает производить необходимую операцию. Движение резца становится возможным за счёт механизма подачи. Станки бывают конечно же разного типа, но именно станки токарной группы обрабатывают внутренние и внешние цилиндрические заготовки. На токарный станок можно установить любую насадку. Теперь стоит немного классифицировать станки токарной группы. Токарно-винторезный станок используется в первую очередь для произведения винторезных работ любой сложности, в которые входят работы по вытачиванию конусов. Их применяют для изготовления деталей с резьбой любого размера и типа. Токарно-винторезный станок способен нарезать модульную и дюймовую резьбу и конечно же метрическую. Их универсальность зашкаливает. Собственно именно поэтому они и пользуются огромной популярностью среди остальной техники данной группы. Особенно широко такое оборудование используется на предприятиях, которые занимаются мелкосерийным производством. При этом стоит отметить, что конструкция всех станков данного типа одинаковая. Как минимум она идентична. Подобные станки достаточно громоздкие и весят достаточно много. Основной вес станка конечно же приходится на огромную станину, выполненную как правило из чугуна. К другим элементам можно отнести переднюю и заднюю бабки, а также шпиндель и коробка, с помощью которой меняется скоростной режим. Вращательное движение, которое собственно и обеспечивает выполнение операции, преобразуется в фартуке. С помощью суппорта можно прикрепить на станок любой режущий инструмент. Суппорт состоит из так называемой каретки, которая в свою очередь с лёгкостью перемещается по направляющим, установленным на станине. Основная характеристика, по которой принято сравнивать станки данной группы – это диаметр обточки, которую и производит станок. При этом немаловажное значение имеет и другой показатель. Каждый станок способен работать с заготовками разных размеров. Ну так вот, по размерам заготовок, которые способно обрабатывать на станке, и делят оборудование. |
zaxvatu.net
Устройство токарного станка по металлу
Статистика утверждает, что 60% всех металлических изделий, деталей и автономных приспособлений, неминуемо проходят стадию обработки на токарных станках. Самый простой токарный станок способен выполнять массу операций на наружных и внутренних поверхностях металлических заготовок, превращая их в готовую деталь с высокой степенью точность. С основами устройства токарных станков по металлу мы сегодня вкратце познакомимся.
Содержание:
- Устройство токарного станка, 6 класс
- Архитектура токарно-винторезного станка по металлу
- Характеристики токарного станка
- Как выбрать токарный станок по металлу
Устройство токарного станка, 6 класс
Основы обработки металлов резанием при помощи механических станков, механическую обработку металлов, каждый изучал еще в школе, правда на минимальном уровне, но все же знаний хватало для того, чтобы производить элементарные операции на простейших токарно-винторезных станках. Устройство токарного станка по металлу — не география, технологические аспекты постоянно совершенствуются, год от года растут требования к станкам и возможности агрегатов.
Поэтому эти знания очень быстро устаревают. К примеру, токарно-револьверный станок с ЧПУ еще лет 20-30 назад был неизведанным механизмом, пришедшим из секретных лабораторий. Сегодня же практически каждый желающий может установит у себя дома любой токарно-винторезный станок самых разных размеров и самых разных конфигураций. Тем не менее, основные узлы и агрегаты остались неизменными, в чем мы сегодня убедимся.
Архитектура токарно-винторезного станка по металлу
Несмотря на то, что первые токарные станки, которые появились в конце 18 века, это были вполне самодостаточные устройства, которые позволяли и обрабатывать металлы на довольно высоком технологическом уровне, нарезать резьбу и выполнять более сложную работу. Первый из них появился в 1794 году и это уже было устройство, практически идентичное тем простым токарно-винторезным станкам, которыми мы пользуемся сегодня.
Основными узлами и элементами токарного станка металлу были и остаются:
- Станина. Основа любого металлорежущего и деревообрабатывающего оборудования. От того, насколько прочная и насколько точно изготовлена станина, зависит качество детали и функциональность устройства. Станина токарного станка должна быть максимально тяжелой, чтобы предотвращать вибрации, смещения, искривления траектории движения режущего инструмента. Масса станины должна быть такой, чтобы поглотить любые вибрации, возникающие по ходу работы на устройстве, а ее конструкция — максимально жесткой, прочной и долговечной.
- Шпиндельная бабка передняя. Основное предназначения шпиндельной бабки — фиксация и обеспечение вращения обрабатываемой детали. Тем не менее, многие станки сконструированы таким образом, что шпиндельная бабка может соединять в себе и коробку передач токарного станка, и устройство подачи обрабатывающей головки или суппорта. Как правило, передняя бабка выполнена в мощном корпусе, который жестко крепится к станине.
- Задняя бабка. Это устройство обеспечивает крепление вращающейся детали соосно шпинделю и должно удерживать деталь в заданных координатах, а при необходимости осуществлять подачу дополнительного оборудования, в зависимости от модификации и типа станка.
- Суппорт. Это один из самых главных узлов токарного станка, независимо от его предназначения и характеристик. Суппорт выполняет важнейшую функцию — он прочно удерживает и подает режущий инструмент в направлении обрабатываемой детали. Суппорт может быть полностью управляемый автоматикой, а может быть ручным. В зависимости от технического решения суппорта, функции токарного станка могут быть совершенно разными. Суппорт может подавать режущий инструмент в нескольких плоскостях сразу, что делает его незаменимым в изготовлении самых сложных деталей.
Вкратце, так выглядит архитектурная схема токарно-винторезного станка по металлу.
Характеристики токарного станка
Основные характеристики токарного станка по металлу должны обеспечить максимально возможное количество функций по обработке металла, при этом станок должен обрабатывать деталь самых разных размеров. В основном, станок по обработке металлов характеризуют такие показатели:
- диаметр обрабатываемой детали;
- длина обрабатываемой детали, обозначающаяся расстоянием между центрами задней и передней бабки;
- максимально возможный диаметр обработки детали, а этот показатель зависит от конструкции суппорта.
Как выбрать токарный станок по металлу
Функциональность металлорежущего оборудования практически ничем не ограничена. При необходимости можно купить и токарно-фрезерный станок, и токарно-револьверный с устройством копировальным и программным управлением. Все зависит от потребности а конкретных деталях и и классе их точности.
Как правило, для домашнего использования покупают или собирают своими руками несложные токарные станки, позволяющие выполнять простейшие, но необходимые операции — проточку валов, изготовление шкивов и конусов, изготовление фасонных деталей, сверление и элементарные фрезеровочные работы. Каждый станок подбирается максимально под потребности, тогда он будет работать в оптимальном нагрузочном режиме и прослужит долго и надежно.
Читайте также Твердотельное реле – принцип работы, Электрорубанки, рейтинг по качеству
Читайте также:
nashprorab.com